Introduction: This article studies the laser-assisted additive manufacturing (LAAM) high-strength steel, using the internal tempering effect to promote the formation of high-content metal carbides (such as M23C6 and M7C3) in the finished sample. The inherent tempering effect helps to obtain better mechanical properties than traditional manufacturing methods in the finished state, and promotes the subsequent heat treatment (HTs) to obtain excellent mechanical properties. The effect of high temperature heat treatment on the microstructure and mechanical properties of materials has been studied on multiple scales. Due to the tempering effect during the deposition process, a large amount of carbides are formed inside. At high temperatures, the high density of dislocations promotes the formation of a large number of nano twins and carbides. The true tensile stress of the high temperature tensile specimen is about 1.81 GPa, and the true strain is about 21%. Compared with the large-scale high-strength steel processed by additive manufacturing and traditional methods, it has obtained an excellent strength-plastic combination. During the deformation process, grain and twin boundary strengthening, precipitation strengthening and dislocation strengthening help to increase the strength, and good plasticity comes from the twin-induced plasticity (TWIP) and deformation-induced plasticity (TRIP) effects, and higher The work hardening rate. This discovery means that by fully understanding and utilizing the IHT effect, AM customized materials can be developed. .
The development of metals and alloys with a combination of high strength and good plasticity is a long-term challenge because of the balance between strength and plasticity. Many approaches have been explored in the development of high-strength steels (HSSs), especially ultra-high-strength steels (UHSS) with ultimate tensile strength >1.5 GPa, which generally require the addition of high carbon (>0.4 wt%) or expensive doping elements (Such as Ni, Co, Cr, etc.). High-carbon additives are one of the most effective and economical methods, but it may cause a decrease in weldability and workability. In addition, the doping of expensive elements increases the cost of materials, which is not conducive to large-scale industrial applications. In recent years, the development of high-entropy alloys (HEAs) provides a promising way to improve the ductility of materials through twin deformation; however, it is difficult for current HEAs to achieve tensile yield strengths exceeding 1 GPa.
Laser-based additive manufacturing (AM) uses high-energy lasers to fuse powder particles together according to a pre-designed CAD model and tool path, gradually forming objects, from points to lines, layers, and finally to 3D components. AM leads to a potential method for the development of high-performance ultra-high voltage devices. A large number of previous studies have established knowledge of the relationship between process parameters, microstructure and performance. Although the deformability caused by high internal residual stress and fine grains is low, the ultra-high-strength steel processed by AM generally has higher strength and hardness than traditional deformed parts due to the refinement of grains. The ultimate tensile strength of the AF9628 low-alloy UHSS produced by AM is as high as 1.4 GPa and the elongation is about 10%, which is the highest among the alloys produced by AM so far. In addition, when the tensile strength of AM processed UHSS exceeds 1.5 GPa, the elongation is usually less than 10%. For example, the AM-treated maraging steel exhibits ultra-high strength of about 2 GPa after heat treatment, while the elongation remains below 5%. The tensile strength of AM-treated H13 steel reaches about 1.7 GPa, and the elongation is only 1.6%.
However, the great potential of using the unique thermal history during AM to develop ultra-high strength steel with good mechanical properties has been neglected. In the AM process, the solidified material will undergo a cyclic reheating and cooling process as it deposits adjacent tracks and subsequent layers. This particular thermal history includes rapid quenching from the liquid state, followed by cyclic reheating, causing a large number of short-term temperature peaks, leading to intrinsic heat treatment (IHT) of the deposited material. Recent studies have shown that the effect of IHT on deposition materials can promote the inherent formation of precipitated phases, adjust the non-equilibrium microstructure, and change the phase composition. For example, during laser deposition of Fe-19Ni-xAl (at%) alloy, due to the IHT effect, NiAl nanoparticles with a size of 2 to 4 nm and a density of up to 1025/m3 are generated in situ.
In addition, in
car
The laser powder bed of the part is fused with more retained austenite to form a horizontal build sample (volume 7%) than in a vertical sample (volume 3%) due to a larger area in the horizontal sample, resulting in a longer time Interval (~160s) melting layer compared to (~55s) vertical layer. Therefore, the horizontal sample allows more time to dissipate heat to the surroundings, resulting in a higher temperature gradient and cooling rate in laser processing. In addition, the unique thermal history in the laser AM process promotes the formation of a dislocation network in AM-treated 316L stainless steel, thereby reducing the strength-plasticity balance.
