Guide: Mankind’s exploration of the sea of stars has never stopped, since the US space company RelativitySpace in JuneManufacture reusable rockets and expand financingLater, this company completed the3D printingRocket Terran 1 first stage complete test.

△Terran 1 first stage test preparation
The Antarctic Bear learned that Relativity Space has completed the alignment3D printingThe first stage of the Terran 1 rocket has been fully tested and will be3D printingaviationaerospaceThe application has been pushed to an important point. At the company’s Long Beach, California plant, the first phase of the rocket successfully passed waterproof, cryogenic and flight pressure tests. Once launched, this two-stage small lift launch vehicle will be equipped with a three-meter fairing, capable of launching a payload of up to 1250 kg into Low Earth Orbit (LEO). It is reported that Relativity is preparing for a demonstration launch in early 2022.
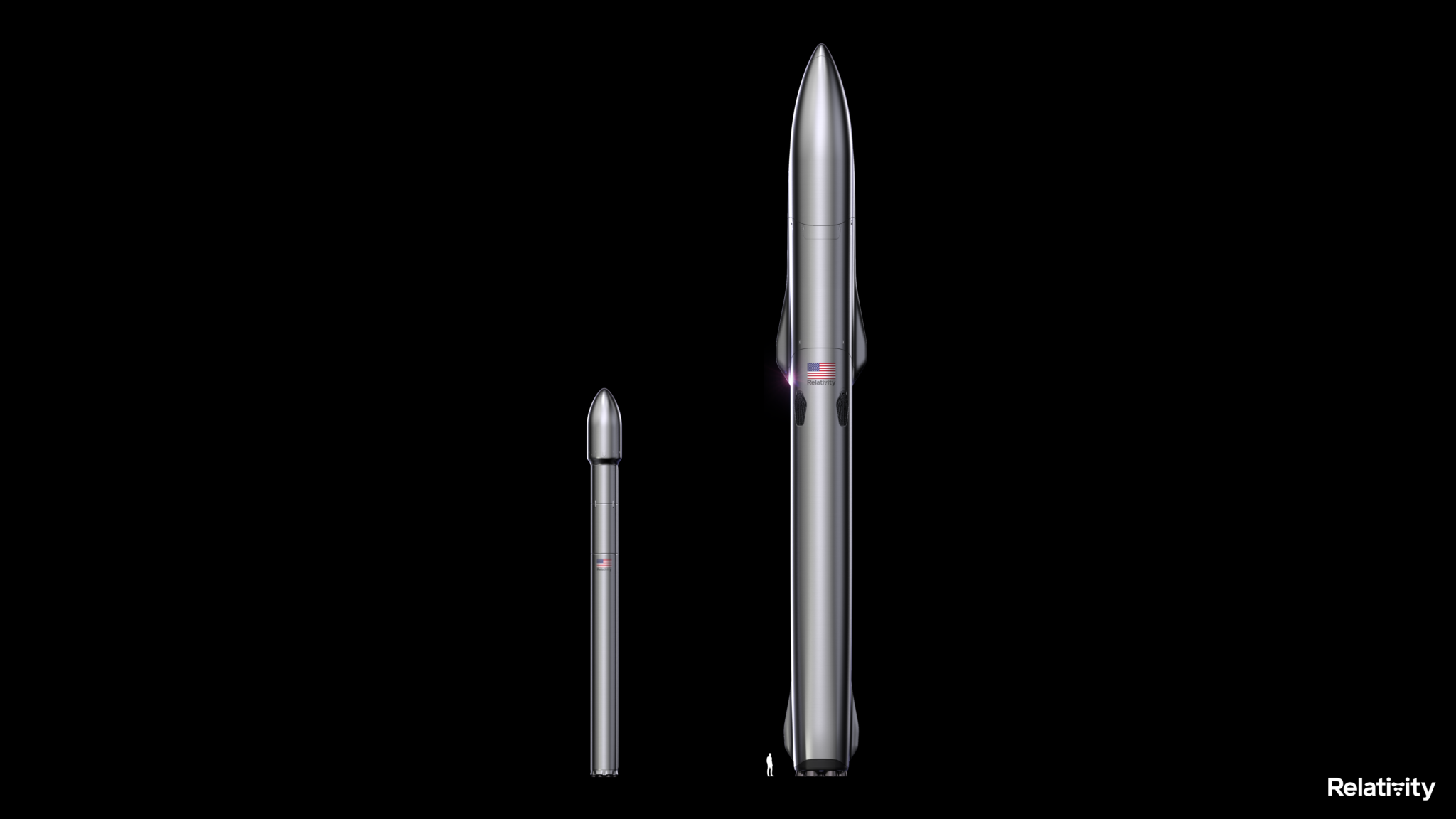
△ Relativity Space’s full3D printingRockets, Terran 1 and larger and reusable Terran R. Image courtesy of Relativity Space.
