A new project underway at the University of Strathclyde has been awarded nearly £500,000 to develop small acoustic systems through additive manufacturing.The RESINators – Miniature Acoustic Resonator Systems project implemented by the University in partnership with the University of Glasgow is exploring the3D printingInstead of relying on electronic systems to create acoustic resonators formed from metamaterials.
“Our aim is to eventually develop cutting edge systems for personal audio, which may constitute the science of acoustic systems audio, the next generation of technology for wearable consumer projects,” said the project leader from Electrical and Electronic Engineering at the University of Strathclyde Dr. Joe Jackson said.
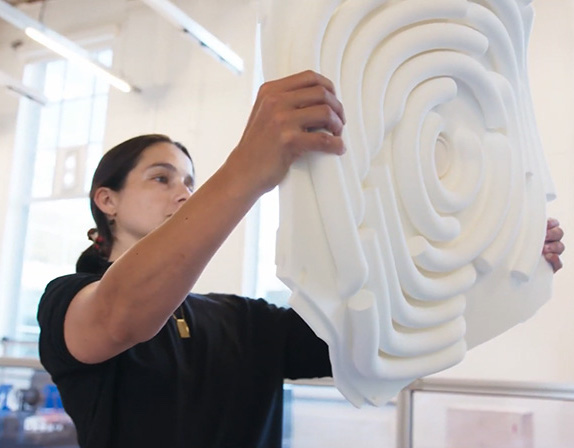
In the past, additive manufacturing has been used to develop sound enhancement and anti-counterfeiting properties for objects. Last year, Fraunhofer UMICSHT and Fraunhofer IBP 3D printed a fungus-based soundproofing device that can be used to create a new family of sustainable acoustic prototypes that outperform conventional products.
Elsewhere, 3D printing has been used to create amorphous shapes to improve guitar acoustics and enable complex underwater sonar applications.On the application of additive manufacturing in sound insulation, Delft University of Technology and
materialise
It has previously collaborated on the development of 3D printed sound-absorbing panels that can improve acoustics in concert halls and sports fields.
Acoustic system miniaturization
The three-year project is funded by the Engineering and Physical Sciences Research Council Department of UK Research and Innovation
funding
, will focus on creating metamaterials with superior acoustic properties that can form new acoustic systems with microscale features. The key to the project is to achieve acoustic functionality from simple, easy-to-build systems (rather than relying on electronics) by manipulating sound using 3D printing to create sound-optimized metamaterials.In the past, miniaturized acoustic systems such as wearable personal audio and
medical
equipment (such as hearing) has proven challenging and costly.
“Most of the research on the sound detection portion of external hearing aids and cochlear implants — an electronic device that electrically stimulates the cochlear nerve for hearing — involves electronics, such as signal analysis and digital signal processing,” Jackson said. “But that’s expensive. And battery life is required, and the more advanced the devices, the more impractical they become, for example, where users need to recharge their hearing aids every few hours.” The RESINators project seeks to study how sound works with acoustic resonators formed from metamaterials To address this challenge, metamaterials are a class of materials whose acoustic properties come from how they are built, not how they are built.
The metamaterials utilized in this project can be constructed in such a way that they produce acoustic properties not achievable with conventional materials, and can provide extremely effective noise suppression. Researchers are using 3D printing to build these complex geometric objects with microscale features that can form the basis of devices such as hearing aids. “It’s a challenge to miniaturize something that can be worn in a small area but still work with audio, so we’re looking to develop new acoustic systems with miniature features,” Jackson continued.
“They will operate at audio frequencies, and together they will drive advances in 3D printing and acoustic system design to create materials with superior acoustic properties, while still being lightweight and small-scale.” Dr Andrew Feeney of the University of Glasgow is working for the The RESINator program provides advanced materials expertise.
“Advances in our materials science and manufacturing capabilities have opened up new opportunities for acoustic devices,” he said. “We are now able to manufacture on a smaller scale than ever before, but more importantly, we can also detect the motion of these resonators using our advanced characterization facilities, which include non-contact instruments such as lasers.” As part of this project, our long-term experience in the development and characterization of advanced materials and devices has been researched with DR. Jackson. “
(responsible editor: admin)
0 Comments for “University of Strathclyde 3D prints new miniature acoustic system”