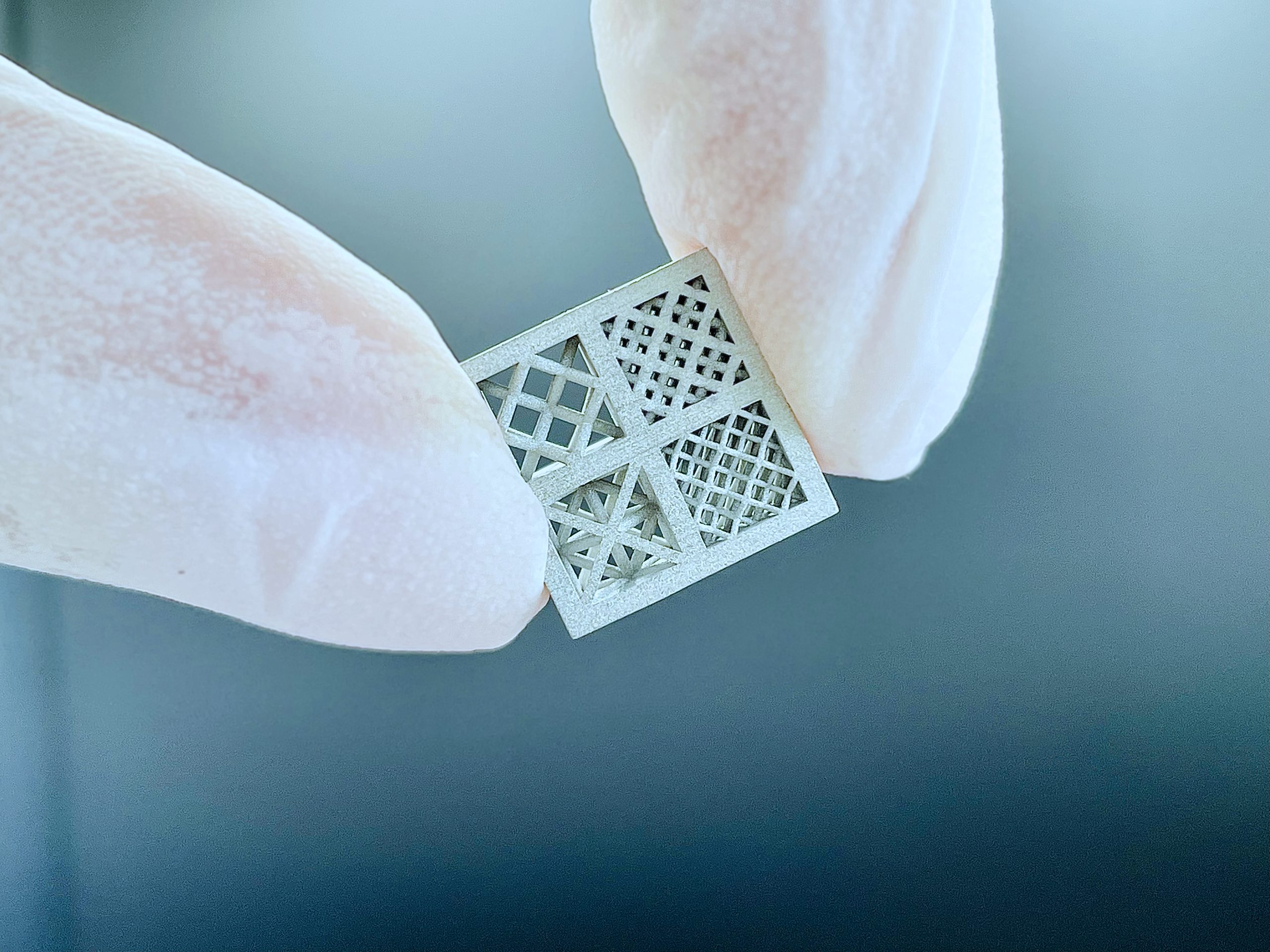
Incus’ LMM technology
After announcing the first release in March 2020, Incus entered mass production of the machine at the beginning of this year and continues to expand its customer base.
