Although technological advancement has allowed the robotics industry to develop rapidly, the ones that really enter daily life are limited to intelligent sweeping robots, which are far from the robots we see in science fiction films. Glenn Garrett, chief technology officer of NASA spin-off company Amorphology, said that there are two main reasons for this situation: cost and safety.
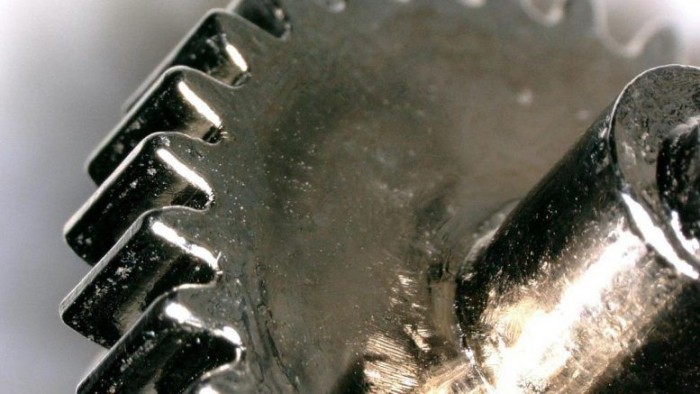
Most automated machinery is still only those that can carry out majorinvestAnd expect long-term savings for large manufacturers to be able to afford it. Although robots occupy more and more factory floors, for safety reasons, they are usually isolated from human colleagues-basically ignorant of their surroundings, they are strong and clumsy.An important breakthrough in reducing the cost of robots is metallic glass, which can be used to synthesize hard and smooth surfaces using 3D printing technology. This allows the metallic glass gears to have a long service life without the use of liquid lubricants, which makes them attractive to NASA robots operating in cold environments. Previously, in this environment, the lubricant needed to be heated before operation.
Every time NASA’s Curiosity rover crosses Mars, it takes about three hours to heat up the lubricating oil for its gears.To help future rover save time andenergy, NASA invested in large pieces of metallic glass for gears that do not require lubrication.Garrett said: “This is the direction of the robotics industry.” Now, Pasadena, California-based Amorphology hopes to reduce the price of collaborative robots through initial advances made for robots that have never been used for human interaction (NASA’s planetary rover).
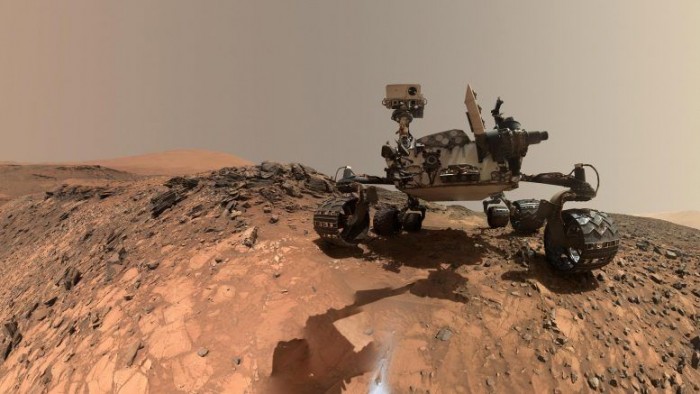
The gears on the NASA rover, like most gears on the earth, are made of steel, which is strong and wear-resistant. However, steel gears require liquid lubrication, and oil does not work well in cold environments such as the surface of the moon or Mars. So, for example, NASA’s Curiosity rover spends about three hours warming up the lubricant every time it is ready to roll, consuming about a quarter of the available energy that would otherwise have been used in science. .Focusing on solving this and other materials-related issues, in 2010, the Jet Propulsion Laboratory hired Hofmann, who was a research scientist at the California Institute of Technology at the time, with a background in materials science and engineering.NASA at the Jet Propulsion LaboratoryFundingA new metallurgical facility was established to explore alternatives to gears and develop new metal alloys.
Since he managed the Jet Propulsion Laboratory at the California Institute of Technology, Hoffman has been familiar with a new class of special engineering materials called bulk metallic glass, also known as amorphous metals. These are metal alloys that can be rapidly cooled from liquid to solid before their atoms form a lattice structure common to all other metals. On the contrary, the atoms are arranged randomly like glass, giving the material properties of glass and metal.Based on their constituent elements-usually including zirconium, titanium and copper-they can be very strong, and because they are not crystalline, they are elastic.Hoffman explained that most compositions will also form hard, smoothceramicsOxide surface, and pointed out that these characteristics together make gears made of some amorphous metals have a longer service life without lubrication. This is very important to NASA because you can run the gearbox without lubricating it.
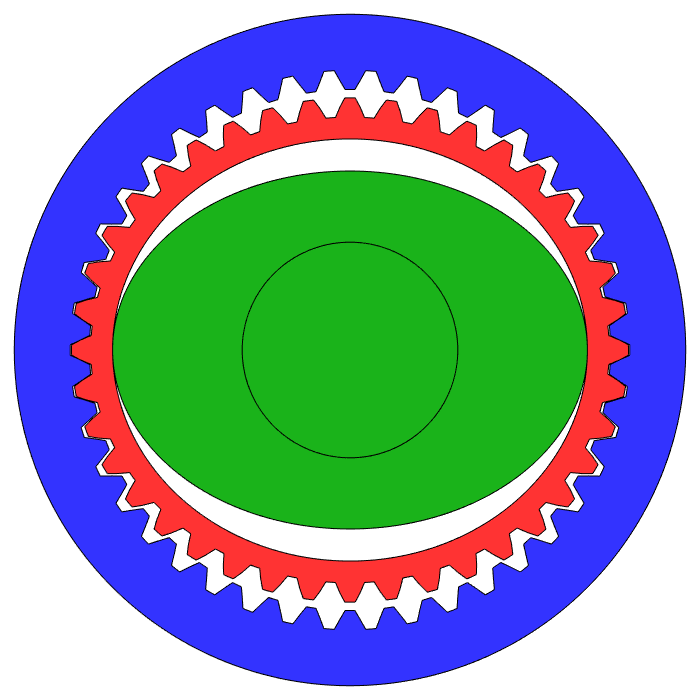
But amorphous metals have another characteristic that makes them attractive to gears on the earth: “These alloys are designed to have a low melting point, because in order to make metallic glass, the alloy must be cooled faster than its crystallization rate. “Hofmann said. This low melting point, coupled with their natural strength and the fact that their volume hardly changes during curing, makes large pieces of metallic glass easy to use for injection molding, which can significantly reduce the cost of manufacturing gears and other parts.
Hofmann said that this is where the use of amorphous metal for forming can bring the greatest savings: its cost is about half the cost of machining strain wave gears from steel. Forming small, high-performance planetary gears and strain wave gears has become the core business plan of Amorphology, which Hofmann co-founded in 2014. Through the California Institute of Technology, the company obtained a number of technology patents he developed for NASA.
(Editor in charge: admin)
0 Comments for “The “super power” of 3D printing metallic glass-it can run a Mars rover and build a robot”