On April 21, 2020, researchers from the University of Edinburgh used FDM 3D printingTechnology has produced a low-cost electrojet/electrospinning device for biomedical applications.
Although different technologies are used, both electro-jet and electro-spinning technologies use similar techniques to produce nanostructures. Electrospinning technology can produce polycaprolactone fibers with a diameter of about 100 nanometers. On the other hand, electrospray ionization (ESI) is used to prepare nanospheres and nanoparticles. However, a typical laboratory electrospinning equipment can have both electrojet and electrospinning modes.
Researchers from the School of Engineering at the Institute of Materials and Technology of the University of Edinburgh found that although the commercialization of electro-jet and electro-spinning methods is quite simple, the cost is between 17,000 and 300,000 US dollars. Therefore, many researchers have adopted unsafe homemade solutions. Researchers developed and shared an FDM
3D printingThe technology enables it to manufacture safe and modular EFI/E-spinning equipment.
What are electrospinning and electrospray technology?
Electrospinning technology is a fiber production method. Electrospinning technology uses the power of electricity to pull out the charged wires of polymer nano/ultrafine fibers. It is a method widely used in pharmaceutical, medical or biological applications, such as scaffolds for tissue engineering or creating nanofiber wound dressings. The researchers further explained: “It is also widely used in medical diagnosis and drug delivery because they can fix identification elements or active pharmaceutical ingredients. Because of their large surface area and porosity, they are also widely used in medical diagnosis and drug delivery. “
Electrospray technology, also known as ESI, can generate ions, that is, atoms or molecules with a net charge. To achieve this goal, the technology uses an electrospray device to apply high voltage to the liquid to generate an aerosol. The electrosprayer itself is an instrument that uses electricity to disperse liquids. Electrospray nanoparticles are usually used in the pharmaceutical, biological or medical fields. For example, electrospray can be used to manufacture drug-loaded nanoparticles for nanoparticle drug delivery, or to load cell growth factors for tissue engineering.
Both of these methods use electro-hydrodynamic mechanisms to produce nano/micro particles and nano/micro fibers. Therefore, it is possible to make a combination set that makes the use of these two technologies possible, each mode depends on the viscosity and conductivity of the solution. As the researchers described in the study, the general setup includes “(i) a syringe placed in a syringe pump for continuous solution flow; (ii) a metal nozzle; (iii) a high-voltage power supply (connected to To the nozzle); (iv) and a collector (electrically conductive to attract charged nanoparticles/nanofibers and placed on the opposite side of the high-voltage electrode).
For electrospinning and electrospray modes, the liquid ejected from the nozzle forms a specific cone geometry, called Taylor cone. In the electrospray mode, highly charged droplets are ejected from the Taylor cone. After the solvent evaporates, solid nanoparticles can be collected. In the electrospinning mode, continuous fibers are ejected from the Taylor cone, and after the solvent is completely evaporated, the nanofibers will solidify.
However, the researchers explained that although the commercial equipment of electro-spinning and electro-jet technology is easy to manufacture, it is expensive. Therefore, many researchers in the world use self-made experimental setup equipment, and users may receive electric shocks in high-voltage components. .
