Cost and efficiency have always been
aerospace
Pain points of industry development. The significance of commercial spaceflight is to quickly provide safe, extremely low-cost rockets to the market, making space transportation services affordable to a large number of organizations and individuals.A key technology to reduce aerospace manufacturing costs is3D printing.pass through3D printing, the pace of rocket research and development will be greatly accelerated. And the ability to supply parts in batches, it is also necessary to create a vertical production model and effectively control costs, in order to rapidly improve the efficiency of parts supply in batches.
Established in March 2021, “Taihan Aerospace” is committed to developing a series of liquid propellant launch vehicles and providing cost-effective rocket launch and transportation services.around3D printing technology, Taihan Aerospace has established a production line for the entire industry chain of rocket parts and realized a rapid iterative R&D model. The goal is to achieve rapid and safe entry into orbit under the premise of strict cost control.
3D printed engine
The Taihan team has backgrounds in rocket manufacturing, 3D printing, material science, and IT. In order to compress the cost to the extreme, Taihan plans to 3D print more than 90% of the rocket’s components in the Taihan factory directly from raw materials into finished products. Through new technologies and a vertically integrated business model, Taihan aims to keep rocket procurement costs within one-fifth of the industry average.
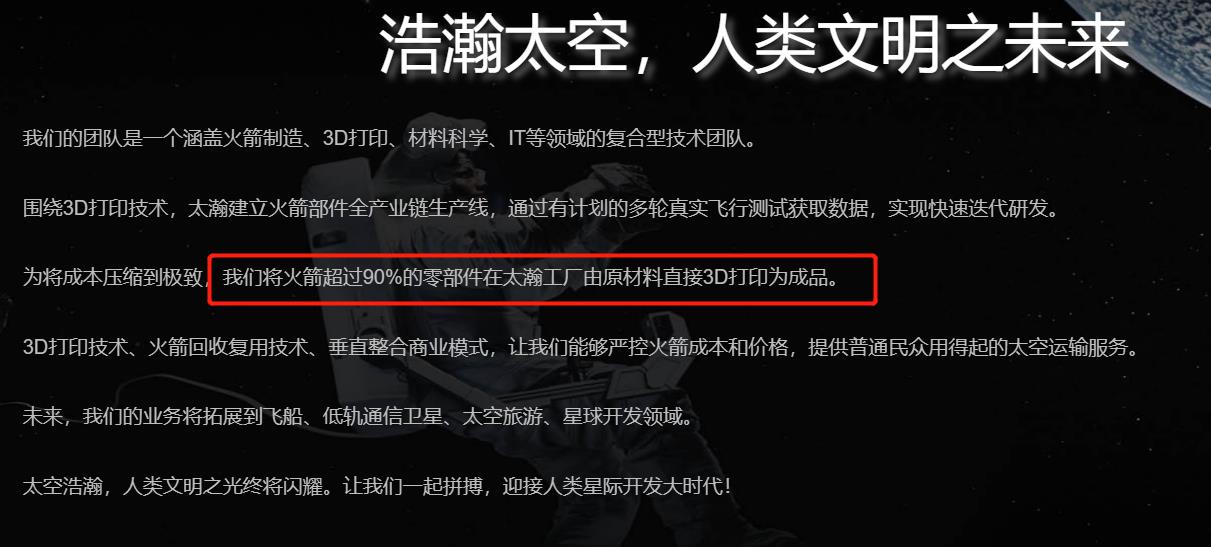
Vehicle development, power first, rocket engine technology is the core technology of the rocket company.
Taihan is developing the Xiaoyi liquid rocket engine, which uses liquid oxygen and kerosene as propellants. The high-pressure supplementary combustion cycle technology is used to improve the engine performance, with an advanced architecture and performance indicators higher than the gas generator cycle technology commonly used in commercial aerospace, and the performance of the national team’s main rocket engine is comparable. The engine V1 currently has a thrust of 20 tons at sea level, and the V2 version is optimized to 30 tons when it is officially put into use.
