Additive manufacturing is a revolutionary technology that provides different ways for material processing and design. However, if there is no synergistic combination, innovations in new materials or new processing technologies rarely succeed. This study demonstrates an in-situ design method to prepare spatially modulated concentration alloys through laser powder bed fusion.
The researchers found that the partial homogenization of two different alloy melts-Ti-6Al-4V and a small amount of 316L stainless steel can adjust the micron-level concentration of the elements contained in 316L in the Ti-6Al-4V matrix. The corresponding phase stability modulation produces a fine-scale modulated b+a′ biphasic microstructure, showing the plastic effect induced by gradual phase change, resulting in a high tensile strength of about 1.3 gigapascals and a uniform elongation of about 9%. Length rate and excellent work hardening ability of >300 MPa. This method opens up a way for the design of concentration-modulated heterogeneous alloys for structural and functional applications.
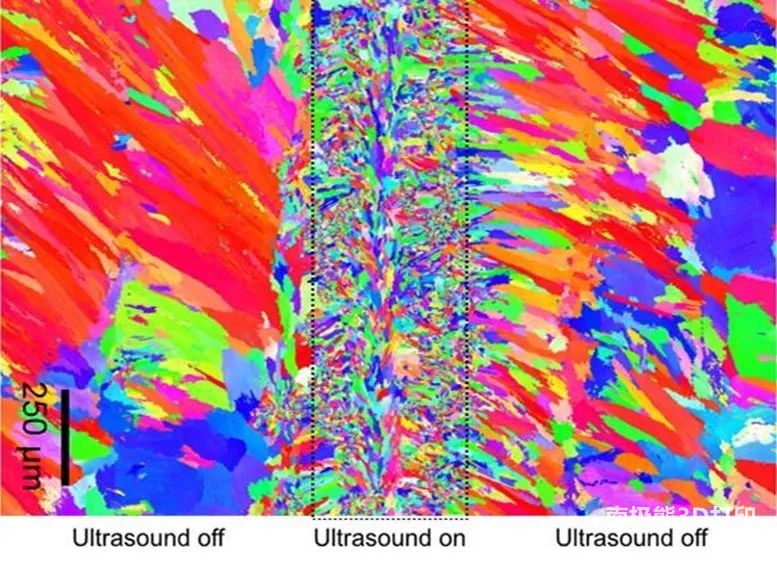
3D printingThe Inconel 625 grain structure visualization is realized by turning on and off the ultrasound during the printing process.Source: RMIT University
Additive manufacturing (AM), also known as three-dimensional (3D) printing, integrates multiple metallurgical processes into one process, in which alloy manufacturing, forming, and processing are performed simultaneously in one process. However, AM is largely regarded as a forming technology that can produce material compositions close to the net shape, and does not make full use of the ability to simultaneously and synergistically advance alloys and processes provided by AM. By flexibly constructing components point by layer, AM provides the opportunity to create a heterogeneous alloy with a specific location composition and microstructure.
In the laser powder bed fusion (L-PBF) process, due to the short life of the molten pool and the fast cooling rate, by using a pre-mixed mixture of different alloys or elemental powders to partially homogenize in each molten pool, a finer size can be achieved. Scale (such as micrometer scale) concentration modulation (hereinafter referred to as micrometer scale). This microstructure has been shown to have the potential to provide unique advantages of various alloys, such as the graded preferrite microstructure in b-Ti; the martensite-austenite heterostructure in steel; and the ferroelastic material Controlled strain release, linear superelasticity and ultra-low modulus of elasticity.
The researchers demonstrated how to use a mixture of two commercial alloy powders: Ti-6al-4v (Ti64) and 316L (67.5Fe-18Cr-12Ni-2.5Mo, wt %), and design such a microCM titanium alloy through L-PBF. The choice of these two alloys is based on the following considerations. Ti64 prepared by the AM method has for a long time the problems of large harmful columnar grains and poor work hardening ability. The elements in 316L (Fe, Cr, Ni and Mo; we call them 316L elements) are effective grain refiners in titanium alloys, and also effective stabilizers in titanium alloys.
In addition, there are also high-quality powders of two alloys in L-PBF. By appropriately selecting the addition amount of 316L and the L-PBF process parameters, these elements form microCMs in the Ti64 matrix, and the phase stability modulation corresponding to the concentration modulation forms a fine-scale modulation b+ a’double in the printed alloy Phase organization. This type of microCM titanium alloy exhibits a high yield strength and a progressive deformation induced plasticity (TRIP) effect during deformation, which leads to an extended uniform extension and an enhanced work hardening effect.
