November 5, 2021, Italy3D printingMachine manufacturer
WASP
Using natural materials, a unique beach store was built for the luxury brand Dior, filled with Dior’s latest merchandise.
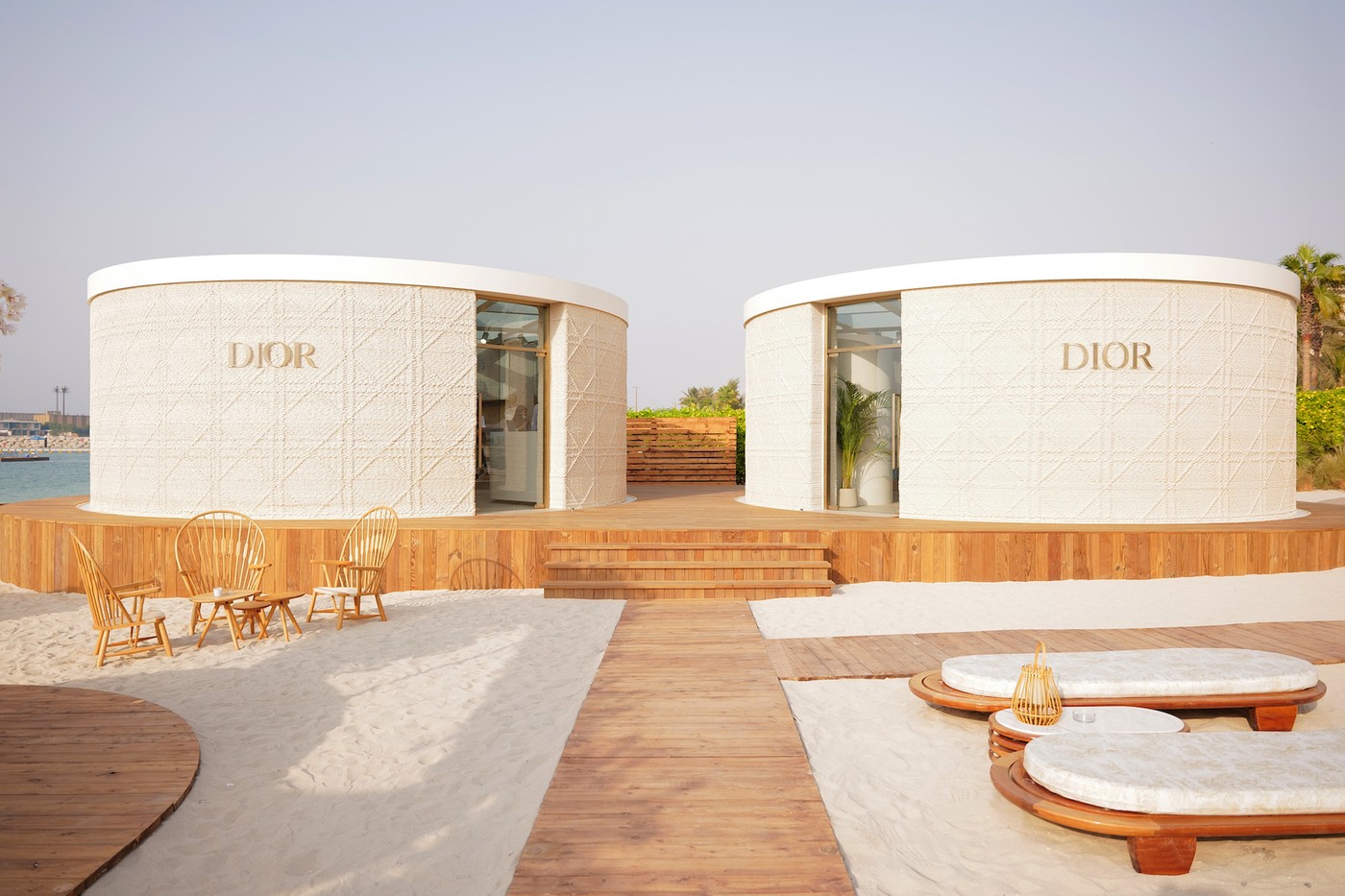
To build Dior’s beachfront boutique, WASP uses Delta 3D printingThe machine combines clay, sand and raw fibers into layers to form a stable (but brand-compliant) store. The exterior pattern of the store reflects the designer’s iconic leather bag and the backlit Dior pattern. Now the interior is filled with many luxurious items.