All parts of the Xiaoyi engine are 3D printed, and the manufacture of one engine can be completed within 30 days, which greatly speeds up the development and testing cycle.pass through3D printing technology, The components of the Xiaoyi engine are much less than those of the traditional technology, and it is simple and easy to install and easy to optimize the structure.
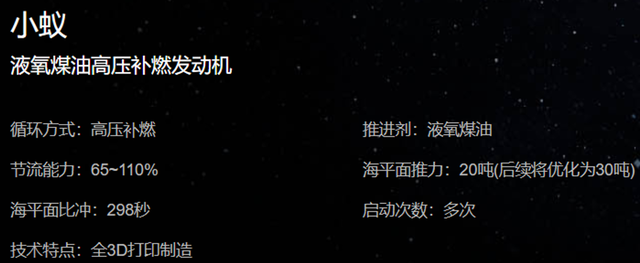
According to the special requirements of rocket engines for 3D printing, Taihan 3D printing team designed and manufactured exclusiveMetal 3D Printingmachine S480, and developed a supporting 3D printing
software
and 3D printing process.Currently established in Xi’an3D printerThe production line is in the process of debugging the 3D printer. In addition to the S480, Taihan is also developing the W450 rocket 3D printer for printing rocket bodies. The printer uses self-developed software, technology and special alloys, and the printed arrow body can meet the requirements of rocket launch. Taihan Shanghai factory is building a rocket manufacturing production line. Using this 3D printer, a complete rocket body will be manufactured within 3 months.
Taihan plans to complete the first launch test within two years of the company’s establishment, and then achieve rapid entry into orbit through rapid iteration. Reduce the time rockets are tested in the laboratory, obtain data and improve optimization through real flight tests. Taihan plans to verify the 3D printed rocket engine, 3D printed rocket body structure, servo mechanism, inertial group, recyclable control system and other products in suborbital. According to the plan, the first 3D-printed engine part is the pre-combustion chamber, and the first 3D-printed rocket body structure is the second-stage box section of the rocket. In addition to the rocket body and rocket engine, the main components of the rocket, including inertial navigation components, servo mechanisms, sensors, and industrialized flight control systems, are also being developed in an orderly manner.
Meanwhile, Taihan is building onlineMetal 3D Printingmall, will
Metal3D printing service
The price is transparent and people-friendly, helping the application of 3D printing technology in various industries. 3D printing technology is likely to be a useful construction tool when humans build bases on the moon and Mars in the future.
Using 3D printing technology and a vertical business model can greatly reduce the cost of rocket manufacturing. For the R&D and factory investment of the rocket and 3D printing business, Taihan estimates that the rocket will successfully enter orbit in 2024 after a total investment of about 600 million yuan in the early stage. 2023 to rely on3D printing serviceEarly access available
income
.
The first rocket and future plans
Feitian is Taihan’s first rocket model. The first stage integrates 9 Xiaoyi engines, and the second stage uses a Xiaoyi vacuum version. The rocket has a take-off thrust of 270 tons and can provide 4 tons of LEO payload capacity. Based on 3D printing technology and vertical business model, the procurement cost of a new Feitian rocket is expected to be controlled to the level of 10 million yuan. Combined with recyclable technology, the cost of purchasing part of each rocket will be lower.
Having the ability to enter orbit is the first step for Taihan to successfully implement the follow-up plan. Taihan develops key equipment through technological innovation, and builds its own industrial automation production line for the entire rocket industry chain (design, manufacturing, testing, launch), which greatly reduces costs and shortens cycle. Taihan advocates rapid iterative research and development, and through planned multiple rounds of testing and trial and error, the research and development cycle, performance, and security are brought closer to the extreme. Through the liquid propellant carrier rocket, the cost-effective small-scale special arrow carrier service and the large-scale arrow carrier service will be improved.