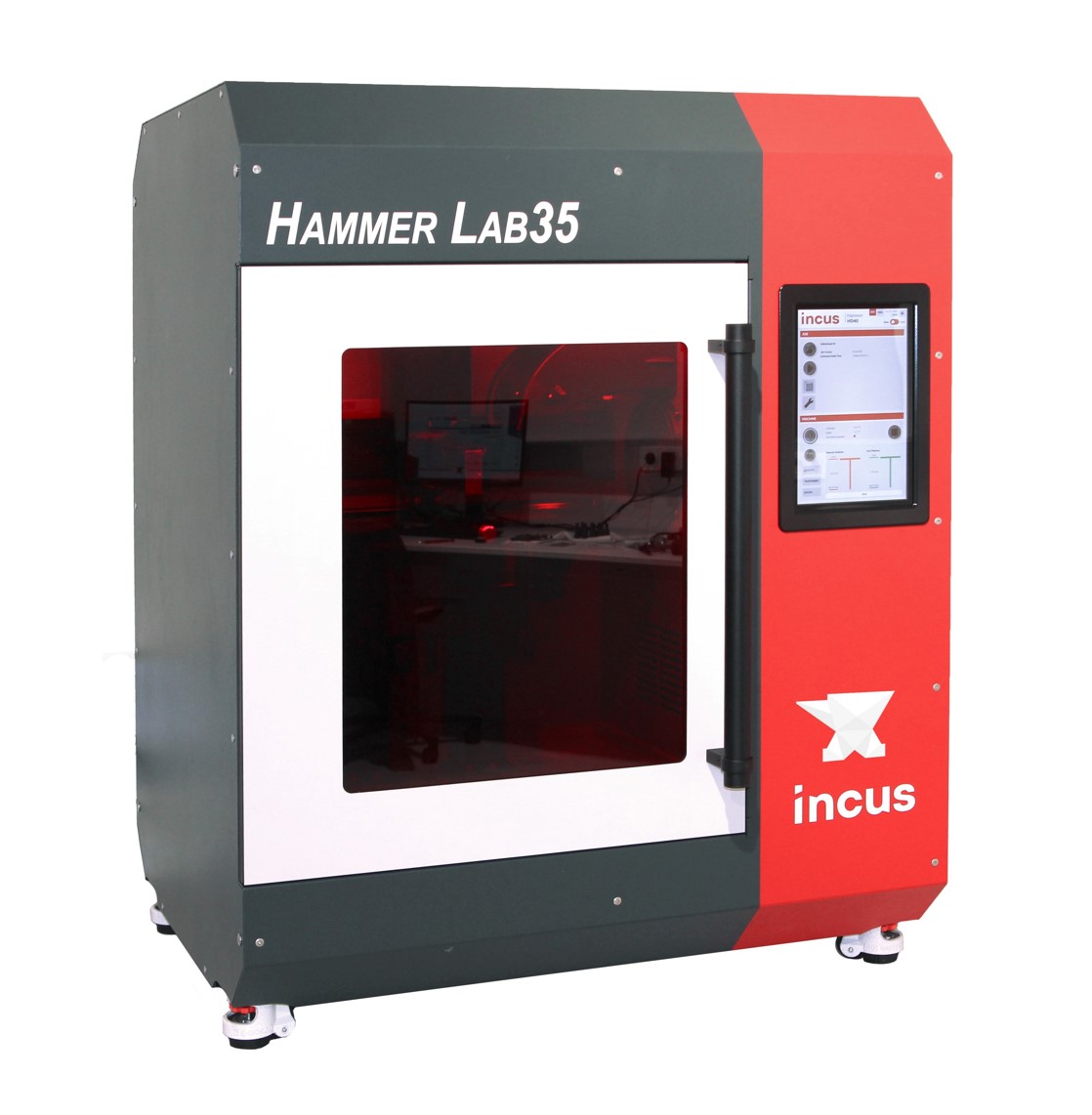
Use lunar scrap3D printingParts
The maintenance of lunar base stations requires continuous supply of goods, research materials and equipment. In addition, spare parts are needed to prevent individual components from failing during the mission.
