Laser beam of metal3D printingAlthough the development is exciting, there are still many defects, and the mechanical performance is difficult to guarantee. LLNL researchers are exploring the use of Bessel beams for beam shaping to help3D printingOptimization, to ensure controllable quality and stable performance!
Although the laser3D printingTechnology has revolutionized the production of metal parts by greatly expanding design complexity, but it is undeniable that the laser beam traditionally used for metal printing is not perfect, which may lead to defects and poor mechanical properties. Researchers at Lawrence Livermore National Laboratory (LLNL) are exploring alternative shapes for Gaussian beams commonly used in high-power laser printing (such as powder bed laser melting LPBF) to solve this problem. Their latest research was published in “Science Advances”.
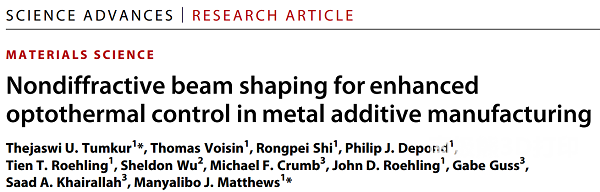
The researchers conducted experiments with the unique shape of the Bessel beam, which has special non-diffraction and self-healing properties. Research has found that the application of this beam reduces the possibility of the formation of pores and “keyholes”, and the application of Gaussian beams in LPBF causes the occurrence of the “keyhole” phenomenon.
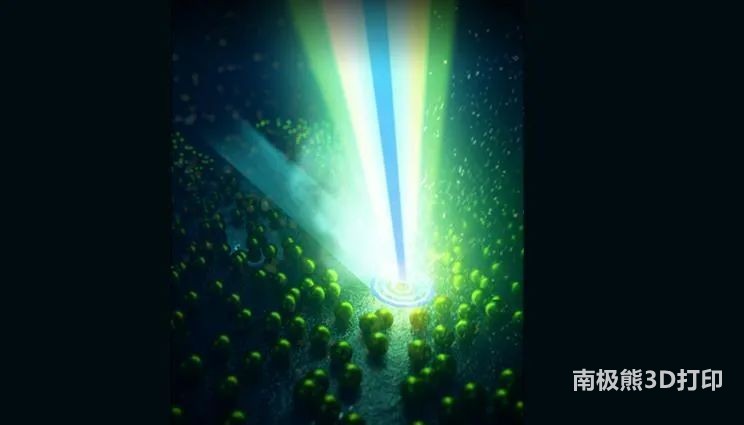
This work shows that alternative shapes such as Bessel beams can alleviate the main problems in LBPF technology-laser and
mineral powder
When they meet, there will be a large thermal gradient and an unstable complex molten pool. These problems are mainly caused by the Gaussian beam shape output by the high-power laser system.
Tumkur Umanath, a research scientist at LLNL and the lead author of the study, said: “Using Gaussian beams is particularly like cooking food with flamethrowers-it is difficult to control the heat deposition around the target material. Using Bessel beams, we can transfer part of the energy Redistributed from the center, which means that we can design the thermal profile and reduce the thermal gradient to help refine the microstructure and eventually form a smoother surface and denser components.”