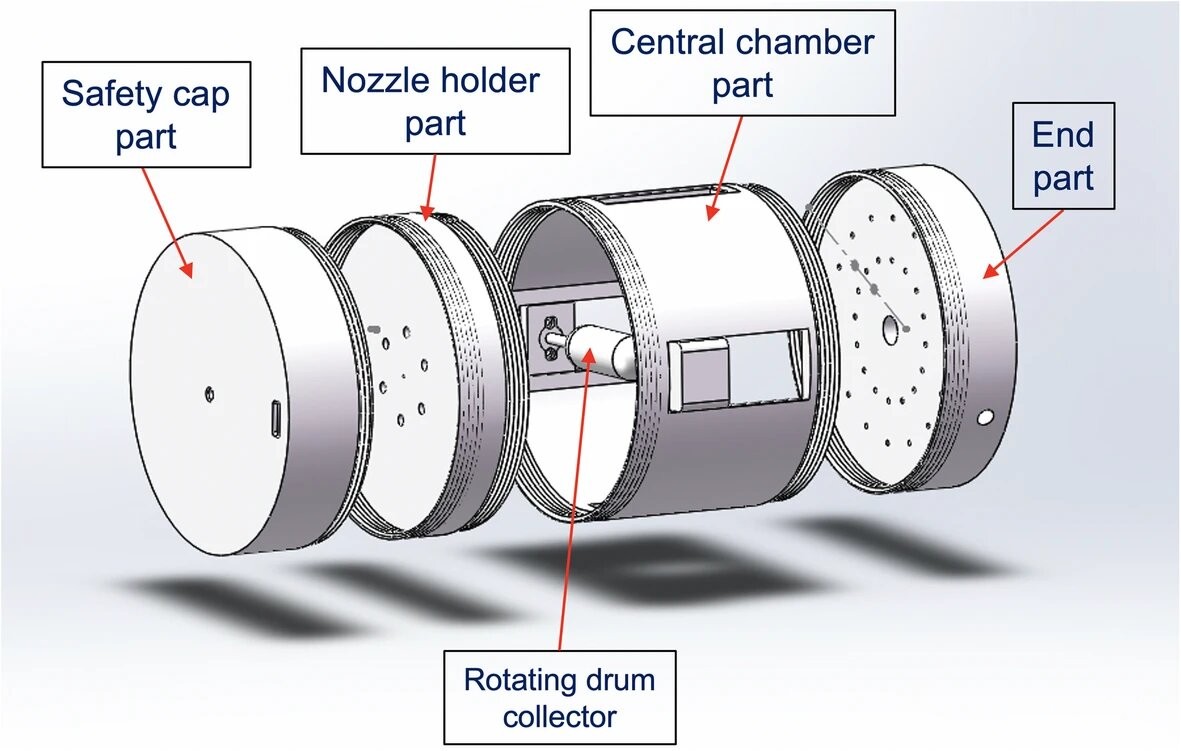
use3D printingCreate a safer and cheaper alternative
In this regard, the researchers believe that FDM
3D printingIt is a suitable and low-cost solution that can produce EFI/E-spinning equipment comparable to commercialization, and the reliability and reproducibility of the results are similar to those of commercialized equipment. In their research paper, they gave a comprehensive overview of the manufacturing process of the setup, and at the same time provided the files and parameters required by the printing device for free. Its design is a modular design, its components can be easily replaced, and the design also provides a safe setting to ensure that users will not come into contact with high-voltage components.
They use Ultimaker 3 FDM system for3D printing, The materials used include PLA, PVA and a thermoplastic elastomer wire, the material cost is 100 US dollars.3D printingThe parts that come out include nozzle holders, safety helmets, central cavity parts, and end parts with internal gas passages.
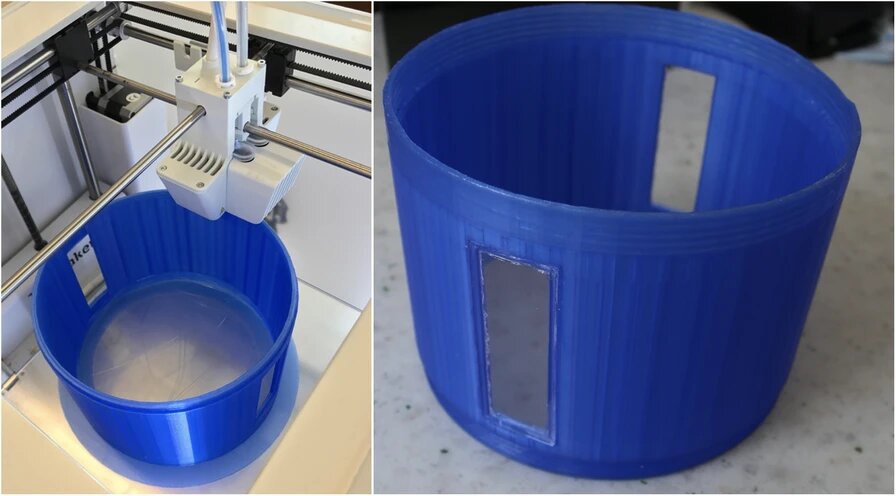
In general, this EFI/E-spinning device was completed in 6 days3D printing.After completion, the researchers successfully tested the device in the electro-jet and electro-spinning modes, but they suggested that3D printingABS, PEEK or ceramic materials are used in the central cavity to increase the chemical resistivity.