The need for self-sufficiency in this task has prompted ESA to seek the feasibility of using existing lunar surface materials such as production waste and scrap parts. Being able to use this resource to manufacture on-board and on-demand spare parts for lunar spacecraft and space stations will help greatly reduce the cost and quantity of cargo missions departing from the earth, while minimizing production waste.
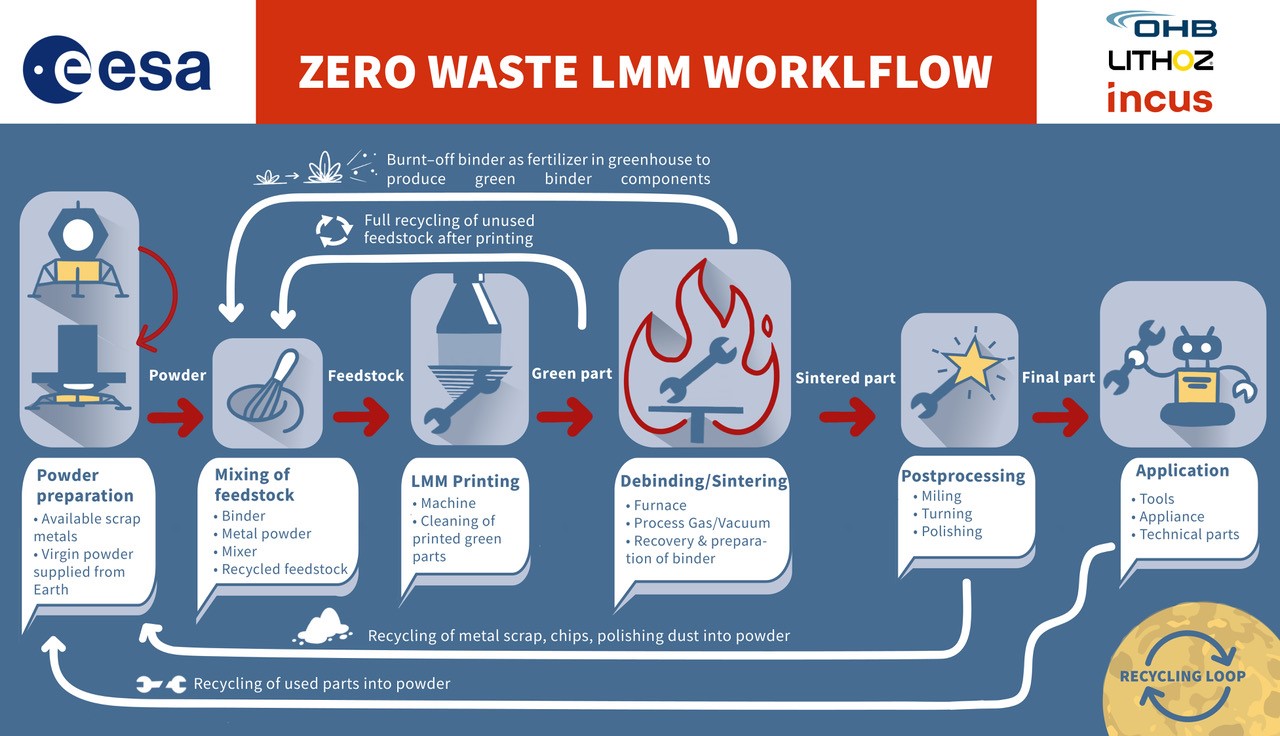
Incus’ LMM technology was selected for this project because of its ability to produce spare parts from recycled metal scrap.The partners hope that this ability may be applied to the moon.
mineral powder
Of recycling.
At the same time, the LMM process uses pastes or suspensions as raw materials and does not rely on the use of highly spherical gas atomized powders or supporting structures. On the contrary, the parts printed by this method are separated by a demolding process, no time-consuming manual rework is required, and it is also very safe for the operator.
Dr. Martin Schwentenwein, Director of Material Development at Lithoz, said: “The lithography technology developed by Incus and Lithoz allows high-precision3D printingCombined with high-performance metals and ceramics, while still maintaining extremely high resource efficiency. Although these concepts have been successfully demonstrated on the earth, the activities of such projects are essential to fill the technological gap and realize additive manufacturing in the space environment.”