Terran 1 and Stargate printers
Since its development in 2017, Terran1 as Relativity’s first completely3D printingRockets may be one of the most innovative products that have appeared in the aerospace manufacturing industry in the past decade.This is mainly because Relativity uses two types of3D printingTechnology has produced a structure that accounts for more than 90% of the rocket’s mass, and its large format3D printingStargate can use aluminum alloy to manufacture primary and secondary structures, and can also perform inspection and small quantities in a printing unit.Post-processing.
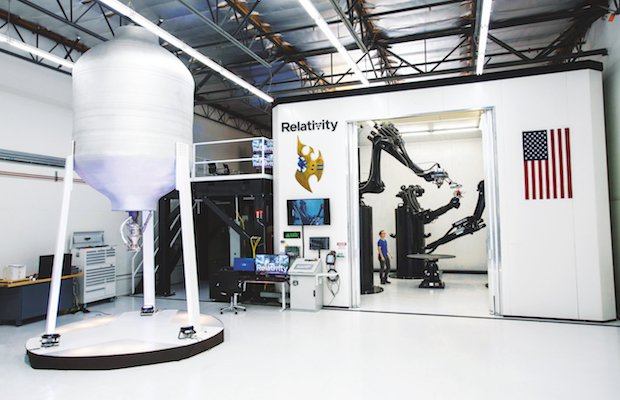
△ Relativity’s Stargate 3D printingEngine and a fuel tank that was additively manufactured in three days.
Stargate can currently print structures up to 3.4 meters in diameter and 7.6 meters in height, perhaps the largest metal part that can be printed at present. Relativity3D printingThe platform can vertically integrate artificial intelligence, robotics, and autonomous manufacturing