guide,3D printingUp to now, many people are still very confused about the status quo of the development of this technology, and some people in the industry will say3D printingThe technology is not yet mature, and some will say that the market demand is insufficient. Of course, with the participation of more and more traditional manufacturing companies, more and more people are optimistic about the deep integration of 3D printing and applications, making imagination a reality.
April 12, 2022, Florida-based
Sintavia
is a company mainly focused on
aviation
aerospace
Applied3D printing servicebusiness, recently announced the use of two AMCM M4K-4Metal 3D Printingmachine, successfully manufactured a large metal heat exchanger. The exchanger is one of the largest monolithic metal parts that can be printed based on PBF technology, and it is also the largest 3D printed exchanger.
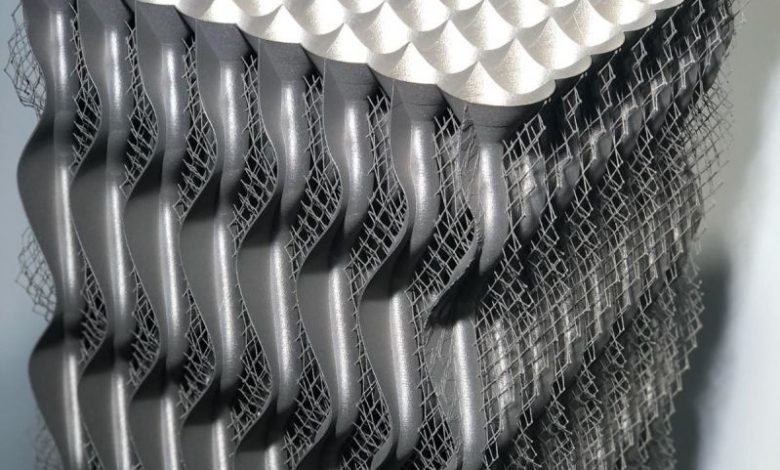
The material used for this exchanger is a marine nickel superalloy, and the entire assembly has external dimensions of approximately 16” x 16” x 39” (approximately 400 x 400 x 1000 mm). The importance of the heat exchange area means that it is manufactured for 3D printing. Design heat exchangers that contain large and densely complex features. This in turn results in very large3D printing modelsfiles, which can make the creation and manipulation of CAD geometry and the establishment of print data time-consuming. With the advanced performance of the M4K-4 device, printing took 12 days, otherwise it could have taken longer.
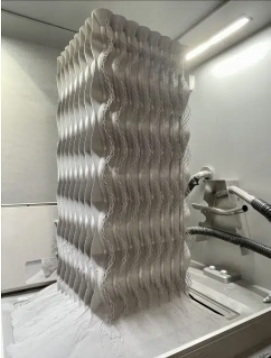
Heat exchangers are ideally suited for 3D printing, allowing design engineers to maximize the surface area of a given volume without compromising the weight of the part.and with3D printerTechnology has developed, and when printers have gotten bigger, people can also make bigger switches.
In addition to AMCM devices, Sintavia also
SLM Solutions
Ordered two 12 lasersMetal 3D Printingmachine NXG XII, they are bigger and faster. Sintavia said that in addition to these benefits of the technology, compared to traditionally designed and manufactured exchangers, by3D printing technologycan achieve up to 2 times the heat dissipation efficiency, reduce the pressure drop by 3 times, and increase the production efficiency by more than 4 times.
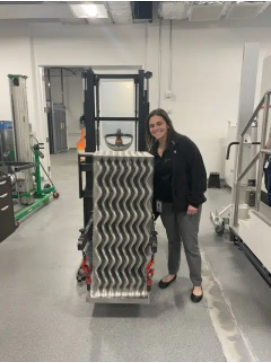
These cooling devices will be integral to future marine engines and open up new possibilities for advancing metal PBF technology to manufacture large, highly complex and complex metal components. The company intends to continue its role as a major manufacturer of propulsion and thermal systems for the aerospace, defense and space industries.
The heat exchanger market is growing rapidly and is expected to grow to approximately $30 billion by 2026. 3D printed heat exchangers are optimizing aerospace, defense, industrial, oil and gas,
car
and products for the racing industry to enhance performance.
(responsible editor: admin)
0 Comments for “Sintavia Metal 3D Prints Large Nickel Superalloy Heat Exchangers, 2X Increased Heat Dissipation Efficiency”