ceramics
The material is widely used in structural materials due to its excellent corrosion resistance, low density and high strength properties.In addition, ceramic excellent
biology
compatibility attracts them in many organisms
medicine
Applications in applications such as bone substitutes, tissue engineering scaffolds,
dentistry
,
Operation
tools and instruments.
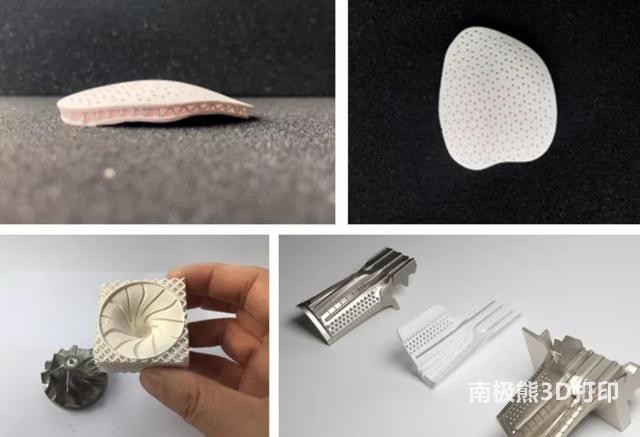
However, they show near-zero plastic deformation and low toughness due to limited fracture resistance. Even the slightest defect introduced during processing can greatly impair the strength and toughness of a ceramic. Therefore, even under ambient conditions, this inherent brittleness or poor toughening mechanism limits the application of ceramic materials in many structural components.
Currently, biomimetic concepts have been used to design engineered materials such as laminated glass and dual network hydrogels. In these structures, nature has overcome these limitations by developing ceramic matrix composites with an internally designed multiscale composite structure in which the optimized composition of hard minerals is layered with a “soft” phase.As a result, the combined advantages of high strength and toughness are achieved, making these structures useful for a variety of applications such as
car
windshield, hurricane protection
architecture
Windows, blast windows and synthetic connective tissue. Nonetheless, this particular concept can be further expanded to develop innovative material designs in terms of structural arrangements and/or configurations.
Specifically, damage tolerance through simple and cost-effective encapsulation of polymer films in ceramic-based structures while ensuring impermeability or composite formation has not been achieved. Although the purpose of using molten glass glaze in traditional ceramics is to fill surface cracks and obtain a smooth surface, this coating does not improve the inherent brittleness of the structure, if not deteriorate.
In this paper, we use3D printingDamage-resistant ceramic-polymer composites were efficiently prepared.
The mechanical properties of the coated/uncoated structural ceramics were compared and analyzed by uniaxial compression test; the process of crack initiation, propagation and stoppage of the structure under different compressive loads was studied by in-situ micro-computed tomography (micro-CT). .
On this basis, the finite element method based on the continuous plastic damage model is used to study the damage propagation law of polymer coating on structural ceramics under compressive load.
In addition, the authors performed atomic modeling to reveal the strengthening and toughening mechanisms of epoxy-coated ceramics under uniaxial compressive loading.
Finally, we analyze printed ceramic samples of different architectures and geometries to reveal the applicability of the coating to general materials.
Graphic analysis
1. Preparation and Morphology of Materials
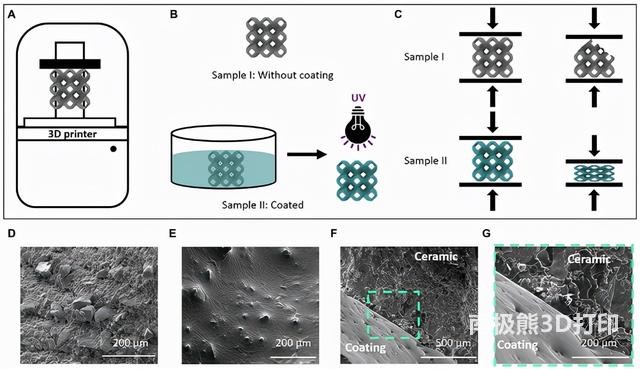
1- Diagram:
(A) Ceramic samples were printed with an SLA 3D printer. (B) Sample I (uncoated ceramic) was used3D printingfabricated without any further treatment; sample II (coated ceramic) was dipped in epoxy and exposed to UV light to cure the epoxy and form a thin conformal coating over the entire surface. (C) Schematic diagram of a quasi-static compression study of two samples. Sample I failed catastrophically, while sample II showed layer-by-layer deformation and progressive failure. (D) SEM image of the surface topography of the uncoated ceramic. (E) SEM image of the surface topography of the coated ceramic, showing the uniformity of the coating. (F and G) SEM images of cross-sections showing the morphology of the polymer-ceramic interface and coating thickness (70–100 μm) at low and high magnifications.
