With the metal3D printingIt continues to expand globally for industrial users, and the research on materials such as powders, unique alloys and various composite materials is also constantly evolving. In this study, the researchers outlined their findings in their recently published “Strength analysis of Ti6A14V titanium alloy produced by additive manufacturing under static load conditions.” The researchers focused on the use of titanium alloy Ti6Al4V and the adoption of Comprehensive analysis of mechanical properties after printing, direct metal laser sintering (DMLS).
For many applications,3D printingAnd the advantages of additive manufacturing processes eclipse more traditional methods of creating dental implants, rocket engine parts, auto parts and other equipment.While increasing affordability is the key, so is the ability of many users to create parts that have never been available before, or even more notably, you can choose to scan old parts that are outdated and pass3D printingOption to recreate parts. (Particularly useful in automotive and military applications).
Medical devices such as implants are usually made of alloys due to the following advantages:
- High mechanical properties
- Low density
- Corrosion resistance
- Biocompatibility
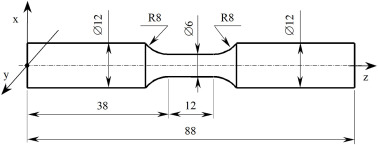
Heat treatment is common when using metals because it can improve mechanical properties. Methods such as hot isostatic pressing (HIP) are usually used. However, in this study, the researchers used DMLS additive manufacturing technology to fabricate samples to test their viable mechanical properties.
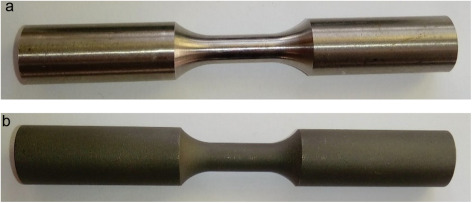
The team created samples in the form of annealed drawn bars (12mm diameter) and created a set of samples through DMLS on the EOS M280W machine, and then annealed them.
“The printing process is characterized by the following parameters: laser power 200 W, minimum layer thickness 30μm, scanning speed up to 7 m/s. The printing direction of the sample is consistent with the Z axis.” The researchers explained.
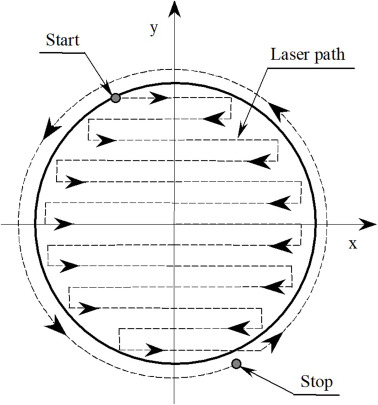
It is found that the strength of the first batch of samples is relatively low, while the hardness-related values are different:
The researchers said: “The difference in results is related to the method of preparing the sample using additive technology and the external load it bears.”
“The hardness value of the unloaded sample on the x-plane changes slightly, indicating that the material produced by the DMLS method has similar mechanical properties.”
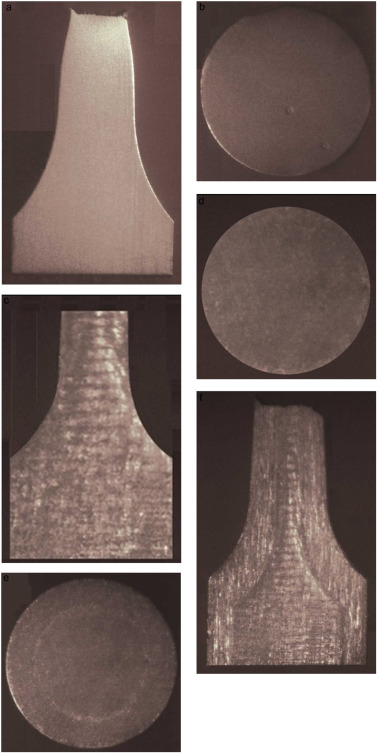
The team of researchers also pointed out that, in this case, the hardness change (between xy and xz) may be due to the material particles3D printingAnd the deformation caused by the axial load.
The test of the macrostructure of the sample DMLS showed significant changes related to the tensile load, indicating that this may also be attributed again3D printingAnd set the parameters and the direction of the material layer. The researchers compared the macrostructure before and after the tensile load, and found that subsequent plastic deformation occurred, and it was clearly visible that it was caused by the load line.
Since titanium is used in many3D printingAnd additive manufacturing processes, so from the use of composite materials to medical devices such as sternum or hip implants, glass printing, etc., this material has been a continuous source of research.
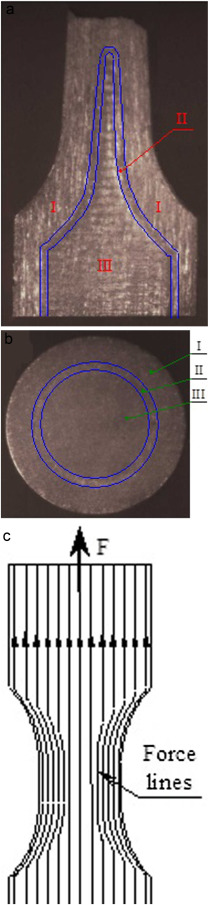
0 Comments for “Ti6A14V titanium alloy: Test DMLS 3D printed samples under static load”