Fiber-reinforced polymers are widely used in aircraft as a lightweight rigid material.
car
as well as
biology
medical
However, composite materials are difficult to recycle and are not conducive to sustainable development. In contrast, light-weight materials in nature, such as bone, silk, and wood, form complex hierarchical structures through directed self-assembly, thereby exhibiting excellent mechanical properties and capable of recycling in nature. In 2018, a research team from the Swiss Federal Institute of Technology in Zurich published a study on thermotropic liquid crystal polymers in the journal Nature.3D printingrelated research, through3D printingThermotropic liquid crystal polymers obtain high-strength, lightweight recyclable parts that self-assemble into core-shell structures[1]. In 2021, on this basis, the team proposed spinning3D printing technologyPrinting liquid crystal polymers[2]. In order to realize the spinning process based on melt extrusion, the research team controlled the feed rate of the polymer, accumulated the molten polymer at the nozzle, and finally pulled out the fibers at a high draw rate. Its printing principle is shown in Figure 1.
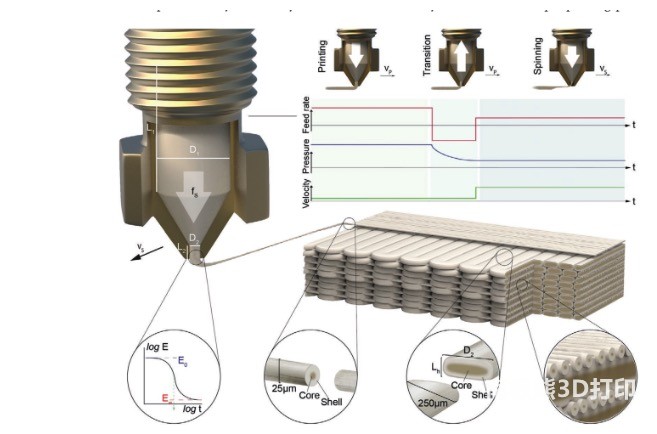
Since the fiber-reinforced laminate fibers formed by spin printing and the matrix material are both liquid crystal polymers, they are fully recyclable. The mechanical properties of the fibers produced by spinning 3D printing decreased with the increase of the fiber diameter. To evaluate the effect of spun-printed fibers on the mechanical properties of cross-laminates, the fiber-reinforced laminates were subjected to longitudinal (0°) and transverse (90°) tensile loads with a fiber content of 7.9 Vvol%. The elongation modulus is increased by 3.4 times and 3 times, respectively. The team also explored the change law of mechanical properties of laminates with different fiber content, and the tensile strength and modulus showed an increasing trend with the increase of fiber content. This spinning printing technique can print fiber-reinforced complex structures as shown in Figure 2, and this structure can be designed to change the fiber content in specific directions to meet the requirements under different mechanical loading conditions. Fiber-reinforced complex structures printed by spinning are fully recyclable and recyclable multiple times.
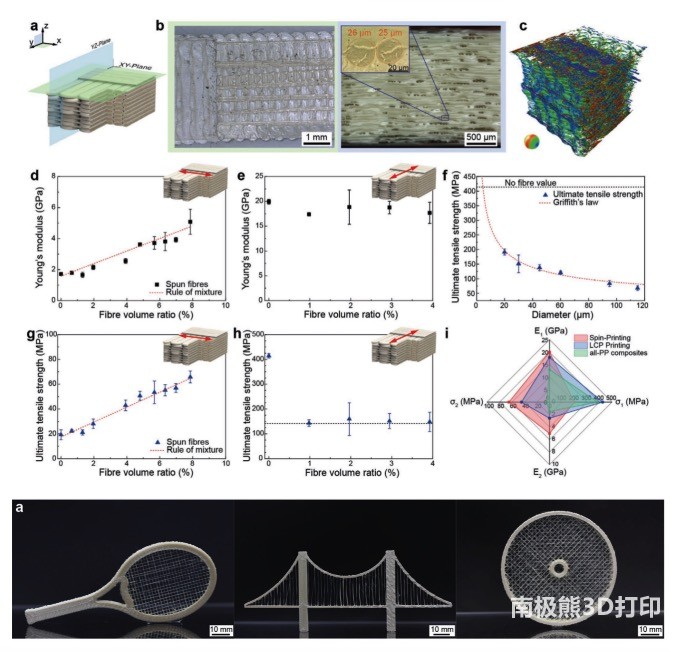
references:
Gantenbein, S., Masania, K., Woigk, W. et al. Three-dimensional printing of hierarchical liquid-crystal-polymer structures. Nature 561, 226
0 Comments for “Spinning 3D-printed liquid crystal polymers to form recyclable full-fiber materials”