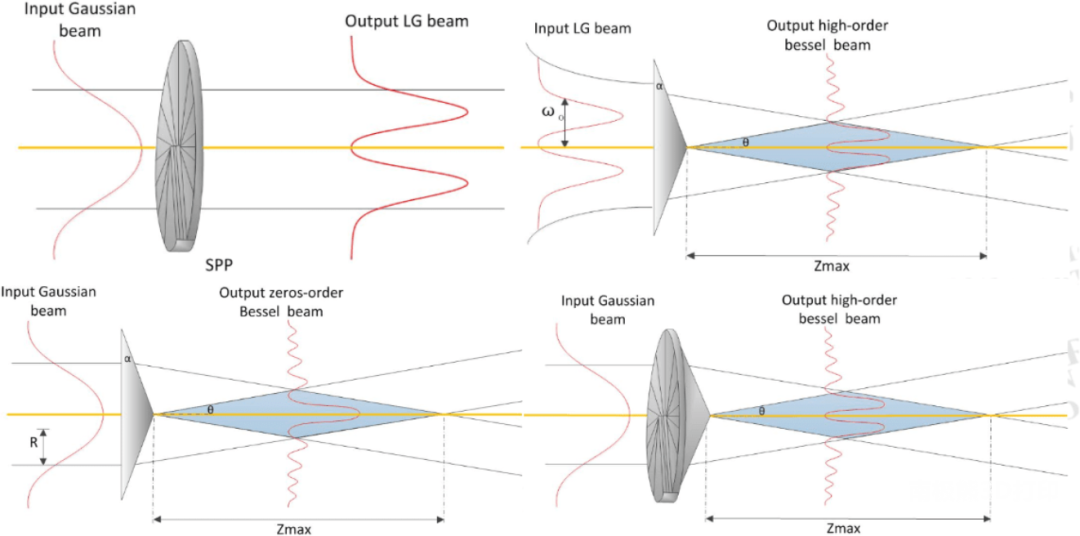
The Bessel beam surpasses the traditional Gaussian beam shape, significantly expands the laser scanning parameters, and avoids many problems caused by the traditional beam. The expected result of the study is that the molten pool will not be too shallow, and there will be no keyholes. In the traditional beam, the laser will generate strong vapor and form a deep cavity in the metal substrate during the construction process. The keyhole will generate bubbles in the molten pool, forming pores, resulting in a decrease in the mechanical properties of the finished part.
Another disadvantage of traditional beams is that they are easily diffracted when propagating, while Bessel beams provide a greater depth of focus due to their non-diffraction characteristics. The researchers observed an increase in the placement tolerance of the workpiece relative to the laser focus when using the Bessel beam. For industrial systems, mounting is a challenge because industrial systems usually rely on expensive and sensitive techniques to position each layer of metal powder within the focal depth of the focused beam as it is deposited.
Tumkur explained: “Bessel beams have been widely used in imaging, microscopy and other optical applications due to their non-diffraction and self-healing properties, but beam shaping has not yet been popular in laser manufacturing applications. Our research has solved metal The problem of disconnection between optical physics and material engineering in the field of additive manufacturing is achieved by integrating and designing the beam shape to control the dynamics of the molten pool.”
The LLNL team “shaped” the beam by passing the laser through two conical lenses, and then let it pass through other optics and scanners to form a ring around the central beam.Researchers use a commercial printer in the laboratory, using the experimental device
Stainless steel powder
Cubes and other shapes are printed in the end. Through high-speed imaging, the researchers studied the dynamics of the molten pool and observed that the turbulence of the molten pool was greatly reduced and the “spatter” was alleviated. Spattering refers to molten metal particles flying out of the laser path, usually leading to the formation of pores.
In mechanical research and simulation, the team found that parts built with Bessel beams are denser, stronger, and have better tensile properties than structures built with traditional Gaussian beams. The project’s lead researcher Ibo Matthews said: “Industry has long sought to improve the ability to control the LPBF process to minimize defects. The introduction of complex structures in the beam increases flexibility and allows precise control of the laser and materials. Interaction, thermal deposition, and final print quality.”