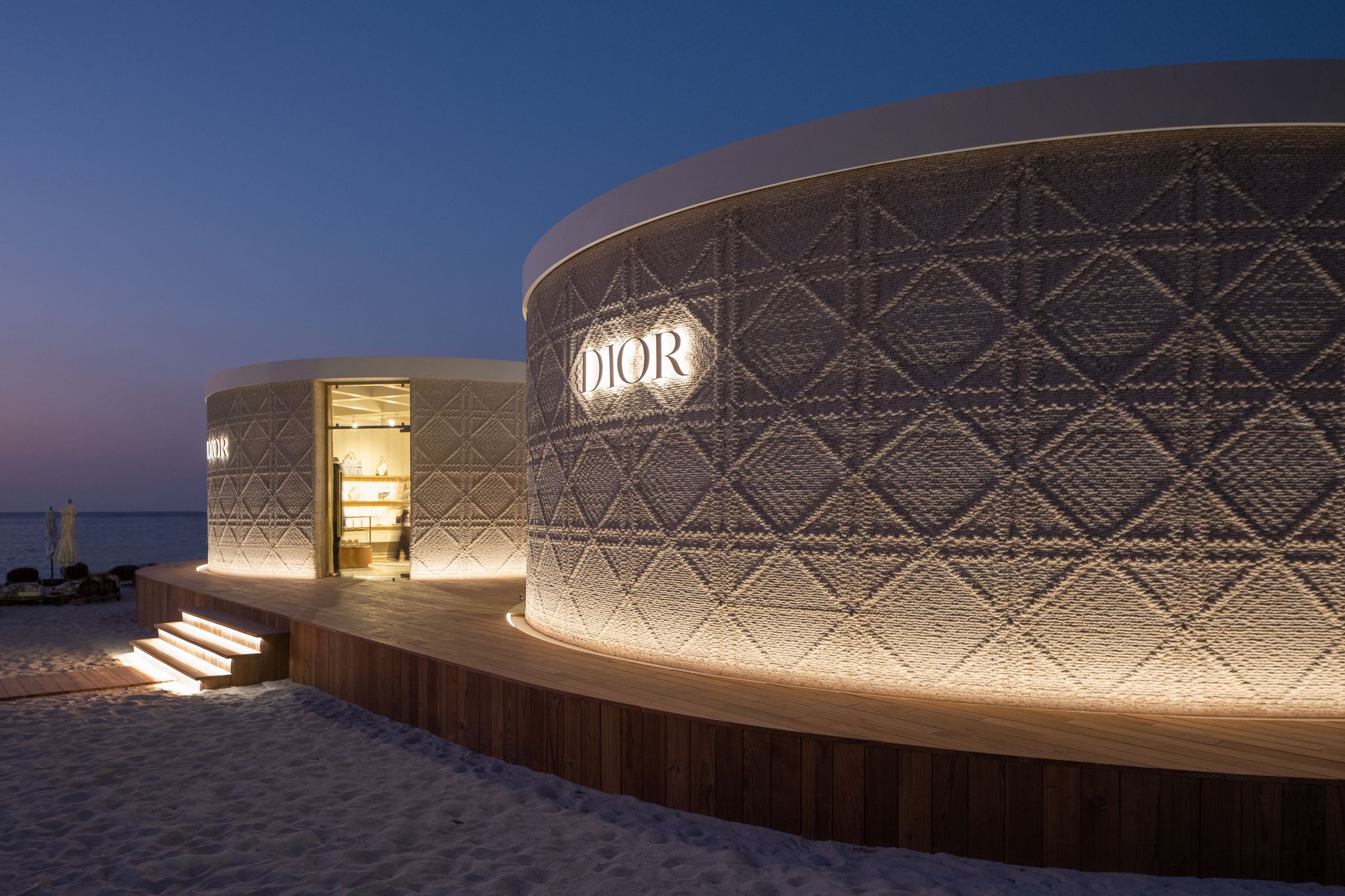
In addition to displaying beach essentials such as lounge chairs, parasols and cushions, the store also displays everything from gorgeous baskets to classic “school bags” and “caro” bags from fashion brands.
