Stratasys has partnered with global luxury car brand Radford to manufacture more than 500 Lotus Type 62-2 cars with custom bodywork3D printingComponents. Discovery+ brings this collaboration to the screen, with Ant Anstead bringing the veteran to life in the latest documentary Radford Returns
car
The manufacturer brought it back to the public eye.
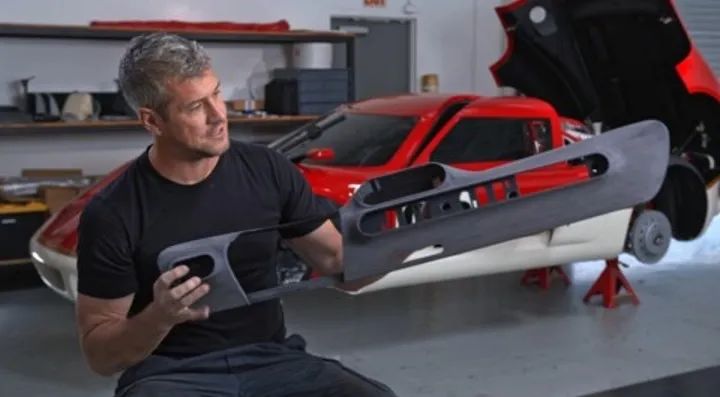
Radford Returns, now available, tells the story of how contemporary technology has reinvigorated body customization, featuring automotive engineer and presenter Ant Anstead and former F1 World Champion Jenson Button, documenting Lotus’ fusion of retro and modern elements The manufacturing process of the Type 62-2 supercar.
This is an excellent3D printing technologycutting-edge applications. Viewers can gain insight into design, prototyping,
mold
During fabrication and final part production, Stratasys
FDM
®, PolyJet™ and Stereolithography3D printing technologyHow to get the perfect application.
“Stratasys 3D printing technology allows us to enjoy the freedom of design and the ability to easily customize some very rare parts for these two prototypes. The new technology enabled by contemporary technology allows us to customize the body to the greatest extent possible.”
-Ant Anstead
To produce the first two cars, Radford Studio, automotive design engineering firm Aria Group, and the Stratasys Direct Manufacturing team 3D printed more than 500 parts.With Stratasys GrabCAD Shop™ Workflow
software
the Radford team was able to schedule and track its 20 different3D printer– A true demonstration of distributed manufacturing.
They deployed Stratasys F900®, F770™, Fortus 450mc™, F370® and J55™ 3D printerdifferent printers can achieve different expectations and effects.
“By introducing 3D printing technology in the workshop, Radford can build a 1960s supercar in the 21st century, high-end, ultra-custom, and with the features that customers expect in a sports car of this class. This is common in the automotive industry. Phenomenon: Everyone who buys a new car wants more customization. 3D printing can make that happen.”
—Pat CareySenior Vice President, Strategic Growth, Stratasys
By utilizing different 3D printers and technologies, the team was able to manufacture large composite parts such as automotive firewalls. This part was made on a Stratasys F900 printer using ULTEM™ 1010
Resin material
Printed in two halves, then glued to form a whole, and then wrapped with carbon fiber prepreg without the use of layup tools.
The firewall’s design includes the complex mounting structure required for the in-car speakers, a fuel filler mount and luggage compartment racks. Additionally, many exterior body parts are printed in FDM® Nylon 12 Carbon Fiber and ASA materials, such as side mirror housings, radiator ducts and body vents. Considering many factors, such as strength requirements, tight project schedules and the need for extreme design freedom, a large number of mounting brackets on the vehicle are also made of FDM Nylon 12 CF.
“In reopening Radford, we only intended to work with world-class companies. Both Lotus and Radford are international companies, and when we wanted to 3D print parts, we chose Stratasys, which is also an international company.”
-Ant Anstead
Stratasys will continue to support the Radford Lotus Type 62-2 project, enabling the company to 3D print production parts using a variety of 3D printing technologies including FDM®, SAF™, stereolithography and P3™ programmable photopolymerization.
About Radford
Radford is a global luxury car brand rooted in the UK, focusing on creating trendy cars with classic designs. Founder Harold Radford has created countless custom vehicles, and Radford has inherited his heritage and craftsmanship to provide customers with luxury custom bodies and personalized vehicles.
(responsible editor: admin)
0 Comments for “Stratasys and veteran luxury car maker Radford recreate the Lotus Type 62-2 sports car”