Guide: On July 30, 2021, the sports performance brand Vorteq passed and Luxembourg’s3D scanninginstrumentThe manufacturer Artec 3D has collaborated to create customized aerodynamic skin suits for cyclists. Using a combination of Artec’s Leo 3D scanner, wind tunnel and engineering design, Vorteq designed what it claims is one of the “fastest” bicycle leather jackets in the world. The highlight is that in this year’s Tokyo Olympics, five different Olympic athletes have already put on this leather jacket. Because of its lightweight and breathable design, it can greatly reduce resistance.
SamQuilter, a metrology engineer at Vorteq, said: “Our mission is to help athletes break through themselves, many of whom have reached or are close to their peaks. Although what we do can only promote small improvements, when you add them together, It can really bring that kind of advantage to athletes and help them surpass the peak and move towards victory. Compared with our previous scanners, Leo provides us with this flexibility, which can scan almost anywhere in the world without additional The hardware only needs Leo itself. When you go to any location outside, it will provide a greater advantage of freedom, because these locations are not completely laboratories in terms of conditions.”
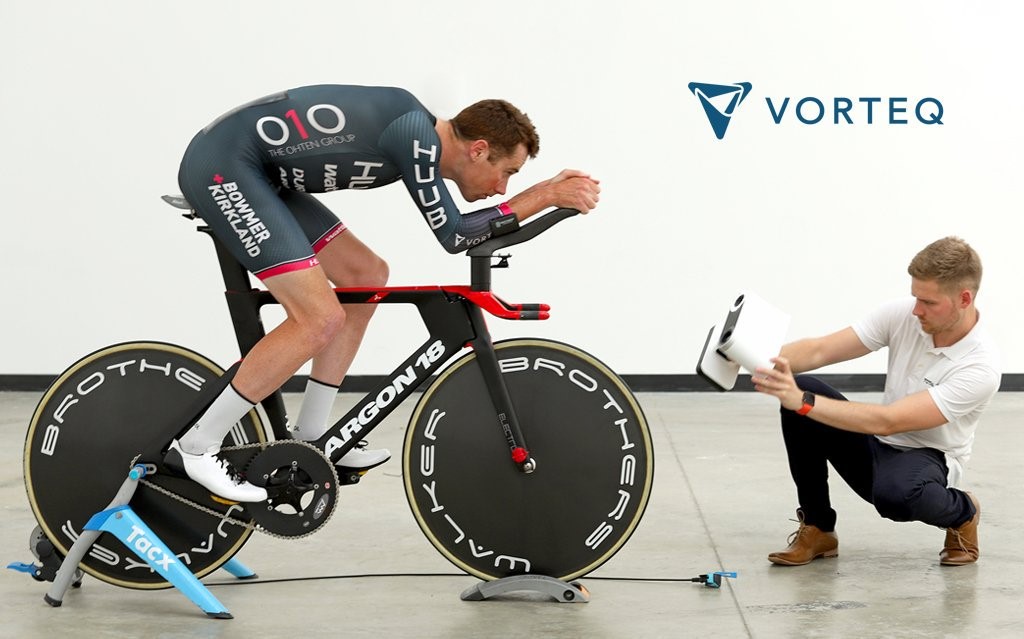
△Metrology engineer Sam Quilter used Artec Leo to perform3D scanning. Picture from Vorteq
Arctec 3D scanning
Artec 3D’s product line includes Eva, Space Spider, Leo and Ray scanners for a variety of different purposes.3D printingContinuous finalist for industry awards. Their company’s scanner was used in the reverse engineering of parts of MarinebedrijfKoninklijke Marine, a material and asset maintenance company for the Royal Netherlands Navy, and Triebold Paleontology’s digital preservation of the 26-foot stegosaurus in the Denver Museum of Nature and Science.
Artec’s scanners are also usedcarThe industry’s vehicle repairs and the creation of full-body 3D scans of dolphins, sharks and large sea turtles to create customized tracking tags that provide information on migration patterns and the effects of ocean temperature.