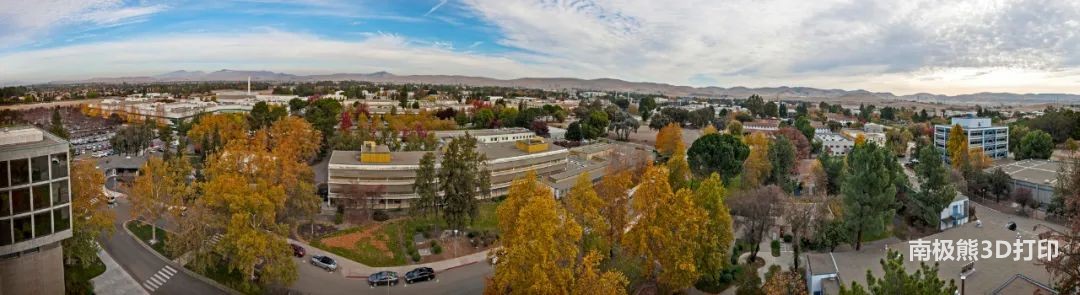
LLNL computer scientist Saad Khairallah used the multiphysics code ALE3D developed by LLNL to simulate the interaction of the laser shape of the Gaussian and Bessel beams with a single trajectory of the metal powder material. By comparing the trajectories, they found that the Bessel beam showed a better thermal gradient than the Gaussian beam, which promoted the formation of better microstructures. At the same time, they also used