Introduction: This paper conducts a series of powder diffusion and melting experiments to investigate the role of diffusion velocity in laser powder additive manufacturing.
In single-layer experiments, high-speed powder diffusion did reduce the packing density of the powder layers.
However,
The multilayer LPBF process of cubic samples with various high powder propagation velocities was successful, the samples had fewer defects and thus better mechanical properties, especially fatigue life,
This is counterintuitive and has never been reported before. The study found,
Regardless of the powder diffusion rate, the actual powder layer thickness gradually increases due to shrinkage during powder melting, but always reaches a steady state in 10 layers, where the deposited dense layer thickness equals the nominal powder layer thickness, resulting in a similar melting condition and quality.
This study provides unprecedented insights into the role of powder propagation speed in LPBF and corrects the inaccurate intuition that high-speed powder propagation is always bad, which provides a more potential solution to improve the productivity and part quality of LPBF.
Laser Powder Bed Fusion (LPBF), also known as Selective Laser Melting or Direct Metal Laser Melting, is one of the dominant metal additive manufacturing techniques today, enabling the accurate and flexible fabrication of complex near-mesh metal parts.
LPBF consists of two basic procedures: powder diffusion and powder melting. During the powder diffusion process,architectureThe platform is lowered a certain distance (i.e. the nominal powder layer thickness),mineral powderThe particles are spread on the substrate by a scraper/roller. During powder melting, a high power density laser beam is used to selectively melt the powder bed based on CAD profile data. Repeat these two basic procedures until the part is fully fabricated.
Besides achieving good mechanical properties, high productivity is another prominent challenge encountered by LPBF technology.Due to the relatively low processing efficiency, LPBF is mainly limited to the manufacture of high-end components, most commonly in
aviation
aerospace
and
medical
industry. The powder melting process has been extensively studied to improve the quality of manufactured parts by adjusting processing parameters.Among these processing parameters, you can
Reduce build time by increasing laser scan speed, hatch spacing and layer thickness.
However, adverse reactions often degrade part quality. For example, increases in laser scan speed and hatch spacing may unduly increase the number of fusion defects, such as pores, cracks, and globules, as linear laser energy intensity decreases. The disadvantage of using larger layer thicknesses is the reduction in volumetric laser energy intensity, which will result in undesirable features such as lack of fusion and reduced dimensional accuracy. While the laser energy intensity can be maintained by increasing the laser power for complete powder fusion, fusion defects in the metal vapor jet and keyhole would be another issue at high laser power. To our knowledge, so far, this correlation between powder bed quality and manufactured part quality has rarely been investigated and validated.
The National University of Singapore and Huazhong University of Science and Technology conducted LPBF experiments with various powder propagation velocities to fabricate monolayer and cubic samples. Properties such as porosity, mechanical strength and geometric accuracy of the constructed samples were investigated. To account for the counter-intuitive difference between the fabrication quality of the monolayer and cubic samples, further staircase samples were fabricated to reveal the shrinkage and compensation effects behind the layer-by-layer LPBF process. To evaluate the effect of thermal conditions of powder propagation velocity changes, we designed and conducted LPBF experiments with post-powder propagation delay in operation to ensure the same cooling time for different powder propagation velocities. This work aims to provide a comprehensive answer to the question “Is high-speed powder diffusion really detrimental to LPBF’s part quality improvement?” The related research results were published in the top metal journal Acta Materialia under the title “Is high-speed powder spreading really unfavourable for the part quality of laser powder bed fusion additive manufacturing?”.
Paper link:
https://www.sciencedirect.com/sc…422002865#fig0008Is
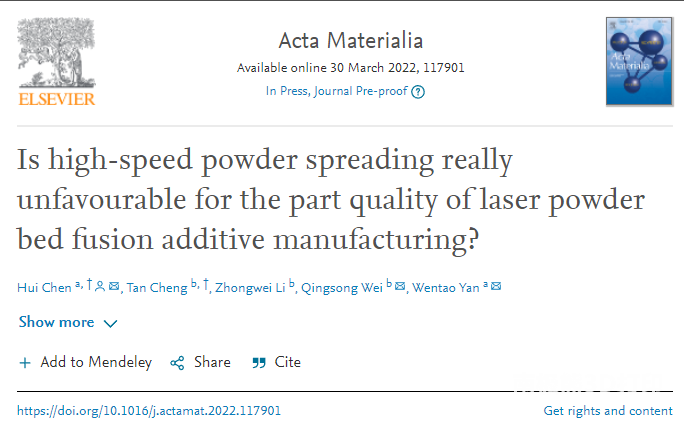
1)
For a given powder layer thickness, higher powder diffusion rates result in lower filler densities and fusion ratios
, for the fabrication of the first few layers, high diffusion rates seem to be inadvisable. However, the actual powder layer thickness increases layer by layer due to shrinkage during powder bed fusion.