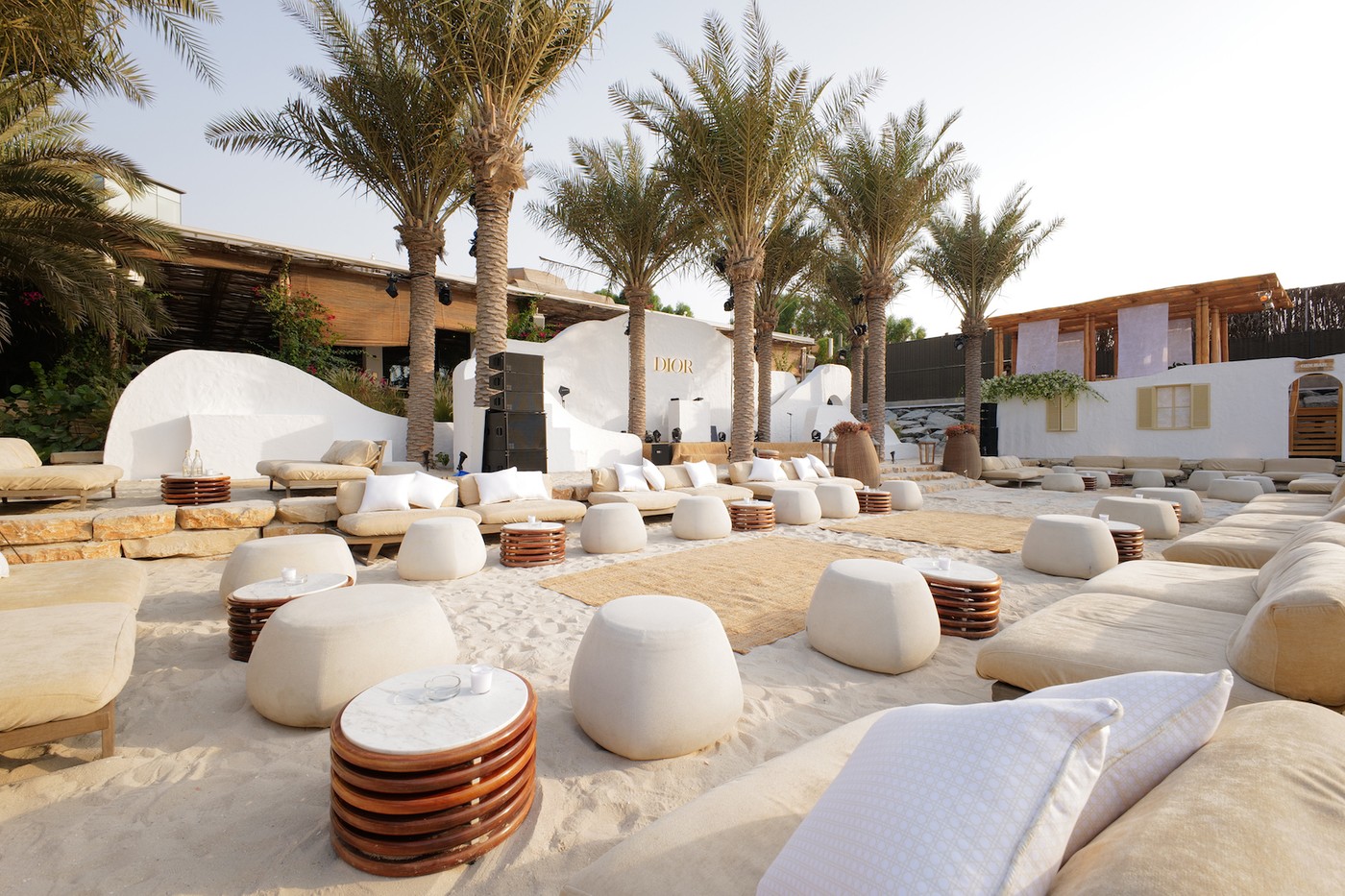
Moretti, the founder of WASP, wrote on his Facebook page: “Life is really strange. I developed a technology that hopes to provide everyone with a low-cost home. I have worked for it for ten years and self-funded. Do all the research and