Here, Tan Chaolin of the Singapore Institute of Manufacturing Technology led a team to study the low-cost AISI 420 high-speed steel using powder injection laser-assisted additive manufacturing (LAAM), in which the internal tempering caused by the IHT effect promotes a large number of internal metal carbides. Formation, and the effect of post heat treatment on the structure and properties of LAMM materials. The increase in metal carbide content after heat treatment and nano-twinning results in a good strength-plasticity combination between a wide range of high-strength steels. The basic mechanism of strength-plasticity balance is clarified, and the ability of IHT to temper deposited materials in situ in AM is highlighted to improve the strength-plasticity combination. Relevant research results were published in Virtual and Physical Prototyping with the title “Superior strength-ductility in laser aided additive manufactured high-strength steel by combination of intrinsic tempering and heat treatment”.
Link:
https://www.tandfonline.com/epri … 452759.2021.1964268
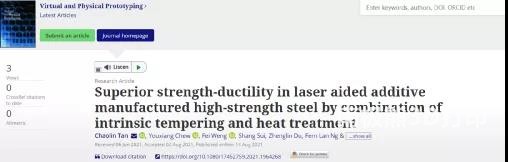
Using spherical AISI 420 powder (Fe-13.78Cr-1.04Mn-0.85Si-0.21C, wt.%), the particle size distribution is D10 = 55.0, D50 = 89.3, D90 = 146.4. The powder has a very low tempering temperature, up to 204°C, which is the ideal temperature to stimulate the IHT effect of the material during the deposition process. The powder morphology is shown in Figure 1a, and the powder particles exhibit a cellular microstructure as shown in Figure 1b. The samples were produced using the powder injection LAAM system developed by the Singapore Institute of Manufacturing Technology (SIMTech). The LAAM process is shown in Figure 1c; 420SS powder is deposited with a constant open space of 0.65 mm and a powder feed rate of 3.3 g/min. Using different laser power (P) and scanning speed (v) for process optimization, the linear laser energy (η) is defined as η = P/v. The raster laser scanning mode that rotates 90° between layers is adopted. The thermal history of using the best process parameters in the LAAM process is recorded by four thermocouples at different positions of the deposited sample (see Figure 1d). .
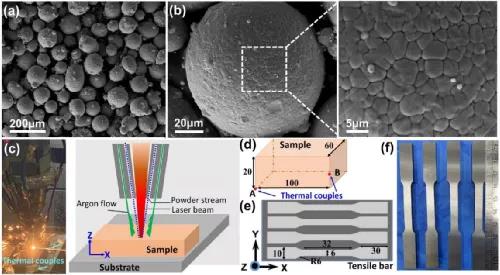
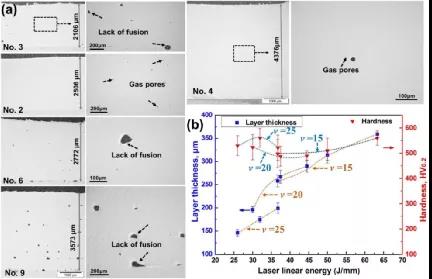
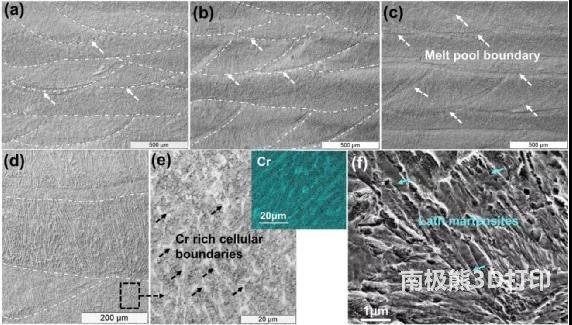
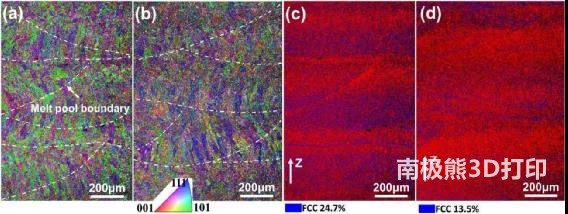
(Editor in charge: admin)
0 Comments for “Singapore Institute of Manufacturing Technology: Laser-assisted additive manufacturing of high-strength and high-plasticity steel!”