This increase in the actual powder layer thickness gradually increases the packing density, thereby increasing the fusion ratio of this layer, which is known as the compensation effect.
Under the combined effect of shrinkage and compensation, the deposited dense layer was able to reach a steady state within about 10 layers with a thickness equal to the reduced height of the substrate (ie, the nominal layer thickness), even with higher diffusion rates. Therefore, the samples can be successfully fabricated with high powder spreading speed and the mechanical properties can be slightly better.
2)
Fusion defects such as pores and cracks are reduced by increasing the diffusion rate, mainly due to the shortened interlayer cooling time.
However, the specific effects of thermal conditions vary with diffusion rates and on microstructure (eg, phase content) depending on material properties.
3)
A major disadvantage of high-speed powder diffusion is the reduced dimensional accuracy of the building direction.
Among the powder propagation speed and laser fluence used in this study, the laser scanning speed is larger, and a constant laser fluence can increase the fusion ratio of the powder layer, thereby reducing the height deviation.
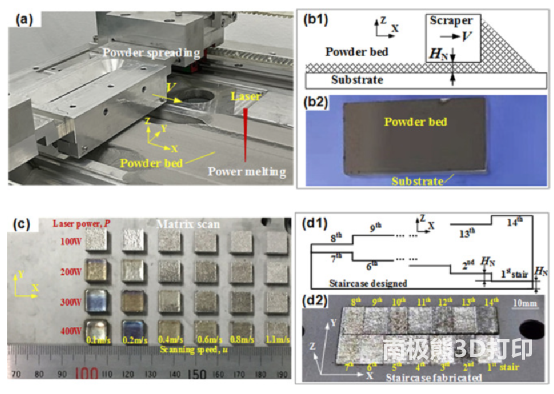
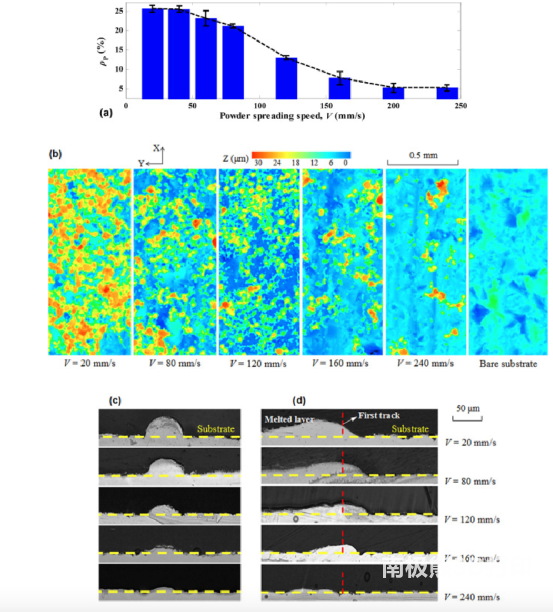
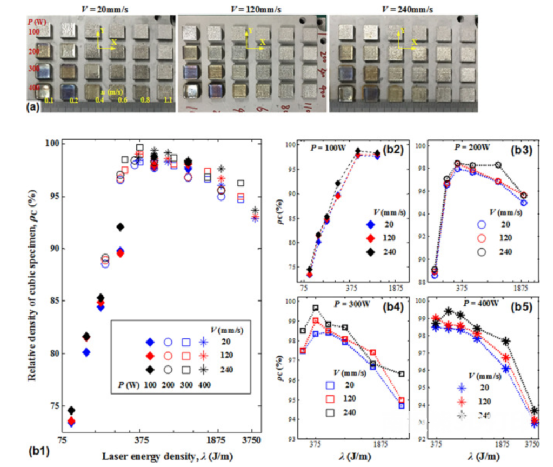
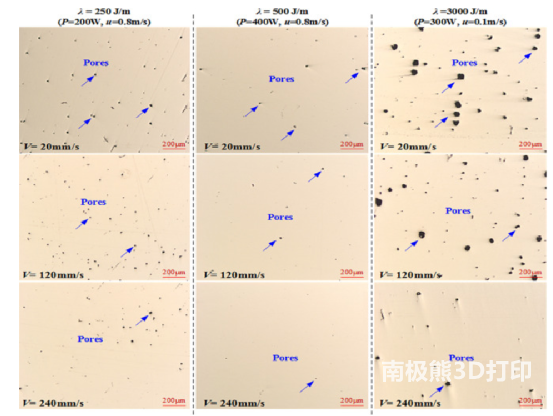
(responsible editor: admin)
0 Comments for “Top Issue “Acta Materialia”: Revealing the Influence Mechanism of Powder Diffusion on the Quality of Laser Powder Additive Manufacturing of Metal Products”