technology, and Terran 1 can be manufactured in less than 60 days, which makes this manufacturing technology very attractive to customers. Relativity also used direct metal laser sintering (DMLS) to produce small, high-fidelity components for Terran 1. The company also recently released a uniquely shaped nose cone created for Terran 1, which does not use fixed tools in the manufacturing process.
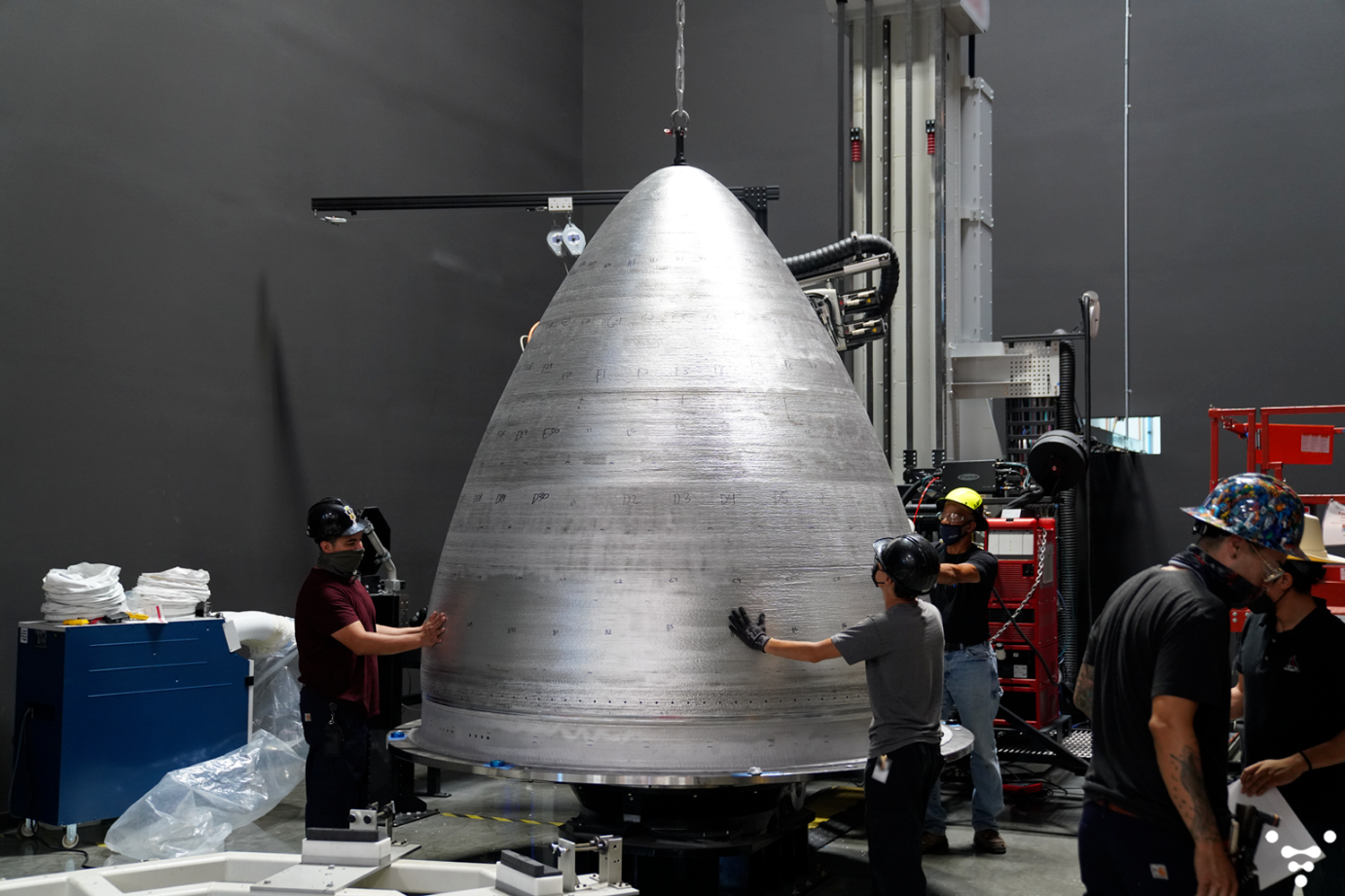
△Terran1 full3D printingNose cone
Terran 1 first-level components consist of three main components: thrust structure, first-level fuel tank and inter-stage.The fuel tank is placed in the whole3D printingOn the dome and fuselage, the first stage parts are integrated together through a horizontal welding process, and the liquid oxygen (LOX) is transported to the engine through the liquefied natural gas (LNG) tank through the delivery pipe. The rocket is equipped with nine Aeon-1 engines to power the first stage, and the total thrust is expected to be as high as 207,000 pounds during lift-off.