2. Mechanism of improving the strength of the material by the polymer coating
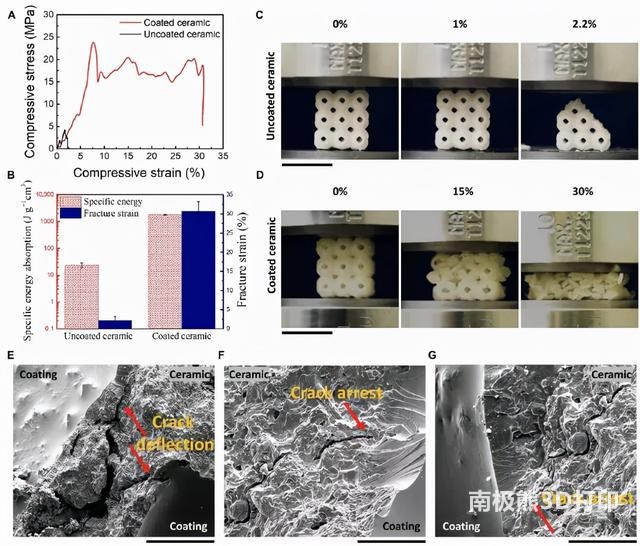
2- Diagram:
(A and B) Stress-strain behavior in quasi-static compression of uncoated and coated ceramic specimens. It shows that the dip-coated ceramics after epoxy resin effectively enhance the strength and toughness of the structural material, and the epoxy resin coating improves the compression toughness of the specimen. (C) Catastrophic failure process of uncoated ceramics at low strain values; scale bar is 1 cm. (D) Gradual failure process of the coated ceramic through layer-by-layer deformation; it explains the effect of the coating, a phenomenon uncommon in brittle materials such as ceramics; scale bar is 1 cm. (E) SEM showing crack deflection in the coated ceramic after compression testing; scale bar is 500 um. (F and G) Crack initiation and propagation through the inner and outer “hard phases” of the coated specimen, and crack cessation is observed in the ceramic-polymer interface, as indicated by the red arrows; scale bar is 200 um.
3. In situ CT to explore its toughening mechanism
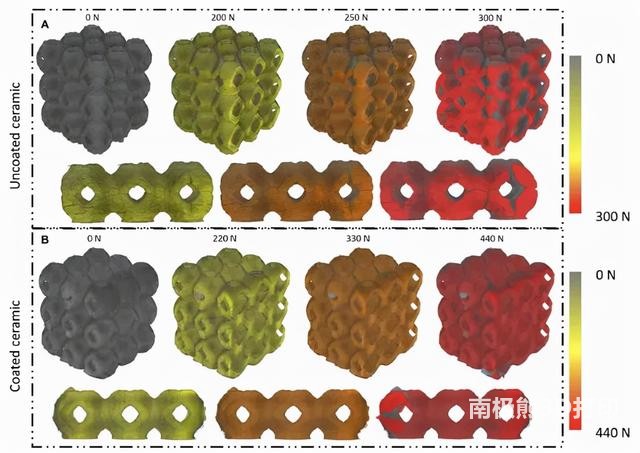
3- Diagram:
(A) CT scan images of uncoated ceramics at different loading levels, with the loading increasing from grey to red. Higher magnification images show how the cracks grow and connect to each other at increasing load levels. (B) CT scan images of coated ceramics at different loading levels. The results show the effectiveness of the coating on crack propagation of ceramic specimens under different loads.