In the future, Taihan will build engines with larger thrust and rockets that carry larger loads, and build cargo and manned spaceships to provide the construction of space station cargo, space tourism, space hotels, space gas stations, moon bases and Mars bases. Transportation services, providing stable, safe and affordable space transportation services. Taihan plans to build a rocket and engine capable of suborbital verification in 2023.
Industry Status
In the global commercial aerospace industry, almost all startups are thinking or exploring 3D metal printing technology. 3D printing helps reduce rocket weight because fewer nuts, bolts and welds are needed to produce complex structures. And when the engine fails RUD (rapid unplanned disintegration), it only takes a few days for the engineers to re-build the model and test it again.
Take SpaceX, the leader in commercial spaceflight, for example. SpaceX first used 3D printed parts on the Dragon 3 aircraft as early as 2014. Their first 3D printed part was the main oxidizer valve of a rocket engine. If the valve is manually manufactured and installed, it will take more than 2 weeks. Using 3D printing technology, SpaceX produced the valve in just 2 days. SpaceX Genius 3D is now also a core tool for SpaceX’s rapid manufacturing.for SpaceXMetal 3D Printermanufacturer of
VELO3D
, which will be listed on the New York Stock Exchange in March 2021.
In addition to SpaceX, Rocket Lab in New Zealand, Relativity Space and Launcher in the United States, and Skyrora and Orbex in the United Kingdom have also received extensive attention in the industry in terms of 3D printing. In 2017, Rocket Lab successfully launched a rocket with a 3D printed engine, and reached the milestone of manufacturing 100 3D printed engines in July 2019. The idea of relativistic space is more avant-garde. The company hopes to directly 3D print a complete rocket without any artificial assembly. Orbex aims to launch a rocket with a 3D-printed engine as early as 2022.
In addition to players in commercial aerospace, many state-owned aerospace departments and units are also actively developing 3D printing technology. The main reason is that large-scale rockets have many manufacturing parts. If the process can be reduced by 3D printing, the manufacturing efficiency of rockets will be greatly improved. In 1969, the Saturn V F-1 engine used in the US moon landing had 5,600 manufactured parts, while the Apollo F-1 engine redesigned using 3D printing technology has been reduced to 40 manufacturing parts.
In China, around 2000, the 7103 Factory of the Sixth Institute of Aerospace Science and Technology Group has begun to deploy 3D printing technology, and introduced selective laser sintering (SLS) equipment and technology for the rapid development of my country’s new generation of liquid oxygen and kerosene rocket engines. In 2016, the first flight of the Long March 5 was successful, and the 3D printing products of the 7103 factory appeared in space with the Chang 5. Up to now, 3D printing technology has been used in more than 240 typical products of more than 40 models in the 7103 factory, and the products have successfully participated in more than 50 launches and flight tests.
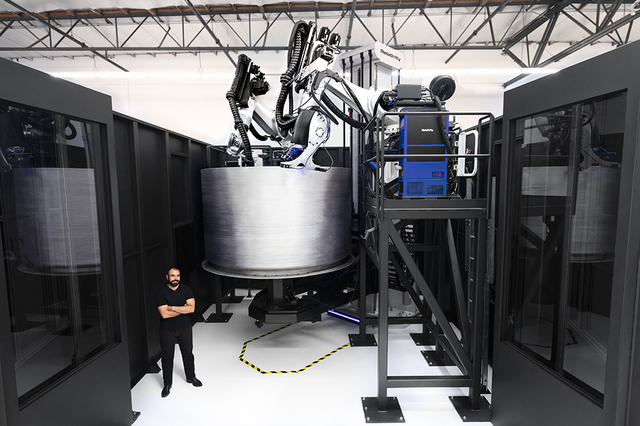
(responsible editor: admin)
0 Comments for “Provide cost-effective rocket launch and transportation services, “Taihan Aerospace” aims at full 3D printing rocket manufacturing”