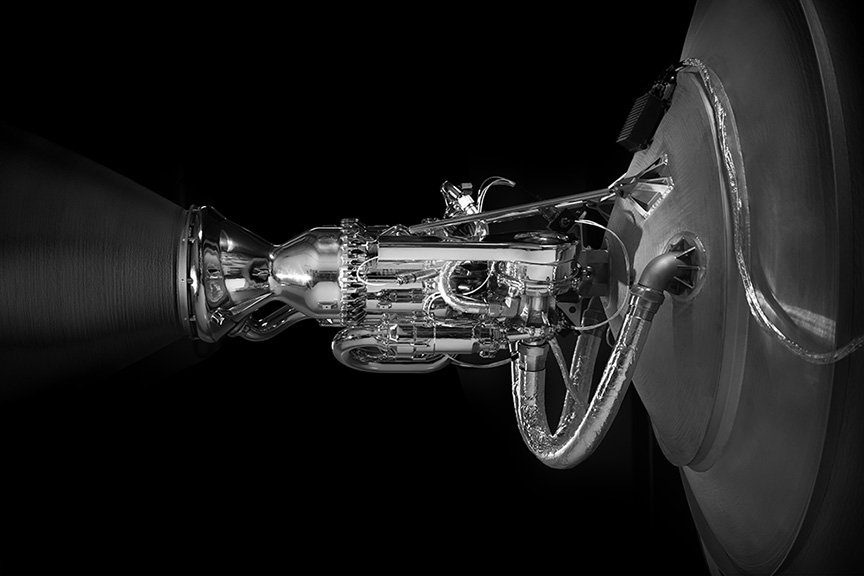
△Aeon engine
The test is complete and ready to launch
With the completion of Stage 1 testing, Terran 1 has entered a critical pre-launch stage. In addition, Stage2 of Terran 1 has also passed low-temperature pressure resistance and hydro-mechanical buckling tests on the structural test bench. Relativity also revealed that they completed the Terran 1 architecture in just 12 months, developed new engines, upgraded materials, and increased the size of the company from 150 employees to more than 500.
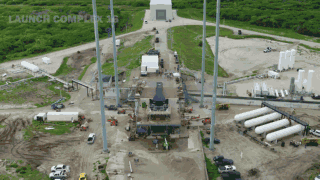
△ launch preparation
It is reported that the demonstration launch of Terran 1 is scheduled for early 2022 at Launch Site 16 (LC-16) at the Cape Canaveral Space Force Station in Florida. The launch site will support Terran 1’s initial test flight and follow-up missions, and support low- and medium-inclination orbits. As part of major launch preparations, Relativity engineers recently completed the first test launch of the LC-16 strong back structure, which will provide support for the launch vehicle. In addition, the preparation process also includes bringing electrical facilities to the launch site and commissioning, starting the hydraulic lifting system, and manufacturing and installing the launch pad.
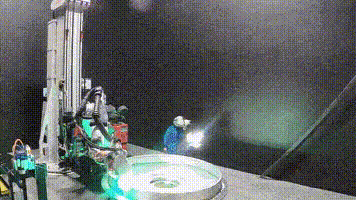
△3D printingTerran 1 Level 2 Flying Tank Manufacturing Process