The author of the paper believes, “3D printingProvides a low-cost method to manufacture a safe and reliable experimental device similar to commercialization. This article proposes a cheap FDM 3D printingmachine3D printingMethod of modularized electrospray/electrospinning device[……….], The device has been successfully tested in both electro-jet and electro-spinning modes. “
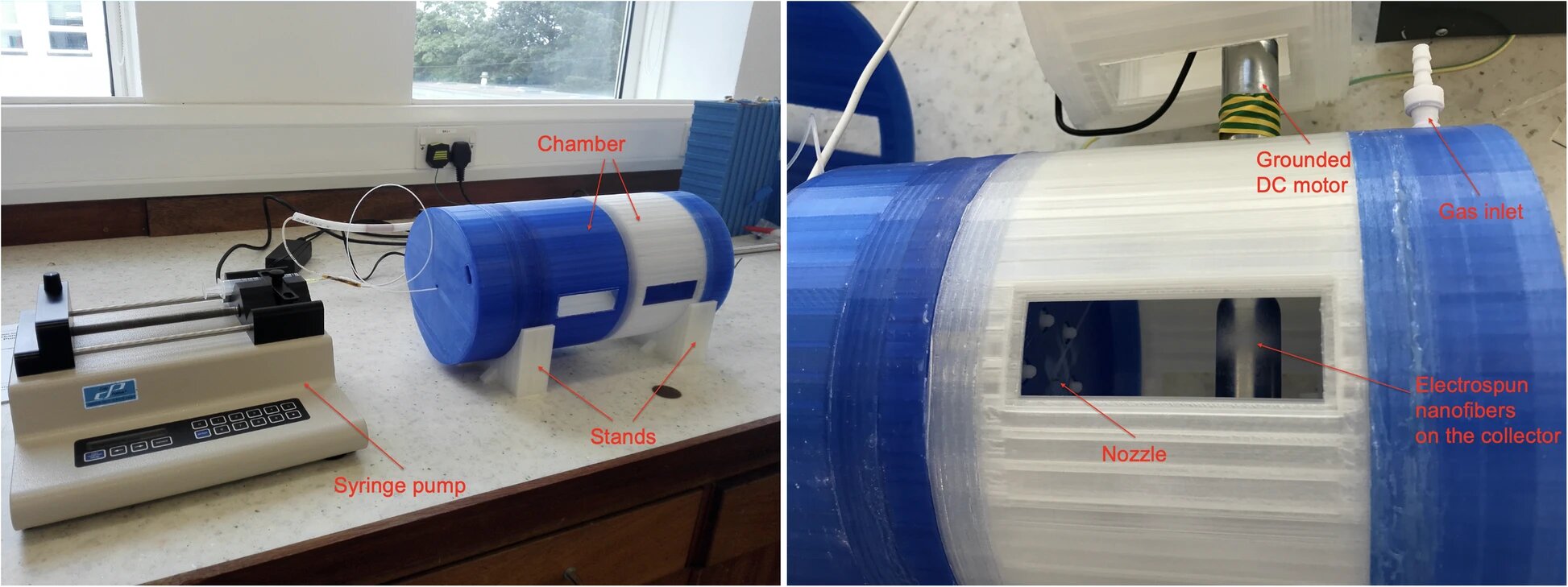
Research Papers”
Low-cost FDM 3D-printed modular electrospray/electrospinning setup for biomedical applications
“Published in the “3D Printing in Medicine” magazine. The paper was written by Jing Huang, Vasileios Koutsos and Norbert Radacsi.
(Editor in charge: admin)
0 Comments for “The University of Edinburgh uses FDM 3D printing technology to manufacture low-cost electro-jet and electro-spinning devices”