In recent years, three-dimensional (3D) printing technology has developed rapidly.Looking ahead, it is expected that the3D printingtechnology to create soft, compliant surfaces on the skin and even inside the body
biology
medicine
Devices and sensors to advance personalized patient health monitoring, wound treatment, and improved organ function. For example, spatiotemporal monitoring of lung deformation in vivo can be used to provide valuable information for respiratory mechanics studies, chronic lung disease diagnosis, and lung cancer treatment.On living organs, the ability to directly print compatible biomedical devices could benefit patient monitoring and wound treatment, which require3D printingMachines adapt (and dynamically) to various deformations of biological surfaces.
Researchers at the University of Minnesota have developed an in-situ 3D printing system that can be used to monitor the movement and deformation of the surface of a target organ to adjust tool paths in real time. By using this printing system, hydrogel-based sensors can be successfully printed on pig lungs (in vivo) under dynamic respiration. The sensor conforms to the tissue surface and provides continuous spatial mapping of dynamic deformation via electrical impedance tomography (EIT).This adaptive 3D printing method could enhance robotic assistance with additive manufacturing capabilities
medical
, thereby enabling autonomous and direct printing of wearable electronics and biomaterials inside and outside the human body. The related research work was published in Science Advances (IF=13.116) with the title of “3D printed deformable sensors”.
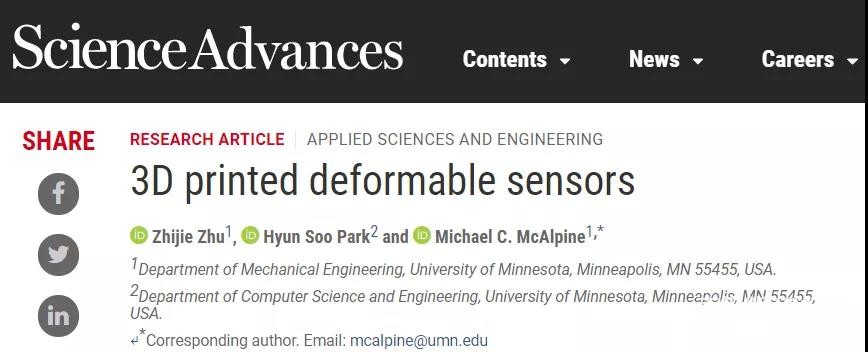
In previous work, the researchers demonstrated real-time tracking of rigid body motion on a target surface, including a total of 6 degrees of freedom (DoF) for translation and rotation. This closed-loop strategy enables direct printing on moving objects without surface deformation, such as the back of a human hand.
This paper presents a more advanced printing procedure: printable on dynamically deforming surfaces, by combining a visual sensing system with3D printerIntegrated, to track in real time with 3D geometry, fabrication of electrical impedance tomography (EIT) strain sensors on deformable lungs.
The authors go through a two-stage procedure: (1) first, a low-dimensional parametric model of the surface geometry is learned from an offline pre-scan dataset to reduce the computational complexity of the subsequent online process; (2) then, through a set of real-time measurements using a stereo camera Sparse fiducial markers estimate parameters in an offline learned model and recover conformal toolpath geometry online.
For offline learning, researchers employ structured light with submillimeter precision and resolution3D scanninginstrument.3D scanninginstrumentMultiple high-fidelity 3D scans of deformed lungs with fiducial markers were obtained (Fig. 1A). Based on 3D scans, the authors construct a point cloud training dataset with point-wise correspondences between data samples, and use machine learning algorithms to learn a linear shape-based model for surface deformation. For online tracking, the stereo camera system consists of a pair of synchronized machine vision cameras with high sampling rate (max 149 Hz) and adjustable focal length (~0.1 m) to track fiducial markers in 3D (Fig. 1B). The marker locations allow the learned deformation-based model to fully recover the shape deformation. This reconstruction was used as input to estimate in real time the conformal toolpath for adaptive printing on respiratory lungs (Fig. 1C). The printed EIT strain sensor conforms to the deformation of the lung and can provide in situ spatiotemporal mapping of lung deformation (Fig. 1D).