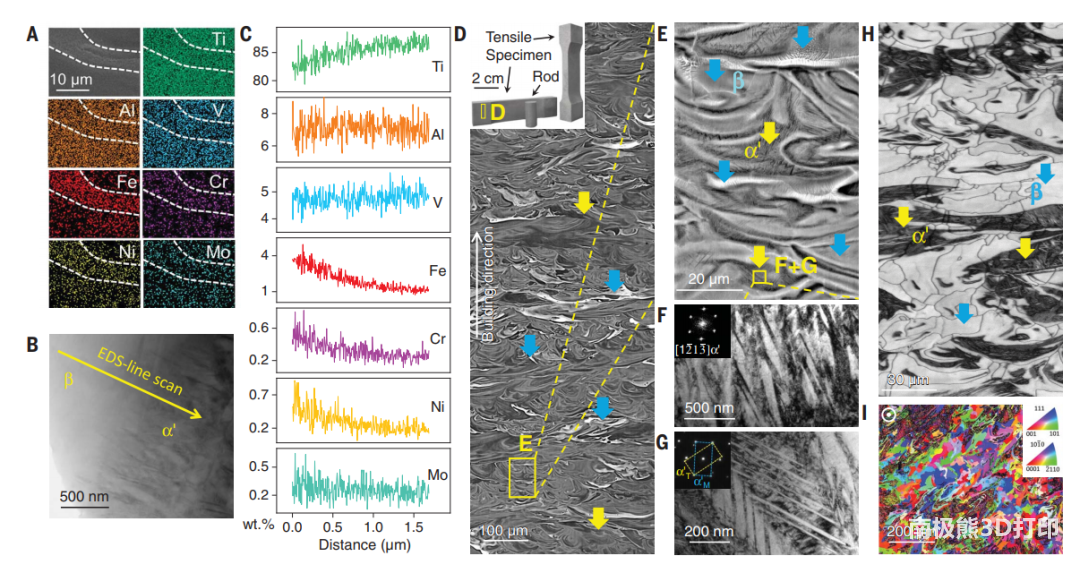
The typical microCM structure of Ti64-(4.5%)316L(wt%) alloy is shown in Figure 1 (A to C). For example, our scanning electron microscope-energy dispersive spectroscopy (SEM-EDS) image (Figure 1A) shows that Ti, Al, and V (Ti64 elements) are obviously depleted, and Fe, Cr, and Ni (316L elements) are enriched in the molten pool. In a whirlpool. The high-power transmission electron microscope-EDS (TEM-EDS) line scan results (Figure 1, B and C) show a clearer intra-particle concentration gradient along the a’-B interface area. Compared with the b-phase zone, the 316L element (b stabilizer) content in the a’martensite phase zone is much lower. In the center of an a′ and a b phase region, the precise composition we measured with 3D atom probe tomography (3D-APT) are Ti-6.0Al-4.1V-0.9Fe-0.3Cr-0.1Ni-0.01 respectively Mo and Ti-5.8Al-3.9V-6.4Fe-1.7Cr-1.6Ni-0.3Mo[也可简化为Ti64-(1.3%)316L和Ti64-(9%)316L]. Therefore, the microCM alloy has a specific position in the entire structure.
During L-PBF, the microCM is generated by the partial homogenization of the two alloy melt vortices in the melt pool, where the two alloy melts in the melt pool are physically mixed by fluid flow with Marangoni motion , Chemical mixing through atomic diffusion.
Although physical mixing tends to homogenize the melt on the scale of the melt pool (generating a vortex of two alloy melts), complete homogenization (for example, the complete decomposition of 316L element into Ti64) requires adjacent enrichment in the melt pool. 316L element and Ti64 element-rich vortex are fully chemically mixed and fully merged with each other. Due to the small molten pool size and the rapid solidification associated with L-PBF (31, 32), it remains partially homogeneous after solidification. The range of 316L concentration measured by APT, TEM-EDS and SEM-EDS in microCMTi64-(4.5%) 316L alloy is ~1.3 to ~9.9wt% (Dc) ≈ 8.6% (weight percentage).
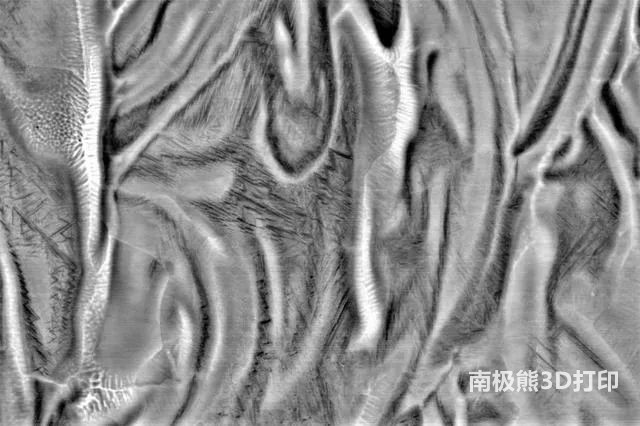
This concentration unevenness has been reported and is considered to be an adverse reaction of AM. However, researchers have actively used this feature of L-PBF to realize microstructures in titanium alloys, thereby forming a modulated dual-phase (a′+metastable b) microstructure with excellent mechanical properties.
The microCM has a direct effect on the phase stability and microstructure modulation of the printed alloy. From the side view cross section of the printed Ti64-(4.5%) 316L, through backscattered electron (BSE) imaging, we observed a lava-like microstructure, showing a clear vortex pattern of fluid flow in the molten pool (Figure 1, D and E). In each individual molten pool area, in the dark (316L element-lean) and bright (316L element-rich) vortices, we found two very different microstructure characteristics. The dark vortex is composed of fine needle-like a’martensite (yellow arrow), the typical lath thickness is about 100 nm, and there are some ultra-fine twin structures inside (the twin spacing is about 20 nm) (Figure 1, F and G) ).
However, the bright vortex consists of a single phase b with a cellular microstructure in the center (blue arrow). We used electron backscatter diffraction (EBSD) results (Figure 1, H and I) to confirm the highly non-uniform and finely modulated b+a’ microstructure. Unlike the traditional large columnar grains along the build direction, ultrafine grains are observed in AM Ti64 (35-37). In addition, the printed alloy has a high density (>99.9%) (Figure S1).
Figure 2 The microstructure and mechanical properties of the printed microCM Ti64-x316L alloy. (A) Engineering stress-strain curves of printed Ti64-(6.0%)316L, Ti64-(4.5%)316L and Ti64-(2.0%)316L alloys. UTS is marked by a large open symbol in the curve. (B) Compared with Ti64 alloys produced by different AM methods and traditional technologies, the engineering tensile strength and uniform elongation of the printed Ti64-x316L alloy (22,38
0 Comments for ““Science”: On-site design of advanced titanium alloys using additive manufacturing concentration modulation”