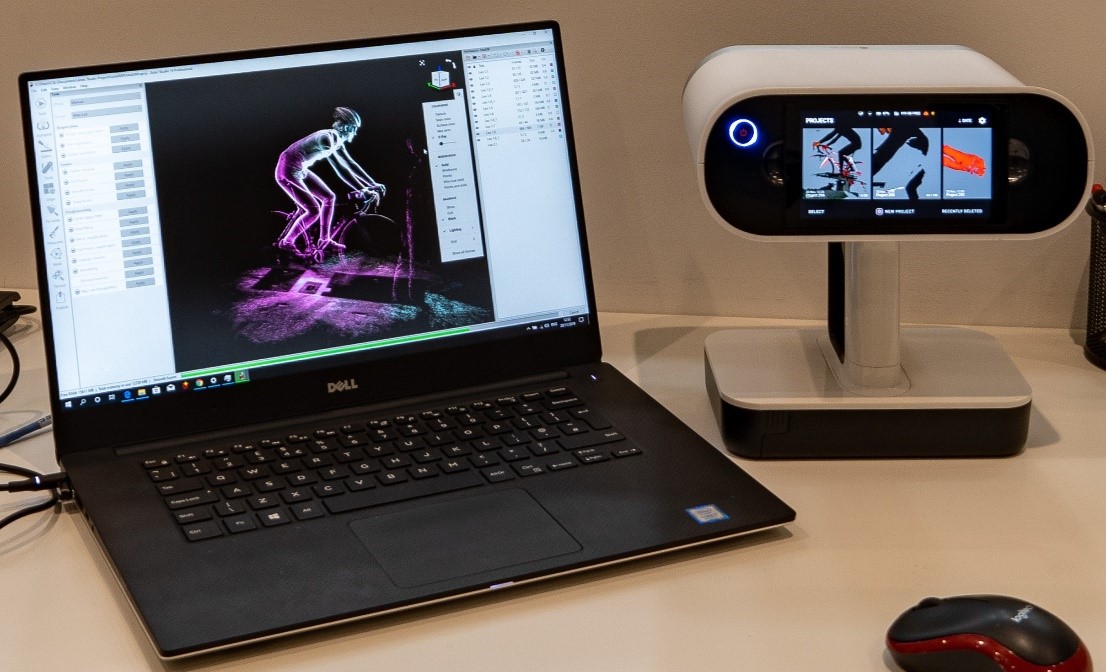
△ArtecLeo 3D scanner and Artec StudiosoftwareA scan of the rider is displayed at the Silverstone Sports Engineering Center. Picture from Vorteq
Aerodynamics and3D scanningPerfect use of
In the world of high-level cycling, speed is everything, and success and failure are often only between a fraction of a second. On the track, the cyclist struggles with wind resistance and resistance every time the pedal turns. It is said that 90% of the energy output of the cyclist is used to overcome the air resistance, so reducing this resistance is the key.
Vorteq uses the sport-specific wind tunnel and fabric wind tunnel of the Silverstone Sports Engineering Center (SSEH) and the latest3D scanningTechnology to create customized skin suits for cyclists to reduce this air resistance while also being comfortable, light and breathable.
Artec 3D’s Artec Leo handheld scanner is a key factor in the design of skin garments. It can digitally capture the precise anatomy of the rider in less than 6 minutes. The scanner has a built-in touch screen and a capture rate of 44 frames per second, capable of scanning medium-sized objects, including people, in a matter of minutes.
“The rider took their bike into the wind tunnel, installed it on the platform, and jumped on it. In just five to six minutes of working with Leo, I captured the rider’s two images in precise, high-resolution color 3D. Location,” Quilter said. “Basically, this means that within ten minutes, I can complete the rider’s job, and they can go elsewhere. I have got everything I need to design an anatomically accurate, lightning-fast Vorteq skin is installed and does not need to be rescanned.”
When making skin garments, Vorteq works directly on ArtecLeo’s scan results, which provide accurate body data of athletes to eliminate inaccurate and inaccurate measurements. The scan results are then post-processed in Artec’s Studio software. Engineers can carefully examine the data and eliminate any rare inaccuracies or unwanted data captures, such as wrinkles.
Quilter continued: “From the moment the athlete enters the door to when we start scanning with Leo, we use Artec Studio to post-process the scanning results, then perform 3D modeling in Geomagic Wrap, and finally export the 3D model to make the skin coat. It takes 2 hours, which was absolutely impossible or even impossible in the past. As for the total production time of a skin suit that can be used for competitions, we are currently 2 days, but this gap is narrowing, and we are working hard. Achieving a 24-hour turnaround time, we will definitely achieve this goal in the near future.”
