With the rapid development in recent years, plastic and metal additive manufacturing technologies have been applied in certain industries. However, engineering
ceramics
The additive manufacturing technology is still difficult to strike a balance between material reliability, dimensional accuracy and manufacturing cost.Traditional polymer base
FDM
The equipment usually uses flexible filaments with a fixed diameter, but the mixture of polymer binder and ceramic powder exhibits brittleness at low solid content (30% wt%), making it difficult to prepare flexible ceramic filaments. However, for high-performance raw materials, the solid content sometimes needs to exceed 80wt% or even higher. In ceramic injection molding, this high solid content raw material is usually crushed into pellets, conveyed by screw extrusion, and heated and extruded to finally obtain dense and uniform filaments at the nozzle. For ceramic injection molding, the selection of organic binders, the preparation of raw materials, the methods and equipment for debinding and sintering have been deeply researched and successfully developed for decades. This knowledge can be used to optimize the process parameters of the screw-based printing equipment, which is equipped with a screw extrusion device and is suitable for the additive manufacturing of engineering ceramic parts using Al2O3, ZrO2, Si3N4 or SiC powder from micrometer to nanometer scale.
In this work, the author proposes an FDM method based on screw extrusion that is suitable for high solid loading raw materials. The optimized structure parameters and processing window of the zirconia ceramic additive manufacturing screw are determined. The interlayer bonding and mechanical strength of sintered ceramics were evaluated. The research results show that the FDM method based on screw extrusion is feasible for preparing ceramic parts with complex shapes.
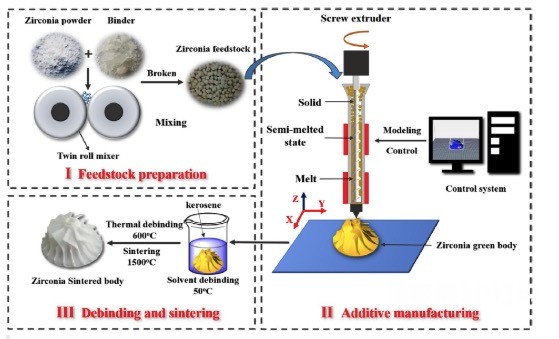
The process of preparing zirconia ceramic parts in this research is shown in Figure 1. First, the zirconia ceramic powder is mixed with an organic binder to obtain a raw material. Then, the raw material board is fed into the barrel through the screw, and then heated, and extruded from the nozzle. The ceramic body is manufactured layer by layer and then degreased in an organic solvent. Finally, dense ceramic parts are obtained through thermal debinding and sintering. The extrusion flow rate is mainly affected by the screw speed and barrel temperature, and is an important indicator for evaluating the performance of the screw extrusion device. When the screw speed is 5 r/min, 10 r/min, 15 r, continuous and stable extrusion effects can be obtained in the range of 130 ~ 190 C. At higher screw speeds (20r/min and 25r/min), raw materials cannot be continuously extruded at 130°C and 25r/min. When the barrel temperature exceeds 150°C, the extrusion expansion effect is not obvious. When the barrel temperature reaches 160°C, the diameter of the extruded wire is almost equal to the nozzle size, which is conducive to higher printing accuracy. This may be because the viscosity of the material becomes lower after the temperature is higher, and the fluidity becomes better. Therefore, the barrel temperature is a key factor in determining the stability of the extrusion line diameter and is very important for printing accuracy.