the Bessel beam to achieve a better energy distribution and avoid the formation of “hot spots” in the Gaussian beam. Once a “hot spot” is formed, an anabolic pool and pores will be formed.
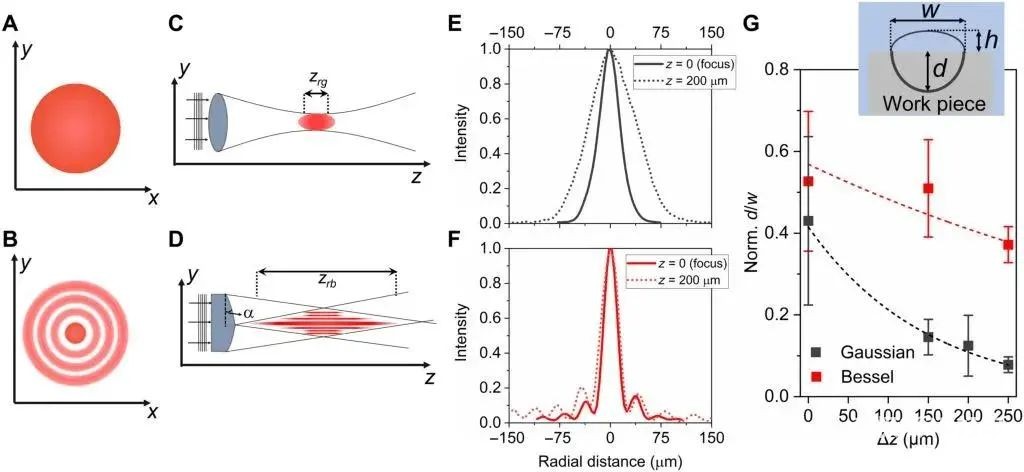
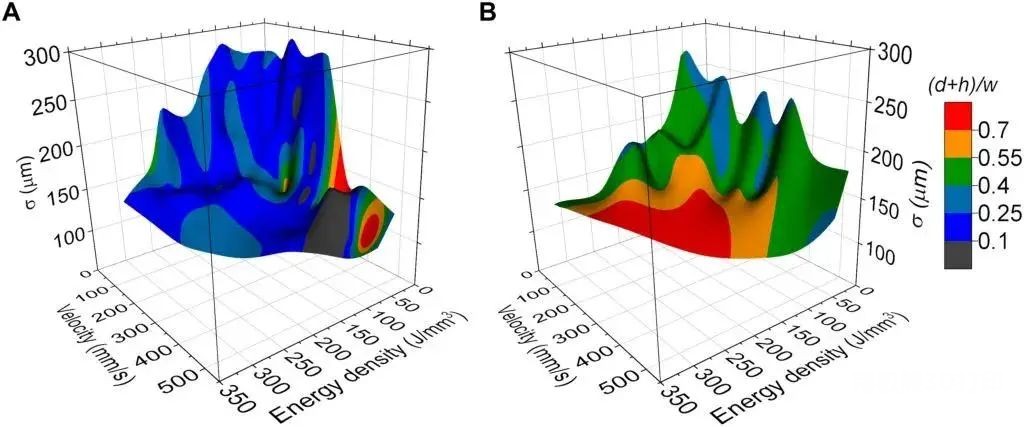
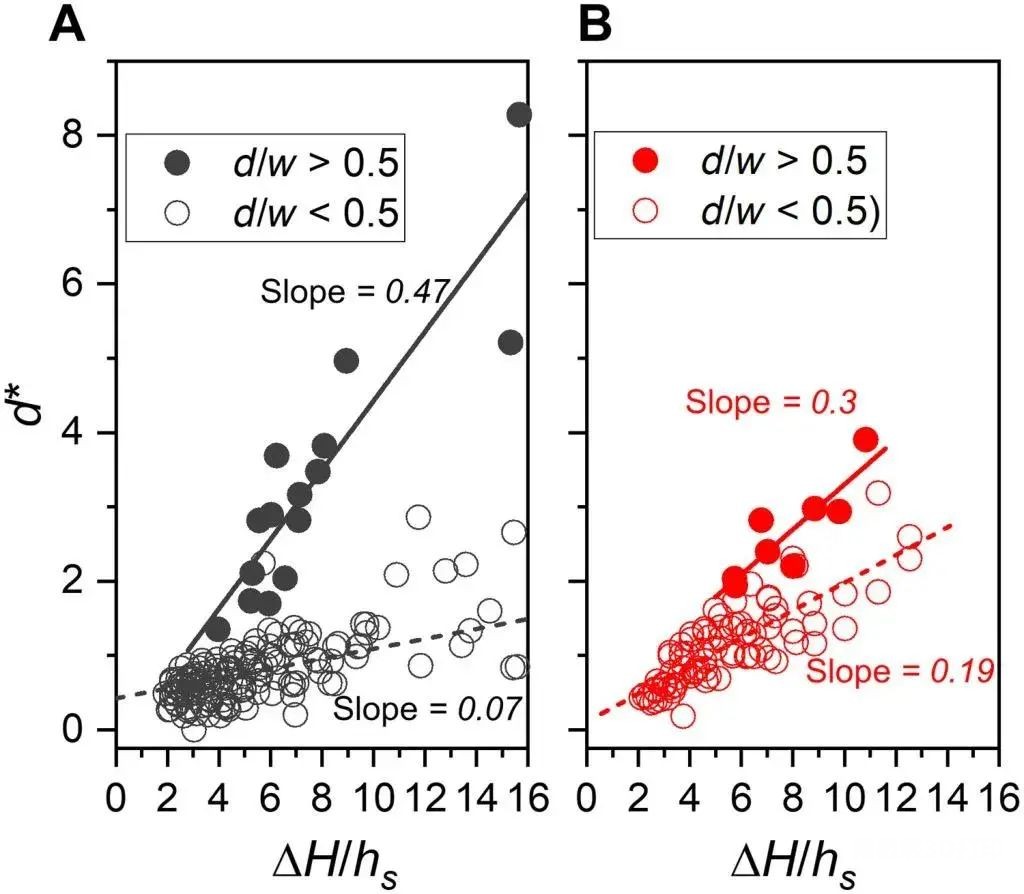
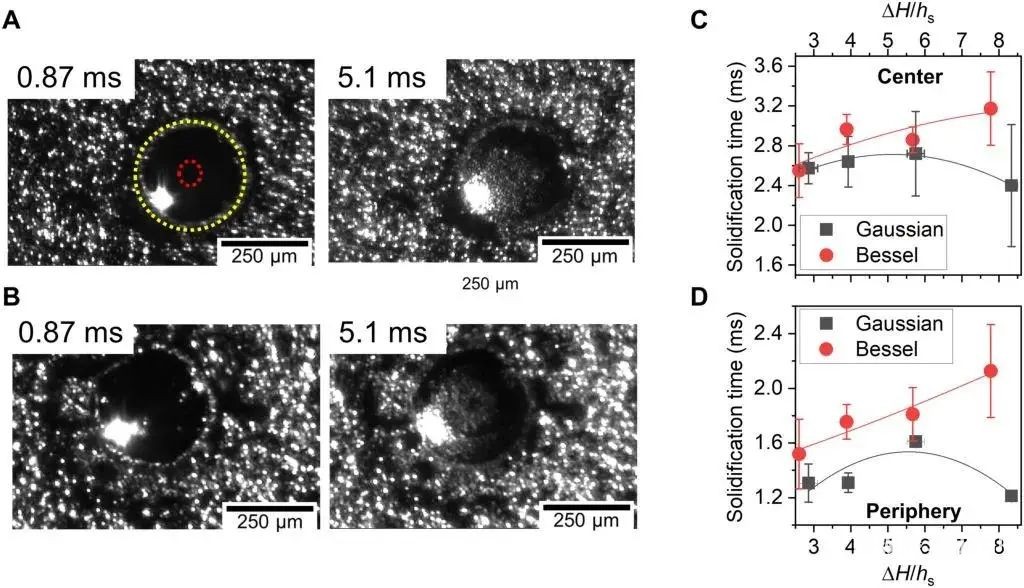
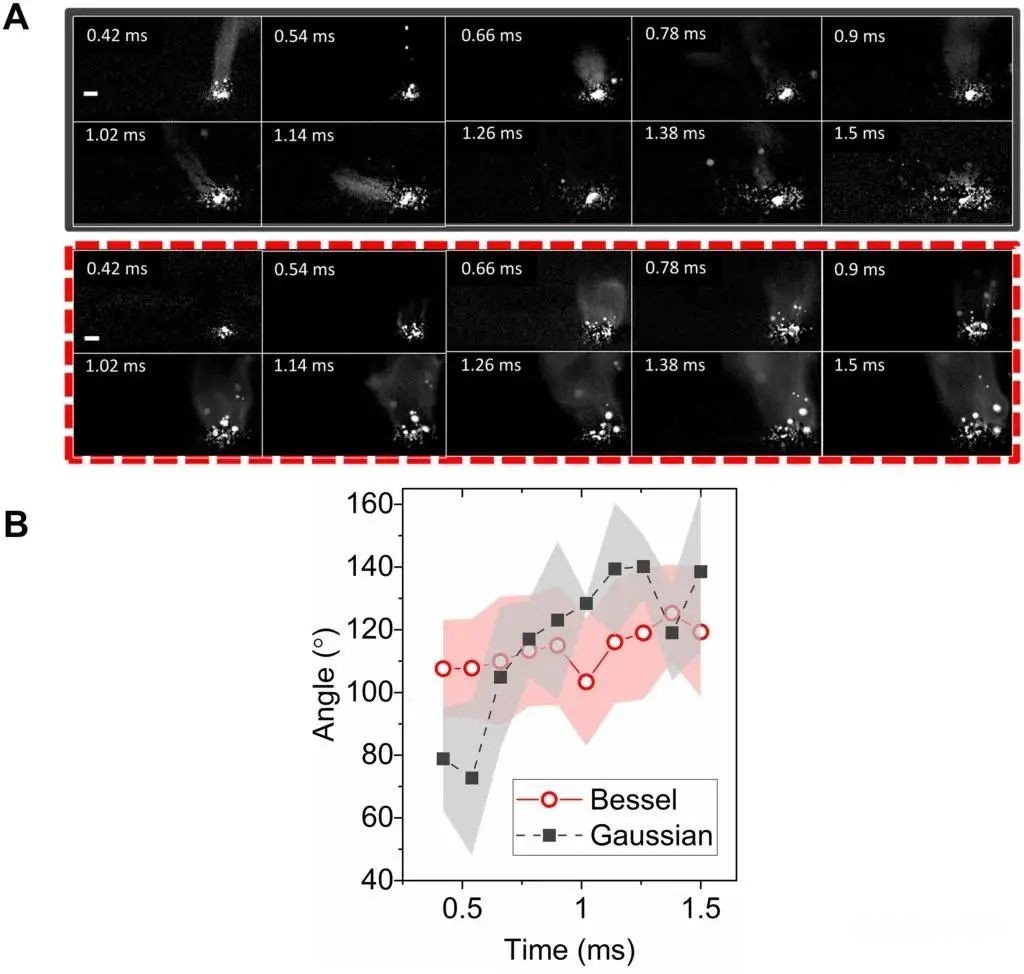
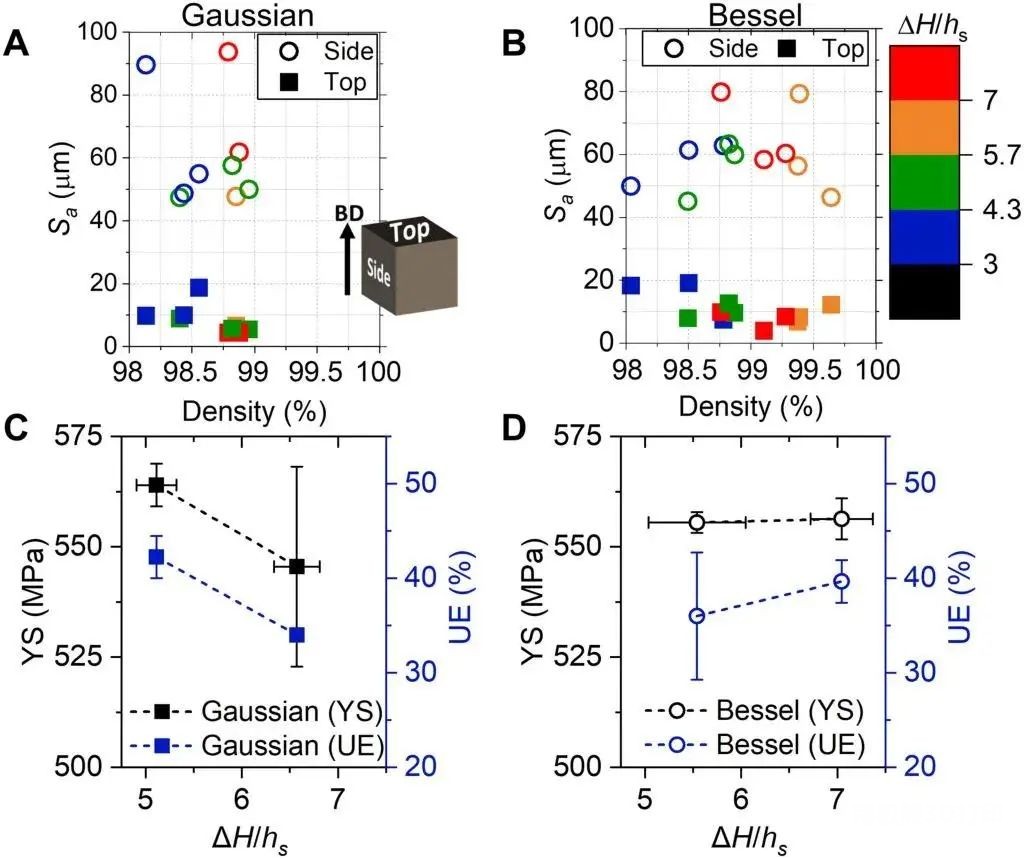
“Beam shaping is just an improvement that LLNL is studying3D printingOne of the many ways of quality of metal parts, this method can reduce the Gaussian beam manufacturing parts usually required by integrating simple optical components.
Post-processing
The cost and shortened time involved in the technology have obvious advantages over the cost of alternate scanning. The production of robust and defect-free parts and the printing of large structures in a cost-effective manner are the general trend.because3D printingReal and industrial
standard
Compatible with, surpassing traditional manufacturing methods, and avoiding the integration challenges brought by alternate scanning technology, it is necessary to continuously explore beam shaping to make it widely used in the printing of various metals and incorporate it into commercial printing systems. “
(Editor in charge: admin)
0 Comments for “Scientists explore the use of Bessel beams to improve pores and defects in 3D metal printing”