development. Then Dior came, a company representing the most exquisite luxury goods in the world, they asked us to print a store, and proposed
Funding
Our development costs. “
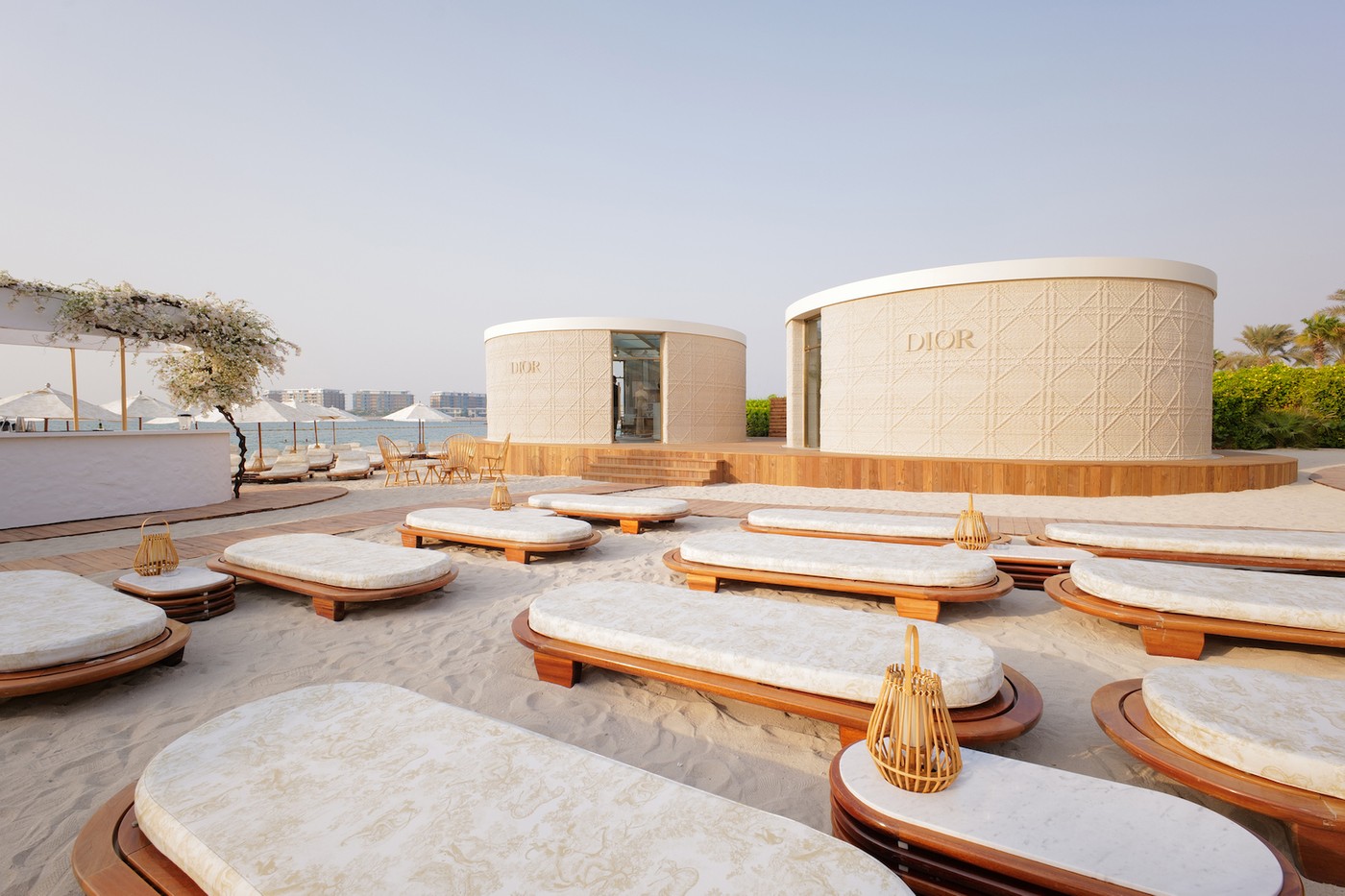
This year,
WASPAlso built a set
Eco-friendly3D printinghouses.
