We know that additive manufacturing has had a huge impact on research and industrial production in many fields, but so far, the use of additive manufacturing to produce ultra-high vacuum systems has proven difficult to achieve, and is generally considered impossible. In April 2021, in a paper published in the academic journal Additive Manufacturing, the world’s first ultra-high vacuum chamber realized by additive manufacturing method was successfully created, which can work under pressure below 10-10mbar. And the total outgassing of additive manufacturing materials does not exceed 3.6×10-13mbar l/(s mm2). The vacuum chamber is made of AlSi10Mg material by laser powder bed fusion technology. Detailed surface analysis revealed that an oxidized, magnesium-rich surface layer was formed on the additively manufactured material. This surface layer played a key role in achieving ultra-high vacuum.
It proves that additive manufacturing (AM) is suitable for the production of ultra-high vacuum (UHV) equipment, which opens up opportunities for rapid prototyping, weight reduction, and enhancement of functions in the entire high vacuum and ultra-high vacuum fields.
The application of ultra-high vacuum systems is very wide, ranging from existing technologies such as photoelectric sensors, cameras, cryogenic Dewars, electron microscopes, and X-ray photoelectron spectroscopy analyzers, to important emerging research fields, such as portable quantum based on cold atoms The sensors all use ultra-high vacuum. AM can promote basic research and technological development in all the above-mentioned fields, because this technology can greatly reduce the size of related UHV equipment, reduce weight, and shorten the development cycle.For example, the UHV chamber developed in this paper is manufactured by laser powder bed fusion (POBF) technology using AlSi10Mg material and weighs only 245 grams, which is more than equivalent
standard
The vacuum chamber is reduced by 70%. This level of weight reduction is crucial to promote the space-based applications of UHV, such as the use of space-borne quantum sensors to conduct experimental research on basic physics.
However, despite recent progress in metal AM processing, no one has yet to use AM technology to create a complete UHV chamber. The challenge for UHV chambers to achieve excellent performance is: surface roughness, porosity and limited hardness. Rough surface can lead to an increase in outgassing rate. Large porosity may cause leakage or virtual leakage due to the existence of “dead space”. Insufficient ultimate hardness will reduce the effectiveness of the knife edge sealing at the vacuum joint.
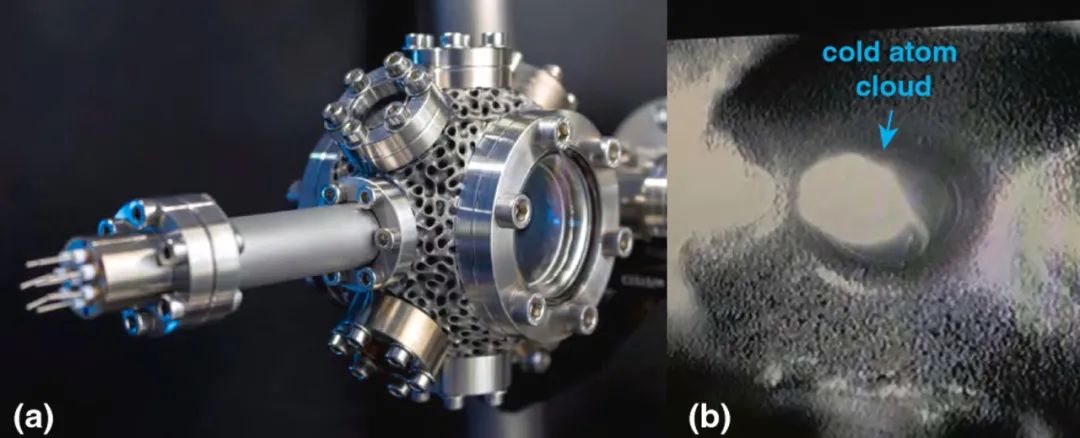
These properties of AM metal make researchers wonder whether it is suitable for making UHV parts.Compared with metals such as titanium alloy stainless steel, AlSi10Mg alloy has a higher thermal conductivity, which may help to improve3D printingTime consistency and reduce build defects. In this paper, the researchers used optical and electron microscopy, mass spectrometry, and X-ray photoelectron spectroscopy to analyze the surface of additively manufactured AlSi10Mg in detail. The analysis shows that the severely oxidized, magnesium-rich surface layer of this AM material can well inhibit the outgassing of the material. Therefore, this vacuum chamber can easily maintain a pressure below 10-10 mbar.
As shown in Figure 1(b) above, this vacuum performance is sufficient for the magneto-optical trap (MOT) to capture the 85RB cold atom cloud. MOT is the basis of almost all experiments and devices based on cold atoms, including atomic clocks for precise timekeeping, high-precision gravimeters used in geology, navigation and civil engineering, as well as navigation and
medicine
Imaging cold atom magnetometer. The application of AM method on UHV equipment will benefit this important emerging field a lot.
bright future
An ultra-high vacuum chamber that can work at a pressure lower than 10-10 mbar was manufactured by the AM method. After several months of operation, no degradation of the chamber performance was observed.
The author believes that the introduction of the AM method into the field of UHV equipment has great potential, which can reduce the size and material consumption of the existing system, reduce the weight, and realize a new portable system with more functions. In addition, AM can also be used to produce elements with high specific surface to improve the efficiency of related vacuum pump devices, such as titanium sublimation pumps. Moreover, it may also be of great significance to study the cause mechanism of magnesium enrichment in the surface layer. This research may also help to further increase the options for AM methods for ultra-high vacuum systems.
For details, please refer to the original paper:
https://www.sciencedirect.com/sc … 21000634?via%3Dihub
(Editor in charge: admin)
0 Comments for “The world’s first 3D printed ultra-high vacuum chamber, 1E-10mbar stable operation, 70% weight reduction!”