Oak Ridge National Laboratory (ORNL) has patented a novel cable-driven construction process in which nozzles can be used to3D printingentire
architecture
objects, while hanging in mid-air. Nicknamed Sky Big Area Additive Manufacturing, or simply “SkyBAAM,” the technology is designed to operate using a cord attached to a spooler, giving users complete spatial control over their end effector movements.
SkyBAAM’s creators say it’s easy to set up and doesn’t require the extensive site preparation currently required when deploying gantry-mounted systems, which “impedes their commercial viability”.
According to a patent document already published at FedInvent, it covers “a cable-driven additive manufacturing system that includes an end effector configured for linear translation within a 3D workspace, an aerial lift via at least a A suspension cable suspends the end effector, multiple base stations are set up below the aerial lift, and control cables run from each base station.”
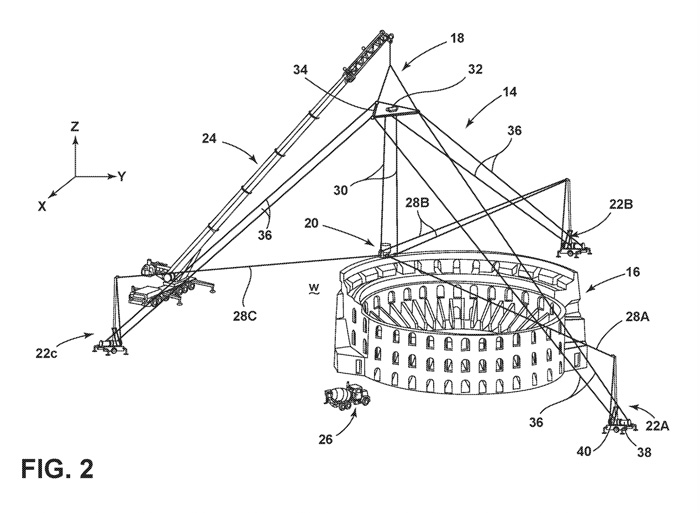
ORNL’s Gantry3D printingalternative plan
In the preamble to its patent, the team behind SkyBAAM demonstrated that the construction of an average family home using traditional processes produces 3-7 tons of concrete waste.In contrast, ORNL engineers say, using3D printing technologyMore sustainable structures with “unique geometries” can be created while using “less material” and
energy
to start.
Many current building systems have nozzles mounted on a gantry, allowing users to adjust the amount of concrete deposit as needed and build structures up to three stories high. For example, using COBOD’s gantry BOD2 printer, PERI Group has previously been able to build a three-story apartment building in Germany, which continues to be listed on the country’s rental market.
ICON also attracted a large number of
invest
Following interest in its Vulcan technology, the company has now raised more than $266 million in funding to support its continued growth. While not attached to a gantry like other architectural 3D printers, even the next-generation Vulcan, due in mid-2021, will have print heads mounted on and moved by parallel base stations.
However, despite the growing interest in such 3D printers, the ORNL team has criticized their complicated setup, which they say is a “barrier to commercial implementation.” Engineers also said the current printed structures were not as “beautiful” as other façade materials, and they could require prolonged reinforcement, necessitating an “improved large-scale, field-deployable” system.
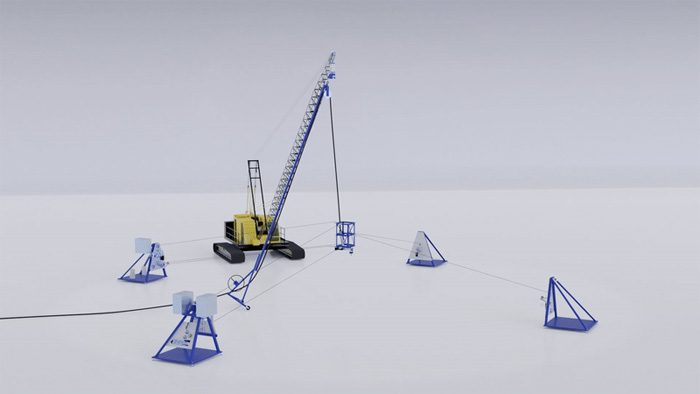
Cable-driven SkyBAAM structure
with traditional concrete3D printerDifferently, the SkyBAAM system outlined in the ORNL patent is designed to operate using a series of pulleys that can be controlled from an on-site base station. At the top of the machine, is a suspended end effector that is said to attach to any cement-compatible nozzle, and a boom capable of carrying a hose to feed it with material.
In practice, SkyBAAM’s inventors say, two of its base stations should be equipped with actuators, such as winders, to move its nozzles into place, and the third acts as a passive base, providing only tension control. However, the researchers also left some wiggle room for customization of the system, including additional workstations, cable guides, or a central controller for automated operation.
According to the machine’s patent, one of the main benefits of switching from a gantry to a cable-mounted setup is that the pulleys can be removably attached, making the latter easier to deploy. What’s more, the system is said to be designed to operate with only three degrees of freedom, compared to the six required for normal cable-driven systems, making it simpler and easier to deploy.
The SkyBAAM 3D printer may still be in the early stages of development, but that hasn’t stopped ORNL from deploying it at an experimental level, and in May 2020, its researchers used the technology to build a first-of-its-kind “smart wall” with built-in electronics that enables It can be used as an energy efficient room cooling system.
“SkyBAAM is unique in that it eliminates the need for a gantry system commonly found in larger additive manufacturing systems,” ORNL researcher Brian Post said at the 2020 unveiling of the “EMPOWER” smart wall. “It can work for hours on a construction site with minimal site preparation.”
Readers can find a complete breakdown of ORNL’s SkyBAAM 3D printing technology under patent number “11230032” here.
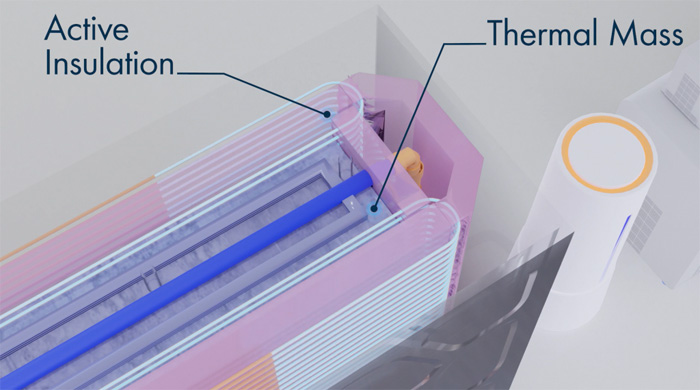
(responsible editor: admin)
0 Comments for “ORNL obtains patent for 3D printing technology of cable hoisting structure building”