This fully assembled house is nicknamed “TECLA” and uses multiple3D printingSystem construction, each system deposits natural materials into a unique support structure.This novel additive manufacturing habitat was created by Mario Cuccinella, Italy
architecture
Designed by the firm, its construction is a proof of concept and a new sustainable
housing
Pattern blueprint.
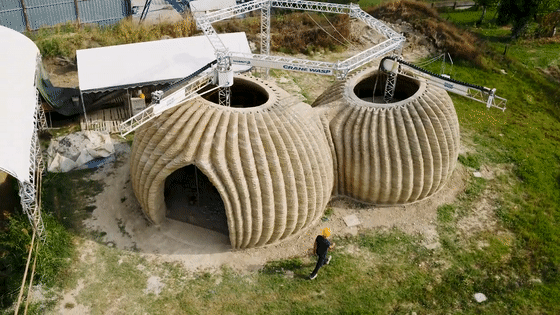
Mario Cucinella, the founder of Mario Cucinella Architects of the same name, said: “The completion of this building is an important milestone. Due to the use of design and technology, TECLA is no longer just a theoretical idea. Real and achievable response to needs.”
“TECLA is the realization of an unprecedented challenge, pushing printing geometry to the physical limit.”
WASP construction qualification
WASP was established in 2012 with a mission to develop digital manufacturing processes and promote circular economy.
The company’s recently launched machines include Delta WASP 4070 TECH and WASP 2040 systems for production, and WASP 3MT CONCRETE, which focuses on construction. In the past 18 months, WASP has also established a close cooperative relationship with Cucinella’s company. In this relationship, WASP has been seeking to find architectural applications for patented technologies.
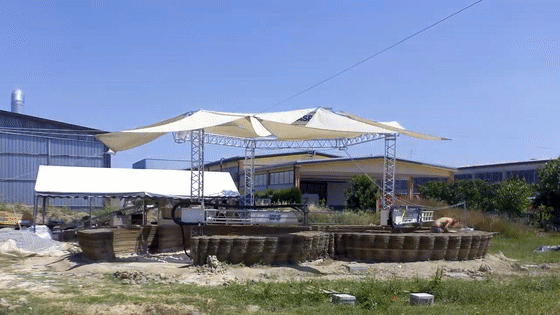
In October 2019, the two companies started planning the TECLA eco-house based on the research of architectural experts from the School of Sustainable Development. WASP is also working with the Building Society School of Architecture to determine how technology can be used to solve the problem of homelessness.
Putting these findings into action, WASP subsequently collaborated with Rossana Orlandi Gallery to utilize the Crane WASP system3D printing “Gaia” ecological building.
House
The shell is made of by-products of natural soil, and it took only ten days to print a wall of 20 square meters and 40 cm thick.