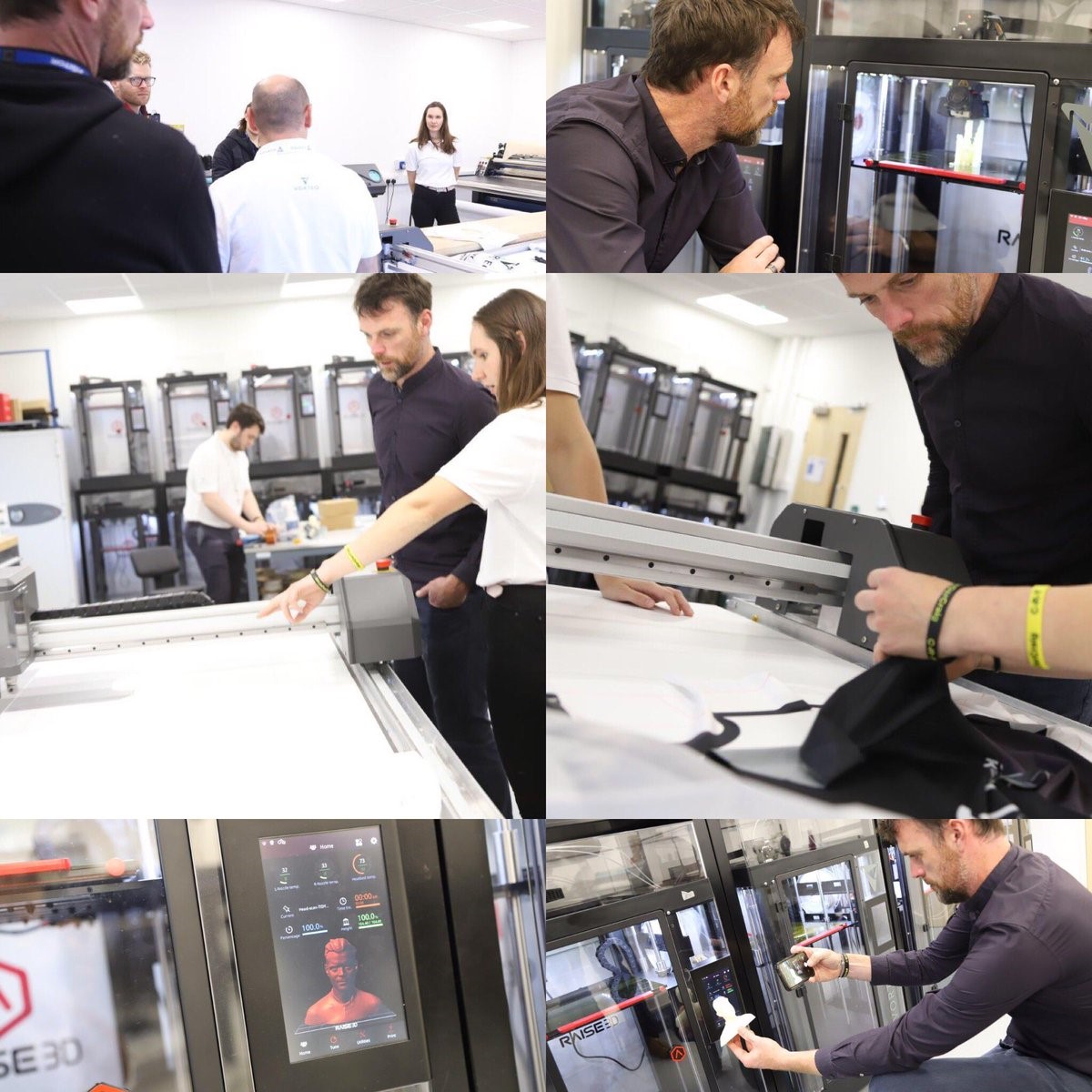
△Design and create Vorteq skin outfits. Picture from Vorteq
Using Artec Leo, Vorteq can also3D printingAnatomically accurate models of athletes can be used to make skin suits for them without the need to try on them. The mannequin allows Vorteq to create customized skin suits for athletes, test a variety of fabrics and patterns in its wind tunnel, and make skin suits in the next few hours, and then deliver them to the athlete’s door.This process currently takes less than two days, although the company hopes to accelerate this process from3D scanningWithin 24 hours of completion.
Quilter explained: “A full-scale mannequin allows us to perform wind tunnel tests on fabrics individually on an arm. For example, see how various fabrics and patterns affect the reduction of resistance. This is where the marginal benefit really increases. .Because for the real rider in the wind tunnel, there will be swing factors that need to be dealt with, that is, the rider moves around, even a slight movement will affect the result. For a real rider, you can never be in a completely stationary human body Accurate measurements are obtained on the model, and the only factor that changes is the fabric worn.”