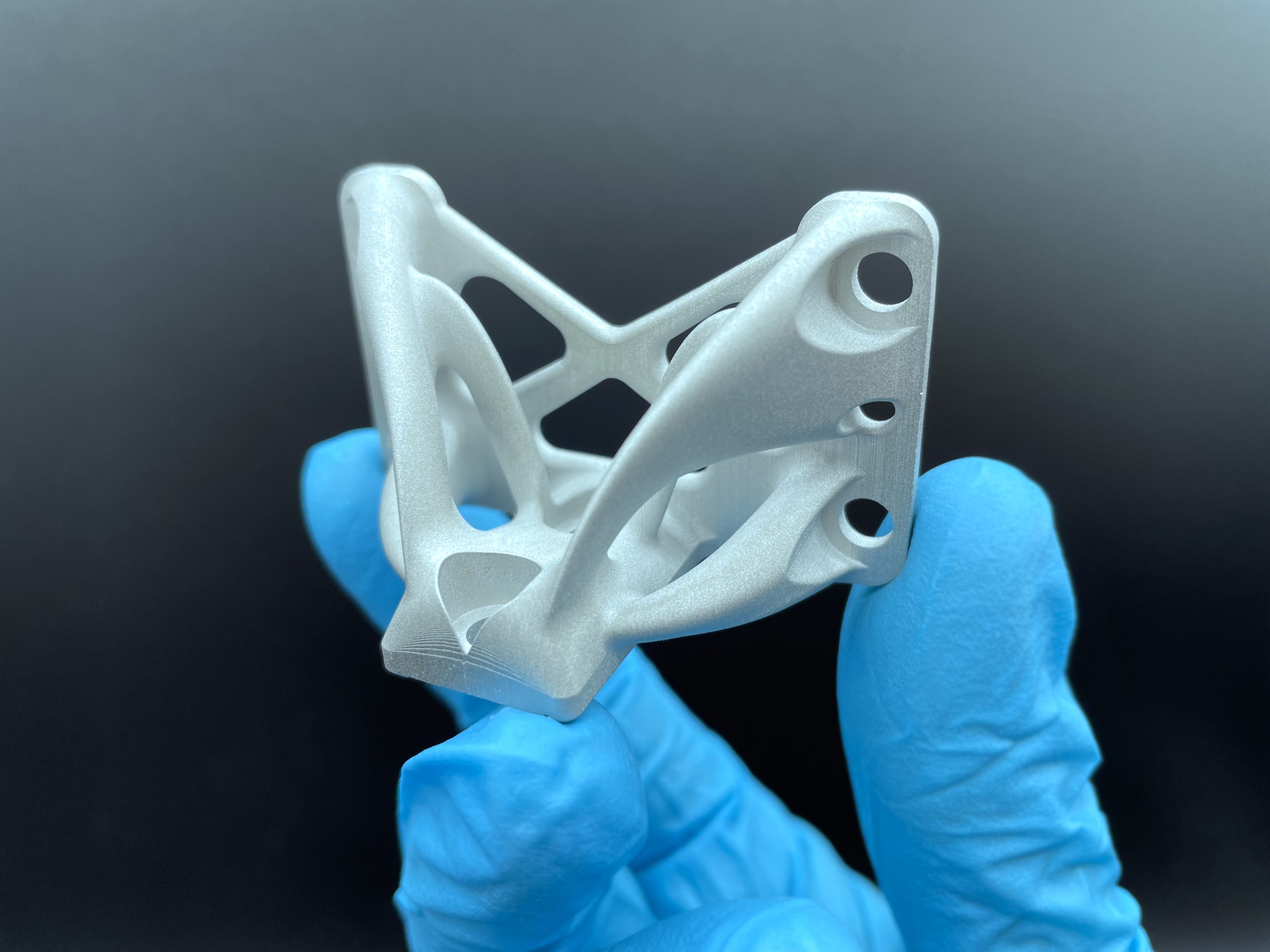
Using space materials3D printing
(Editor in charge: admin)
0 Comments for “Using lunar waste to print parts, Incus and the European Space Agency cooperate to unlock new capabilities in the light-curing LMM process”