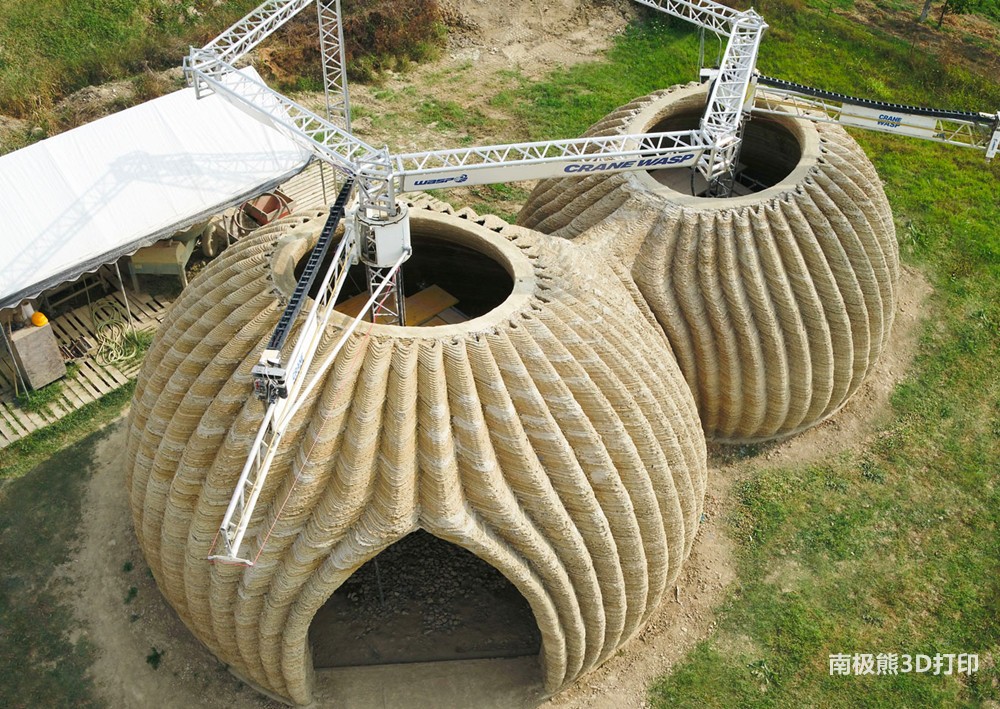
3D printingA sustainable habitat
Building on Gaia’s success, WASP now collaborates with Mario Cucincella to make TECLA using fully recyclable materials. The architect designed TECLA (a combination of technology and clay) based on the research of a long-term partner, and it is currently being built in the Massa Lombarda area in northern Italy.
Essentially, TECLA is a self-supporting, livable structure that can be made by stacking layers of reusable and recyclable materials (such as local soil). In theory, the resulting habitat is completely carbon-neutral and can adapt to any imaginable climate or condition around the world.
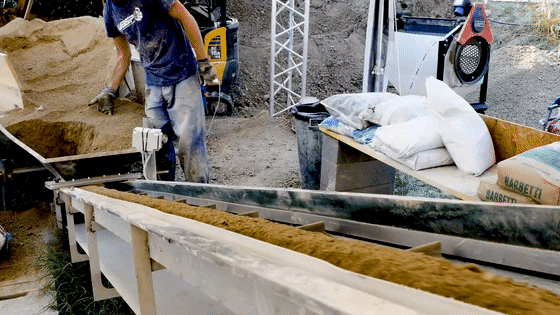
In order to turn the designer’s idea into reality, WASP deployed several Crane at the same time 3D printingMachine, which makes it possible to minimize the manual intervention required in the production process. WASP’s automated approach can also maximize the cost efficiency of the process while reducing
energy
Output, thereby increasing its ecological and environmental protection qualifications.
In the production process, two synchronized3D printingArm, and custom
software
Perform printing control without colliding with each other, so that materials can be picked, mixed and pumped.The simultaneous printing method was finally able to create a dome-shaped building in 200 hours, using 60 cubic feet of material and only 6 kilowattsenergy.
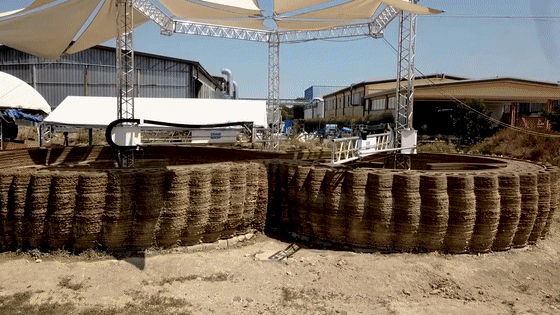
(Editor in charge: admin)
0 Comments for “WASP 3D printed two beach shops for luxury brand Dior”