Previously, Vorteq only cooperated with the Olympic team and other elite athletes, but since early 2020, the company’s customized skins have been provided to cyclists of all levels, enabling them to perform at their best.
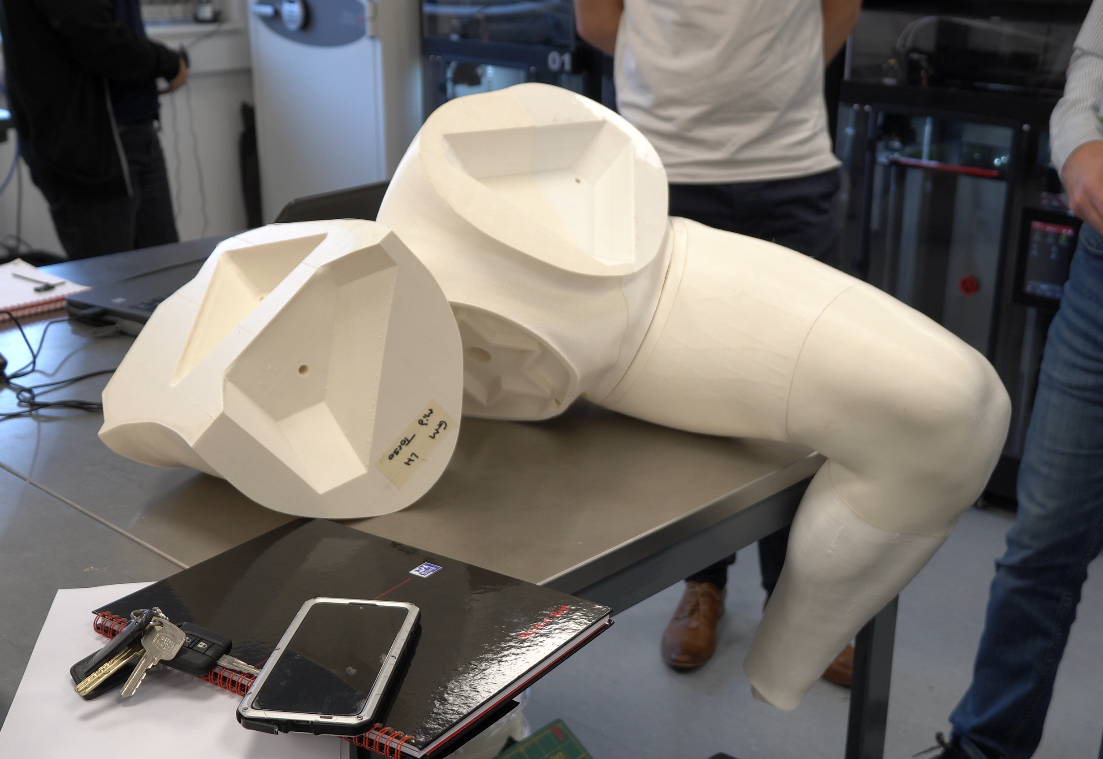
△Vorteq mannequin components are ready for assembly and wind tunnel use. Photos from Vorteq
when3D printingMeet the Olympics
Previously, many Olympic athletes have turned their personalized equipment to save time, weight, or other benefits.3D printing.For example, Shelly-Ann Fraser-Pryce’s3D printingRunning shoes were exhibited at the last Rio de Janeiro Olympics, and Adidas and3D printingMachine manufacturer Carbon’s latest3D printingThe 4DFWD midsole is currently worn by some athletes at this year’s Tokyo Olympics.
Previously, the French Bicycle Association has deployed custom handlebars, using3D printingTechnology produces an increase in aerodynamic efficiency, a global engineering companyRenishawIn cooperation with Lotus Engineering Company and Hope Technology Company, a new track bike was designed for the British Cycling Team.
Recently, the Italian National Cycling Team revealed that it has used the Calibry 3D scanner from Thor3D, a Russian handheld 3D scanner developer, to improve its aerodynamic performance before the Tokyo Olympics.
(Editor in charge: admin)
0 Comments for “When 3D printing meets the Olympic Games, Artec Leo 3D scanning technology will produce “the world’s fastest” bicycle leather jackets for Olympians”