A research team at the U.S. Department of Energy’s Argonne National Laboratory has successfully used3D printingComponents expand the recycling of important medical isotopes. The new additive manufacturing parts make the laboratory’s original recycling process (invented in 2015) faster, more reliable, and less costly, making it possible to use the method on an industrial scale.
Radiologists use molybdenum 99 (Mo-99) to detect and diagnose heart disease, bone decay and various rare cancers. Rich molybdenum is essential for the production of Mo-99, and the purchase cost per gram is usually about US$1,000. So far, Mo-99 manufacturers have been unable to economically and efficiently recover molybdenum-rich on a large scale. The Argonne team wants their novel3D printingThe equipment can improve the efficiency of the recycling process, allowing manufacturers to produce more Mo-99 from their expensive molybdenum-rich reserves.
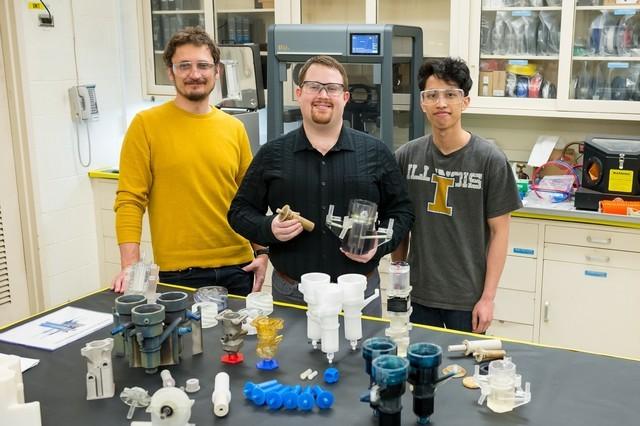
Argonne Research Group and its3D printingContactor photos provided by Argonne National Laboratory
use3D printingRecycling rich molybdenum. The project is led by Mo-99 project manager Peter Tkac. His team first discovered the recycling of rich molybdenum. In the initial process, the research team mixed the used molybdenum-rich chemical mixture into an acidic solution. Then, using funnels and test tubes to purify rich molybdenum in multiple stages, this process is very cumbersome. Tkac said in a press release: “Our original method is difficult to automate.” A full year later, Tkac began to collaborate with Peter Kozak, a researcher at Argonne National Laboratory, and work with others to automate the original process.
3D printingAcrylic contactors replace funnels and test tubes for corrosive chemicals used in the containment and transfer process. The research team claims that it is these contactors that make the recycling process faster and more cost-effective. Kozak explained: “We print each contactor as one piece, with simplified functions and fewer external connections.” “This allows us to push the liquid into the system as quickly and reliably as possible. ”Although the new equipment can effectively separate the enriched molybdenum from potassium and other pollutants, the team found that due to the low pH value of hydrochloric acid, after 15 hours of operation3D printingThe acrylic is corroded. Kozak added: “Our experiment was successful, but if you want to enter the full-scale production phase, the material life you need will be longer than this.
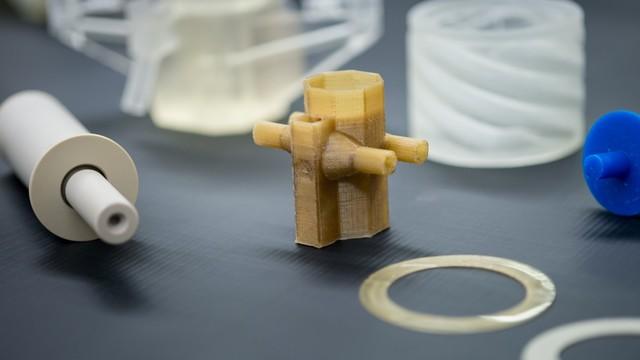
3D printingContactor photos provided by Argonne National Laboratory
The research team for improving the efficiency of PEEK finally decided to use polyether ether ketone (PEEK), a durable polymer known for its chemical resistance.However, in the trial3D printingAfter the PEEK contactor, the research team found that the material shrinks significantly during the manufacturing process, which leads to warping.In order to solve this problem, Argonne’s scientists changed the printer’s fan speed and temperature, and finally succeeded in achieving3D printingThe PEEK contactor is stronger and more flexible than the original acrylic parts. The end result is a faster and more cost-effective concentrated molybdenum recovery system that can withstand harsh chemical conditions for long periods of time. The findings of the project are described in detail in the “Magazine of Solvent Extraction and Ion Exchange” titled “MOEX Process Demonstration for Making Ring Centrifugal Contactors Using Addition”. It is composed of Peter Kozak, Peter Tkac, Kent Wardle, Alex Brown and George Van der Greft ( George Vandegrift) co-authored.
Because of its ideal mechanical and chemical properties, PEEK has become the focus of many medical devices in the past.Medical in the U.S.3D printingThe start-up FossiLabs has previously used porous PEEK material to produce3D printingSkeletal scaffolding structure. The bone structure is designed for long-term implantable medical devices. Elsewhere in Shanghai, a medical device manufacturing company designed and manufactured a PEEK exoskeleton called BioNEEK, which can provide support for various knee problems. Knee pads have dampers, which are designed to absorb shocks that would otherwise be directly applied to the knee joints.
(Editor in charge: admin)
0 Comments for “Scientists use 3D printing to expand isotope recycling”