Just two days before announcing the first phase of the complete test, Reuters reported that the Federal Aviation Administration (FAA) proposed to issue an operator license to this venture-backed startup after completing an environmental review. According to the news agency, the U.S. Air Force and the Federal Aviation Administration, a partner agency, prepared an assessment and stated that Relativity must also meet agency safety, risk, and financial responsibility requirements before it can issue a license.
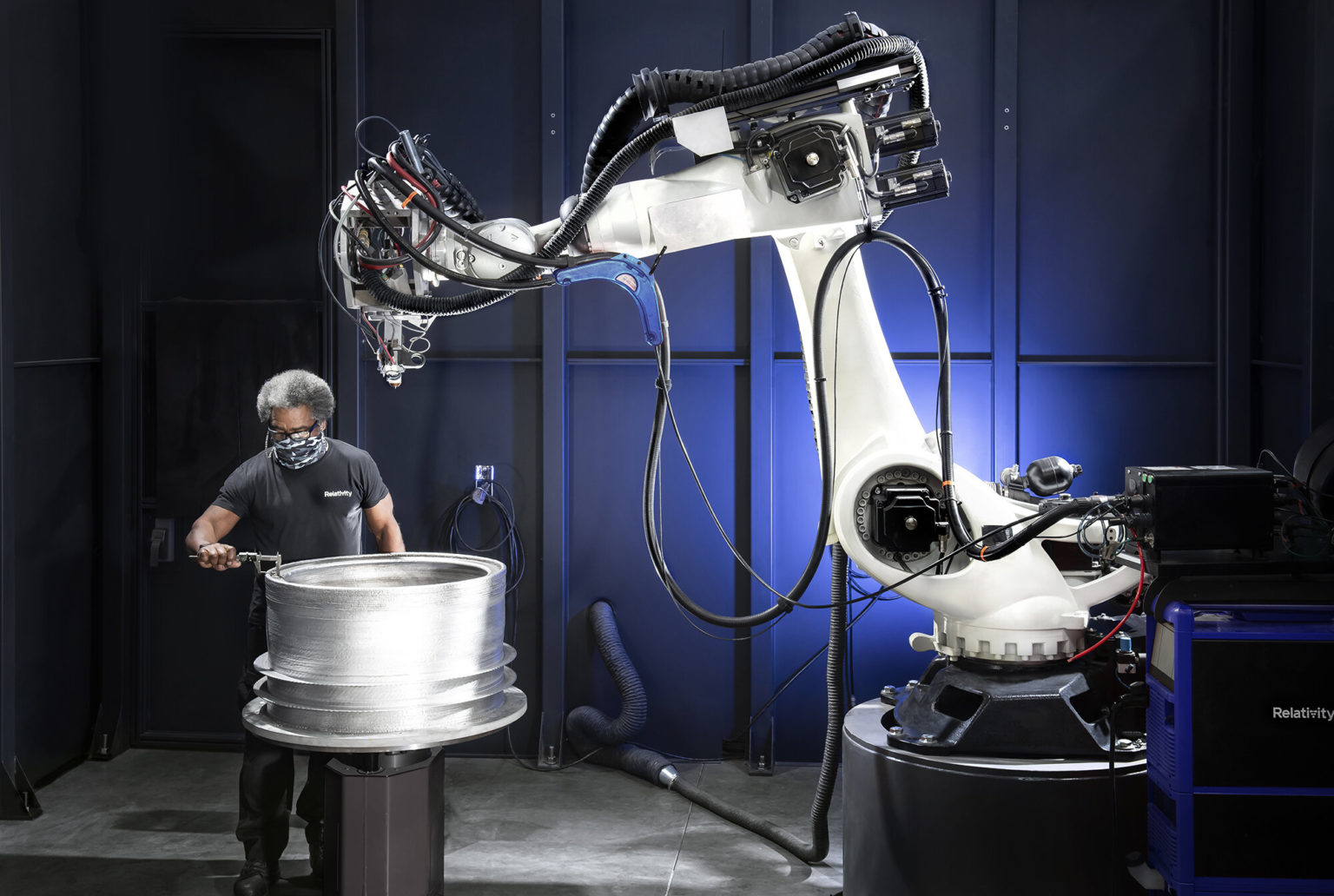
△The interior of Relativity Space3D printingtechnology
Antarctic Bear learned that Relativity is currently valued at US$4.2 billion and is the second most valuable private aerospace company after Elon Musk’s SpaceX.The achievement of this valuation is consistent with the recent E roundFinancingThe US$650 million raised in China has a lot to do with it.investThe total funding has also increased to 1.3 billion US dollars.At this rate, this private company has enough strength to use indoor3D printingTechnology to manufacture the entire rocket, and continue to develop the “factory of the future” plan by simplifying the supply chain. At present, the company has achieved a 100-fold reduction in the number of parts of the launch vehicle.Let us look forward to the first in the world3D printingLet’s take off the Terran 1 rocket!
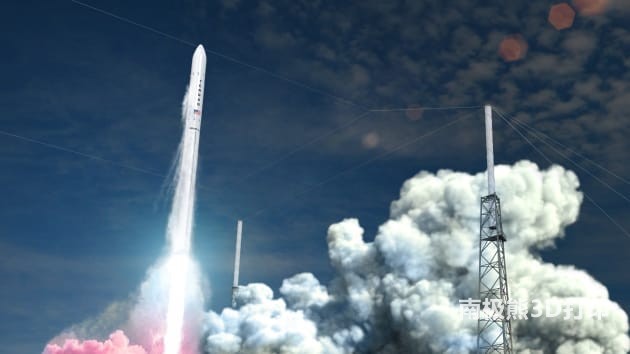
△Computer rendering: Relativity’s rocket Terran launched from the LC-16 launch pad at Cape Canaveral
(Editor in charge: admin)
0 Comments for “Relativity Space’s fully 3D printed rocket Terran 1 completes the first phase of testing”