
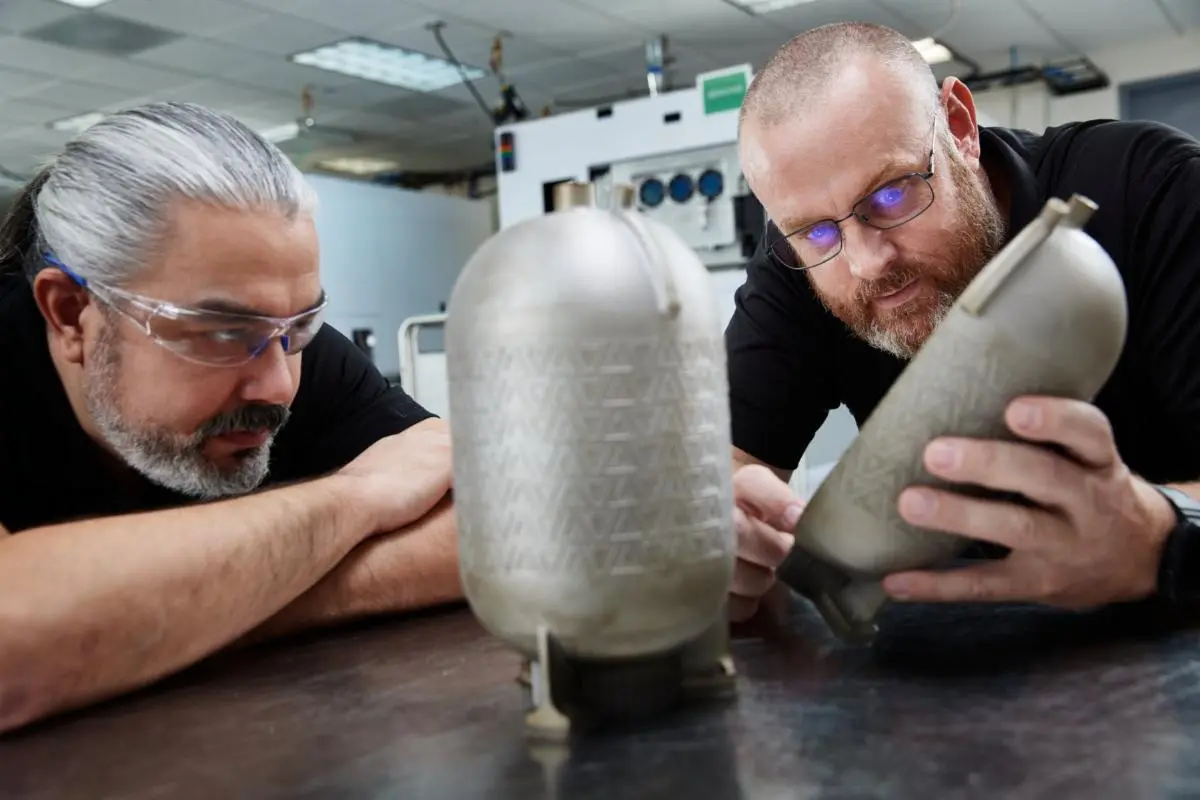
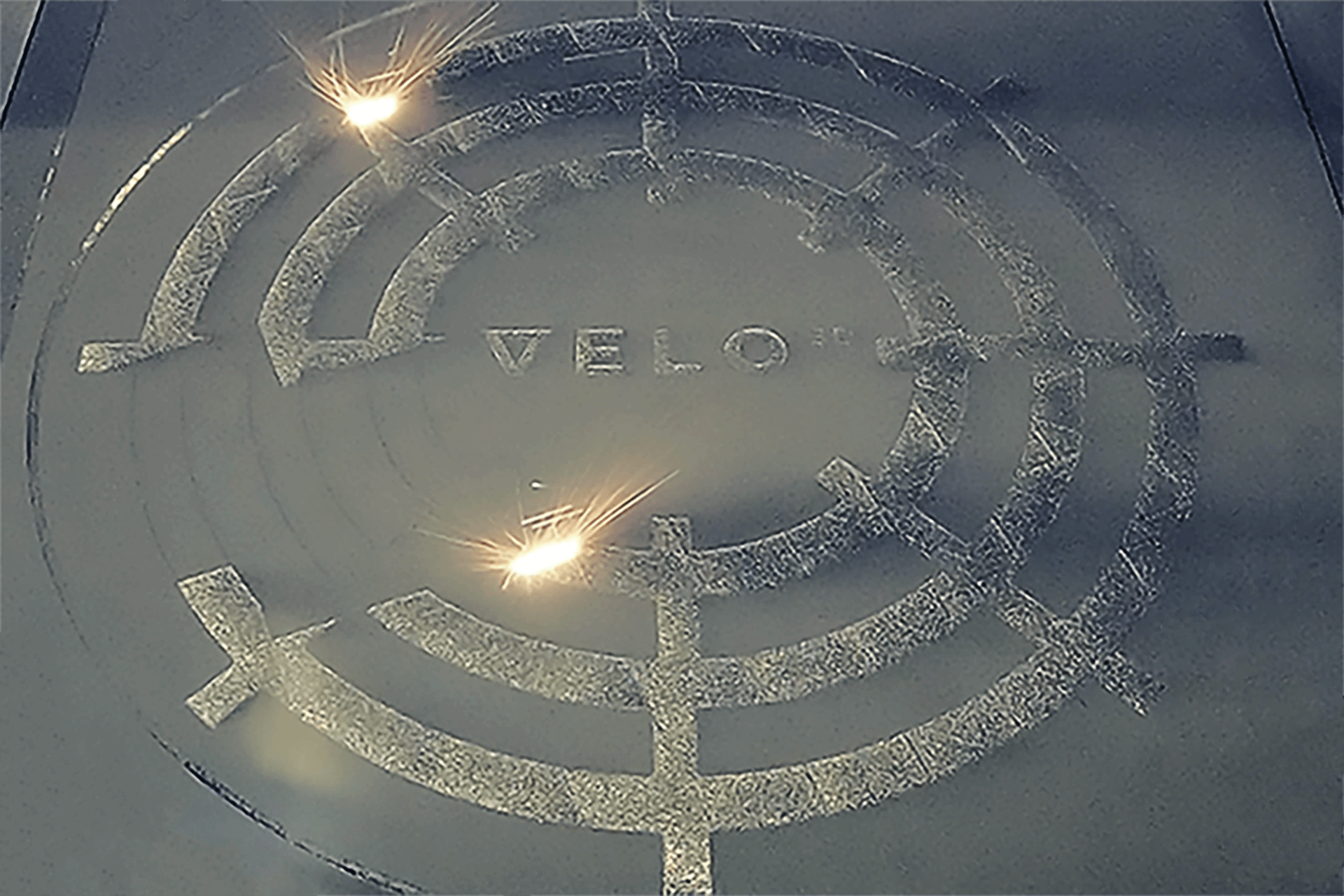
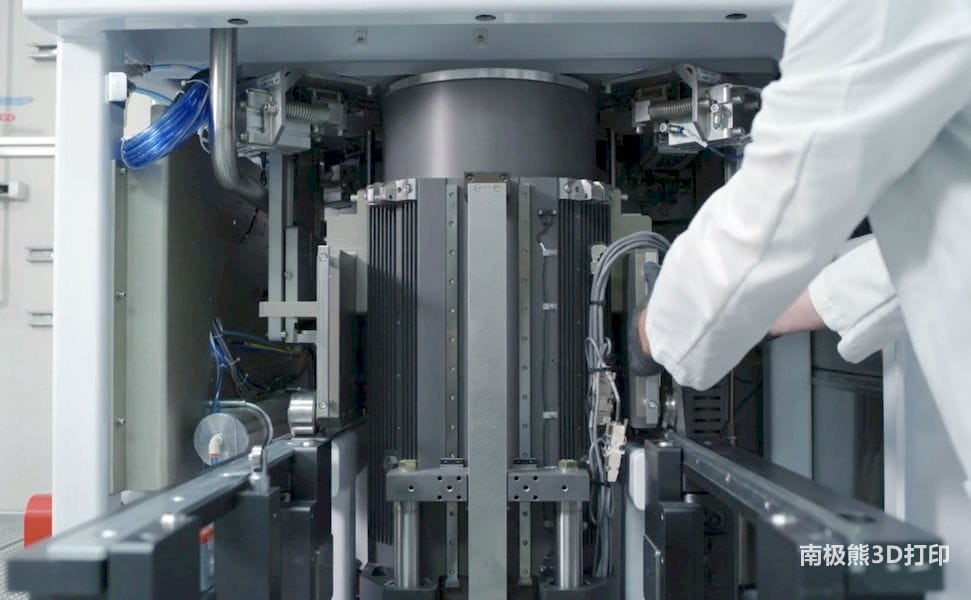
Sapphire uses metal laser powder bed fusion technology. While conventional systems typically need to support surfaces below 45 degrees, sapphire uniquely enables a design that overhangs down to zero degrees. Sapphire was designed from the ground up with an eye toward production. The 315mm diameter cylindrical cavity for sapphire is now available in 400mm and 1000mm configurations. The machine is able to provide the same SupportFree functionality and quality control in two different moulding cavities. Sapphire supports a comprehensive list of applications, and Sapphire integrates with VELO3D Flow™ pre-print software and Assure™ quality assurance and control systems. A dual kW laser is also employed to speed up printing, as well as a proprietary non-contact recoater to reduce the risk of parts crashing.
(responsible editor: admin)
0 Comments for “Primus Aerospace uses VELO3D unsupported metal 3D printer to produce titanium aerospace and defense components”