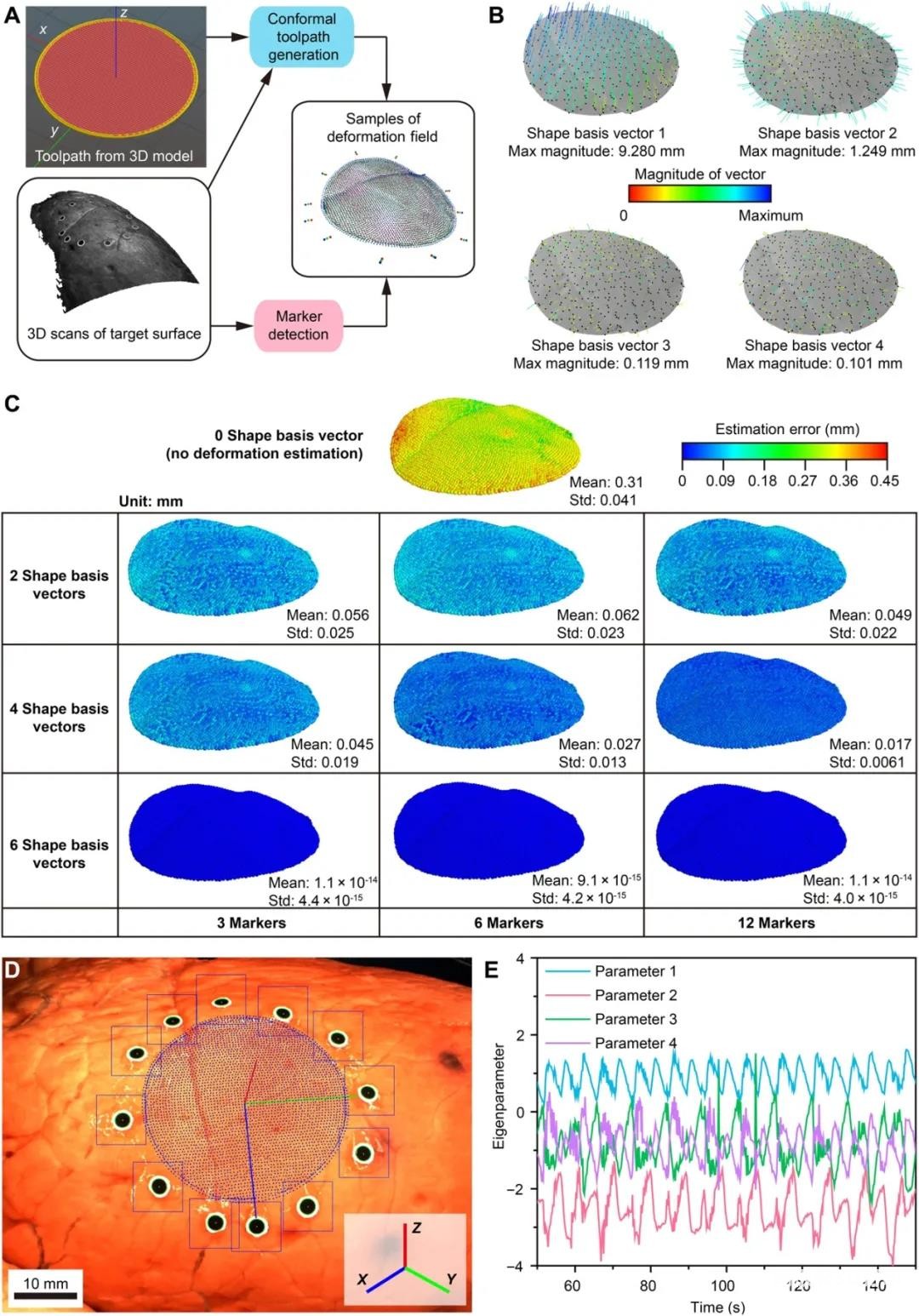
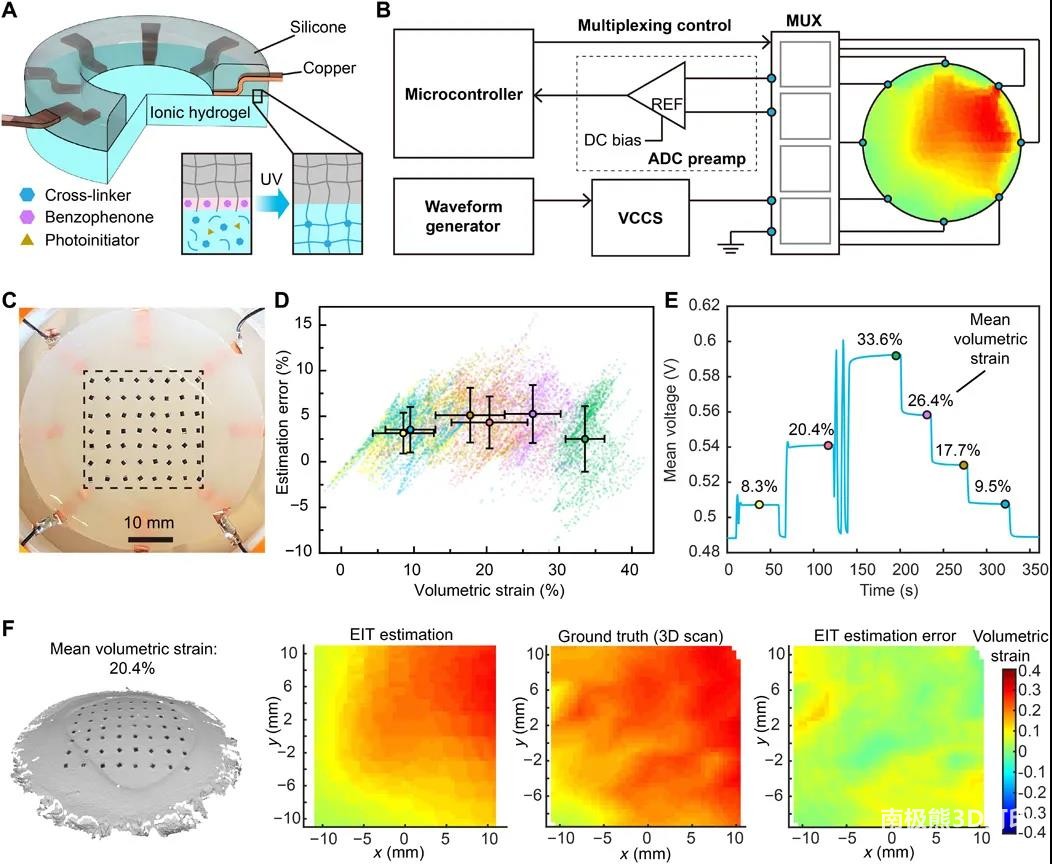
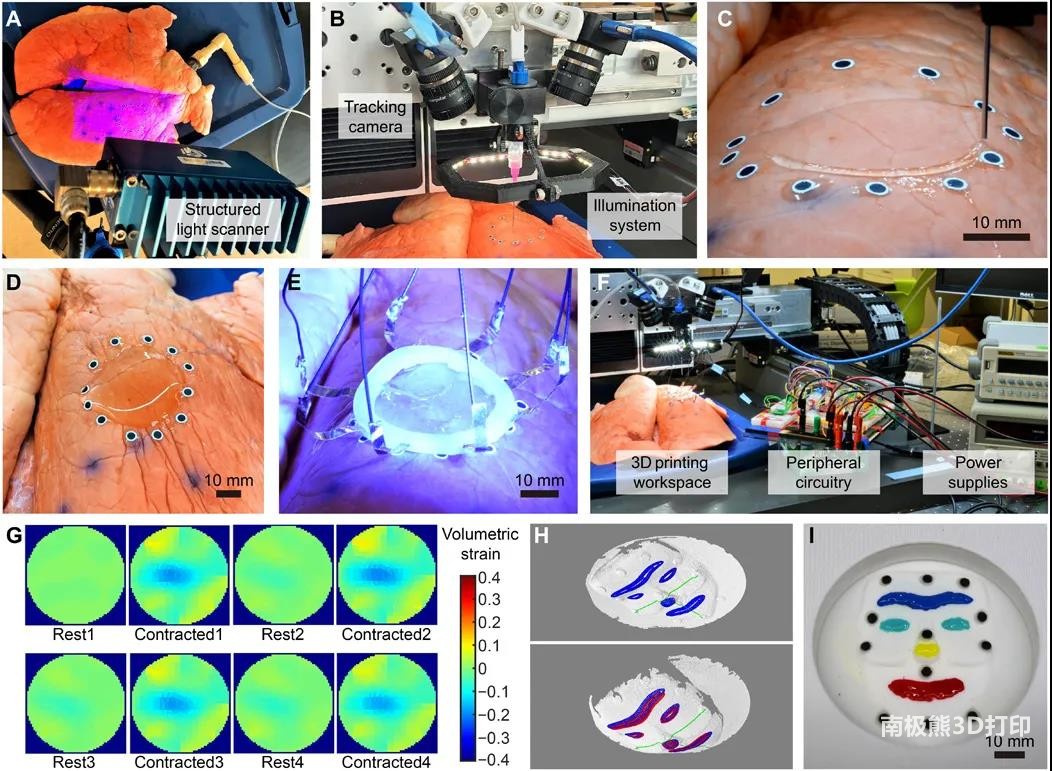
(responsible editor: admin)
0 Comments for “Science sub-journal: 3D printing flexible sensors directly on the surface of living organs”