Introduction: On August 3, 2021, researchers from Lawrence Livermore National Laboratory (LLNL) in the United States have begun to use3D printingTechnology to produce flow electrodes (FTEs) for electrochemical reactors is said to increase reactor performance by more than 100 times.It is reported that the process used by the LLNL team is Direct Ink Writing (DIW), which can3D printingA customized porous electrode made of graphene aerogel is produced.This printed structure is essential for a series of subsequent electrochemical reactions, for example, it can convert carbon dioxide and other molecules into usefulenergyproduct.
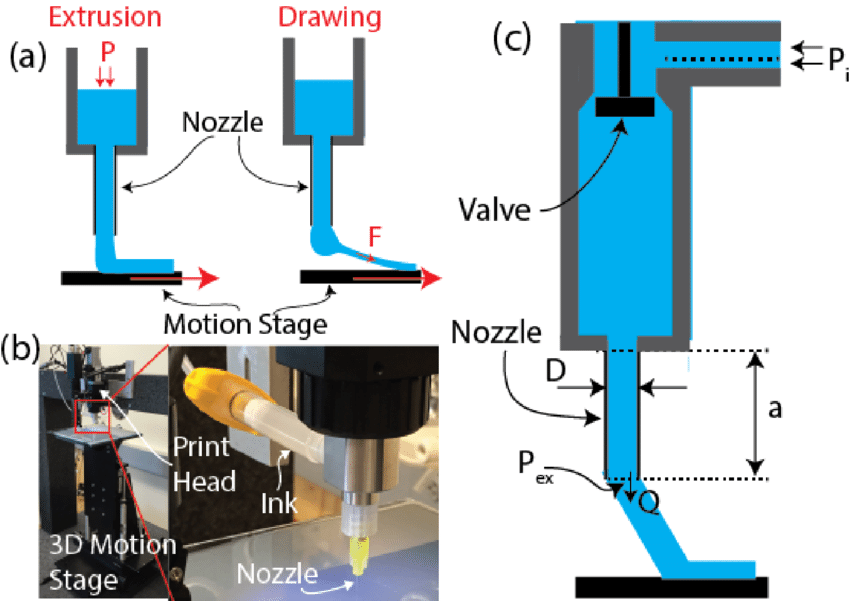
△Direct ink writing
By taking advantage of the design freedom provided by additive manufacturing, researchers have found that they can better control the flow through3D printingFTEs of electrodes. In the context of the use of electrochemical reactors, this may mean maximizing the performance of the transmission medium and reactor.The lead author of this study, LLNL engineer Victor Beck, explained: “Our use of a 3D reactor with precise control of the local reaction environment is a pioneering achievement. The new, high-performance electrode will be the next generation of electrochemical reactions. Important part of the device architecture. This shows how we can take advantage of3D printingThe control of the electrode structure is used to design the local fluid flow and induce complex inertial flow patterns, thereby improving the performance of the reactor. “
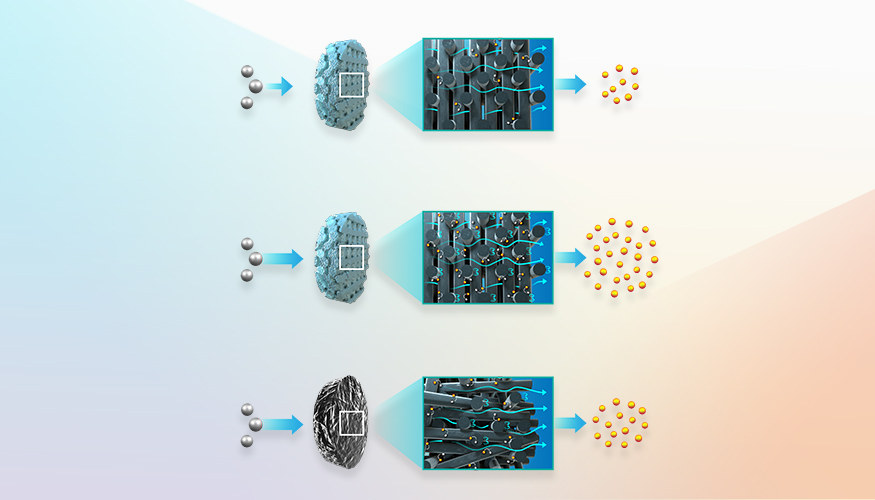
△by using3D printingWith the lattice electrode geometry, the LLNL team was able to maximize the mass transfer in the electrochemical reactor and greatly improve the performance of the reactor. Picture from LLNL
Mass transfer and electrochemical reactor
Electrochemical reactors are often used to convert chemical reactants into a more useful form of energy, namely electricity or fuel. According to the LLNL researchers, the commercial viability of these reactors largely depends on achieving greater mass transfer, which is simply defined as the delivery of fluid reactants to the reaction surface through electrodes. For this, we need FTEs that can control and design flow.
So far, FTEs have been manufactured using “disordered media” such as carbon fiber-based foams and fibers. Although cost-effective, these disordered materials often lead to uneven flow and mass transfer distribution, which is detrimental to the performance of the reactor.
The researchers proved that by choosing3D printingThey can customize the flow channel geometry of FTEs to optimize the reaction in the reactor while alleviating the shortcomings of traditionally manufactured FTEs.
“Achieving fine control of the electrode geometry will enable advanced electrochemical reactor engineering, which was not possible in the previous generation of electrode materials,” added Anna Ivanovskaya, co-author of the study. “Engineers will be able to design and manufacture optimized structures for specific processes. In addition, with the development of manufacturing technology,3D printingElectrodes may replace traditional disordered electrodes for liquid and gas type reactors. “
3D printingGraphene aerogel FTEs
According to reports, the FTEs printed into a complex lattice structure are different from the previous ones.3D printingCompared with the experimental product, it enhances the quality transmission by 1-2 orders of magnitude (10 times-100 times). LLNL’s FTEs also achieved reactor performance comparable to traditional disordered materials, which is a very promising result.
Swetha Chandrasekaran, co-author of the study, said: “Passed3D printingAdvanced materials, such as carbon aerogels, may design macroporous networks in these materials without affecting the physical properties such as conductivity and surface area.”
The LLNL team stated that the success of the research will now allow them to explore the effects of engineered electrode architectures without relying on expensive industrial manufacturing processes. LLNL is currently studying the use of resin-based micro-stereolithography and two-photon lithography3D printingStronger electrodes and other reactor components.

△Located in the LLNL campus in Livermore, California. Photo courtesy of LLNL
Electrode3D printingIt is not a new concept, although it is still mainly limited to the academic field.Prior to this, a research team from Oak Ridge National Laboratory and the University of Tennessee had previously developed a complementary metal oxide semiconductor (CMOS) circuit3D printingElectrode method. Specifically, scientists use the Nanoscribe Photonic Professional GT two-photon polymerization system to nanoprint polymer structures directly onto semiconductor chips, where they can be carbonized.
In other respects, scientists have previously3D printingTo be able to detectfoodElectrodes containing mycotoxins paved the way for new ways to ensure food safety. This toxic metabolite is produced by the fungus Fusarium and can usually be found in corn products containing wheat, such as oatmeal.
(Editor in charge: admin)
0 Comments for “U.S. LLNL laboratory uses 3D printing technology to increase the performance of electrochemical reactors by more than a hundred times”