Nordic Additive Manufacturing is using
TRUMPF
Five years after the laser metal deposition (LMD) additive manufacturing technology, a form of directed energy deposition (DED), Norway’s Nordic Additive Manufacturing (NAM) was recently interviewed by Norwegian manufacturing magazine Maskinregisteret about using the technology positive results achieved.
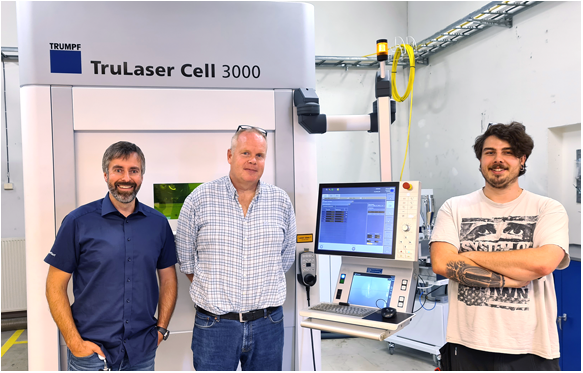
The company started using the process after purchasing a Trumpf TruLaser Cell 3000 in 2017 and is applying the technology to the construction of new parts, repairs, modifications and additions to existing parts.
“Our customers are not only tool manufacturers and
car
In the industry, everyone who makes metal products is a potential customer. Magne Manskow Vik, a member of the NAM team.
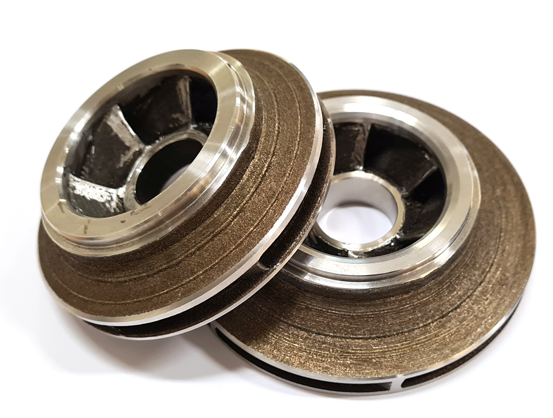
Based on the current results, NAM says that laser-based DED AM restraint should find further applications across the industry, not just the current rather niche applications. Sture Hørli, managing director of NAM, added: “When today’s designers have a good understanding of technology, we have achieved great innovation in terms of innovation.” “You can only speculate on what it is possible and what it will provide. What, but the fact that the introduction of new technologies allows us to manufacture components with entirely new properties will provide huge benefits in the manufacture of small parts, improved processes.”
One of the challenges NAM faced in implementing DED AM was the strict production in Norway
standard
, especially in the oil industry, which has proven difficult to solve because DED is not mentioned in the NORSOK standard. NORSOK Standards are a series of industry standards developed by the Norwegian oil industry to ensure the safety, value-added and cost-effectiveness of oil-related industry development and operations.
“We’re working on getting ISO certification, but that’s not the only obstacle,” Sorli continued. “The LMD (Laser-Based DED) process is not described in the NORSOK standard. Our solution is, we deliver a bespoke product to an industry that doesn’t need it, and then we segment each component delivered to a customer that needs it We do a lot of tests to show our customers the reliability of the product. Our close cooperation with Sintef has yielded good results. In addition, Manulab at NTNU Gjovik also performs CT scans.”
NAM reports that the company has benefited from its owner’s partnership with some industrial giants. Apart from its main owner,
invest
Funds Komm-In, Nammo, Sintef Manufacturing, Norse Industries as and Sparebank are co-owners, Tor Henning Molstad through Molstad Model & Form as and Molstad Eiendom as companies. Molstad is also active as chairman of the board. “We are an excellent company with reliable and capable owners who have given us the opportunity to develop and build our capabilities. In addition, we have gained great trust as we receive inquiries and assignments because they have a lot to do with us. Confidence,” commented Tor Henning Molstad. “NAM is located in the middle of the Raufoss Industrial Park, which means that most of the production companies are on our client list. Now is the time to be found in the rest of the country. There is a desire to grow to get a proper boost .”
Sorli added: “We want to be able to expand the company by bringing in bigger investments, it takes time to build competitiveness, we’ve got that, and now we’re starting to make money. Then, naturally, it’s going to increase capacity, go further with new technology and more people. Building companies. We invite all interested companies to challenge us so we can show what we can produce, and we are also open to dialogue with interested partners.”
NAM is currently participating in several research projects in the EU, with partners including Fraunhofer, Kongsberg Maritime and other German and Italian entities. “With additive production, you can achieve a fast process from idea to final product, and we have designed a completely new printing strategy for our customers that enables them to significantly reduce their manufacturing time.”
(responsible editor: admin)
0 Comments for “Positive results for Nordic Additive Manufacturing using DED AM technology”