4. Finite element analysis of the shaping zone
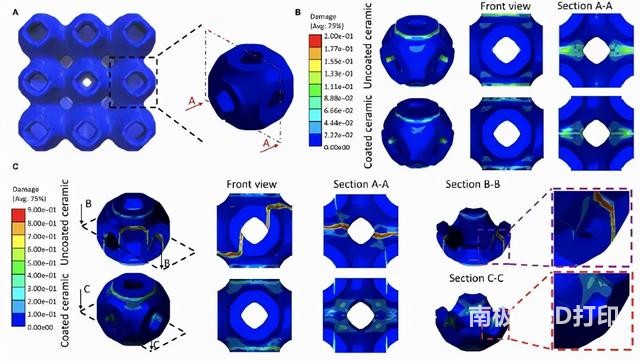
4- Diagram:
(A) Finite element analysis comparison, taking structural elements, calculating principal stress and strain. For better presentation, the cells are cut in the middle. As can be seen from the figure, the damage profiles of the coated and uncoated samples are shown at (B) low strain (about 0.7%) and (C) at high strain (about 1.75%), which show that at low strain, The damage profiles of the coated and uncoated specimens were similar; however, at high strains, the damage of the uncoated ceramic was much greater than that of the coated specimen. This is similar to the previous result.
5. Simulation analysis of ceramic materials
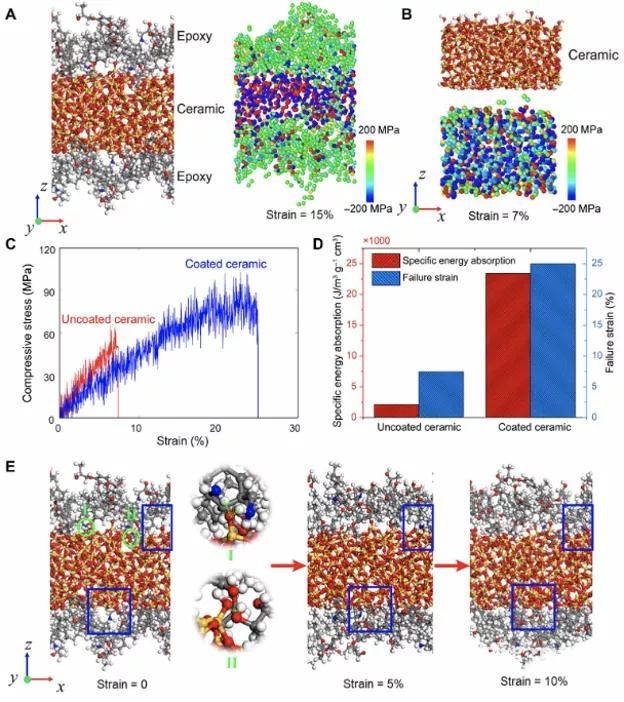
5-Illustration:
Atomic model comparison of mechanical properties simulation under uniaxial compression. (A) Atomic structure and stress distribution of epoxy-coated ceramics under uniaxial compression in the x-direction. (B) Atomic structure and stress distribution of uncoated ceramics under uniaxial compression in the x-direction. (C) Stress-strain curves of coated and uncoated ceramics. (D) Specific energy absorption and failure strain of uncoated and coated ceramics. (E) Snapshot of epoxy-coated ceramic under uniaxial compression. The circular inset in the second panel shows the two types of hydrogen bonds that form between the epoxy and the ceramic (enlarge the green circled area in the first panel). The upper inset shows the hydrogen bond between -NH2 and -OH, while the lower inset shows the hydrogen bond between -OH and -OH. The results show that the blue rectangles and squares highlight the evolution of the interfacial interactions of the epoxy coating during compression, during which the epoxy coating fills the ceramic surface defects, effectively reducing stress concentrations.
summary
Although ceramic materials have high strength and modulus, their application in many structures is limited due to their inherent brittleness and low toughness. However, ceramic-based structures, using bottom-up assembly of complex layers of hard ceramics and soft polymers, inherently overcome this drawback.
Here, we propose a much simpler approach to fully act as an exosoftening phase on the constructed ceramic structures via a conformal polymer coating, leading to damage tolerance.
The results show that the polymer coating structure has multiple improvements in compressive strength and toughness, while resisting catastrophic failure through crack propagation delay. More damage resistant than conventional ceramic parts, this surface modification method can be a simple strategy to fabricate complex ceramic parts.
(responsible editor: admin)
0 Comments for “What should I do if the ceramic material is easily damaged? 3D printed polymer coating”