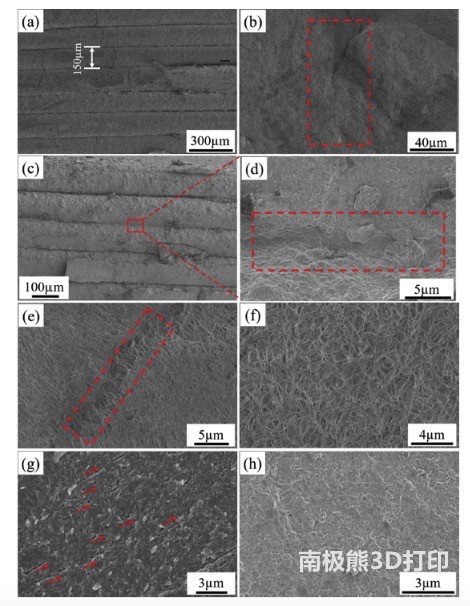
The two main aspects of this research are surface quality and interlayer bonding. The surface quality is directly related to the accuracy of the sintered material and the subsequent processing cost, while the interlayer bonding affects the reliability of the sintered material. The SEM image taken on the surface with a layer thickness of 0.15 mm is shown in Figure 2(a). The gaps between the various layers on the surface are visible, and FDM technology is difficult to avoid. However, estimated from the cross-sectional image, the depth of this interlayer gap is only about 0.1 mm (Figure 2(b)). After sintering with a shrinkage rate of about 20%, the layer thickness becomes 0.1 mm (Figure 2(c)). It can be clearly seen in the enlarged image of Figure 2(d) that the microstructure of the interlayer area and the inner layer The same dense and uniform. The red lines in Figure 2(b) and Figure 2(d) mark the interlayer area of the printed and sintered parts.
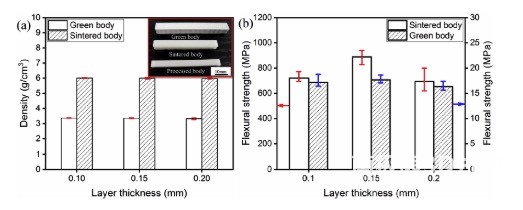
Figure 3 shows the density and bending strength of the green body and sintered body when different layer thicknesses are tested. The layer thickness has no significant effect on the density of the printed and sintered bodies (see Figure 3(a)). The density of the billet is 0.35 g/cm3, which is 58% of the theoretical density of 3Y-TZP, and the density of the sintered billet is about 6.0 g/cm3, which is 99% of the TD. As shown in Figure 3(b), the flexural strength of the blanks prepared with different layer thicknesses reached more than half of the 30mpa flexural strength of the injection-molded blanks, which proved that the interlayer bonding inside the blanks was sufficient. The strength of the sintered body with a thickness of 0.15 mm exceeds the strength of the sintered body with a thickness of 0.1 mm and 0.2 mm, reaching 890 MPa, which is close to the level that can be achieved by dry pressing or injection molding. Further optimization of printing parameters to minimize processing defects and improve the reliability of prepared materials will be carried out in follow-up research.
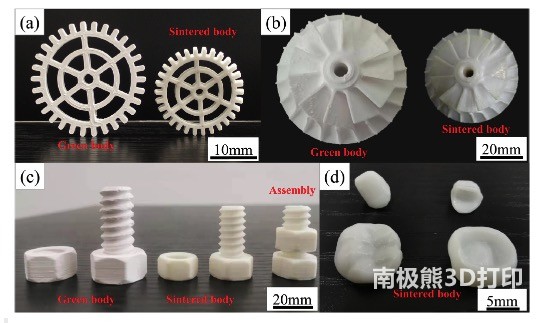
Figure 4 shows some zirconia ceramic parts prepared by the research and development FDM method. The longitudinal linear shrinkage rate of the rectangular bar from the blank to the sintered part is 20.5%. By comparing the geometry of the blank, it is confirmed that the method has a reliable shape-retaining ability (see Figure b)).
The FDM system based on screw extrusion is suitable for printing ZrO2 pellets with high solid content, and has broad application prospects for the additive manufacturing of other engineering ceramics such as Si3N4 and Al2O3. The design screw diameter is 12mm, the aspect ratio is 17:1, and the compact ratio is 2.34. Its strength is sufficient to withstand the shear stress generated during the extrusion process. Through the monitoring of printing temperature, screw speed and nozzle size, the processing window for obtaining stable, precise and controllable extrusion flow and sufficient interlayer bonding uniform structure is optimized. The densities of the zirconia body and sintered zirconia body have reached 58% and 99% of the theoretical density, respectively, close to the level that can be achieved by dry pressing or injection molding. It is verified that the FDM system based on screw extrusion is suitable for the printing of ceramic parts with complex geometric shapes, and the dimensional accuracy is controllable.
(Editor in charge: admin)
0 Comments for “Screw Extrusion Fused Deposition Modeling Additive Manufacturing of Dense Zirconia Ceramics”